-
01 Capabilitiesof 5-axis machining
centers and
multitasking machines -
02 Why Okuma is chosenOkuma, a manufacturer of
5-axis machining centers
and multitasking machines -
03 Case studiesof installing 5-axis
machining centers and
multitasking machines. -
04 Lineupof 5-axis machining
centers and
multitasking machines -
05 Q&Aabout 5-axis machining
centers and
multitasking machines
05
Q&Aabout 5-axis machining centers and multitasking machines
Basics of 5-axis Machining Centers
What is a 5-axis machining center?
This is a machining center to which 2 rotary axes have been added to the 3 linear axes, and is capable of performing multi-face machining with a single setup.
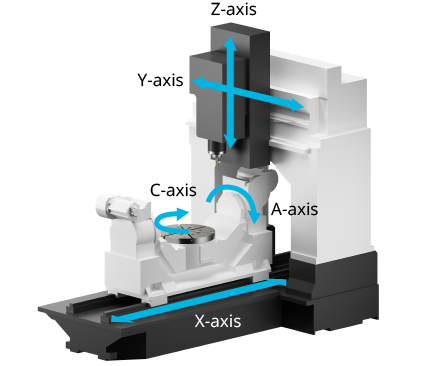
What kind of machining is possible with a 5-axis machining center?
5-axis index machining and simultaneous 5-axis machining are possible. 5-axis index machining is used for parts with multiple surfaces, and simultaneous 5-axis machining is used for parts with free-form surfaces.
5-axis index machining
- Machining with 3 linear axes at angles adjusted with 2 rotary axes
Multi-face machining
Simultaneous 5-axis machining
- Machining performed while moving 5 axes simultaneously
Free-form surfacing
What are the merits of adopting a 5-axis machining center?
Multi-face machining can be performed by carrying out setup only once, which allows less jigs to be required. Also, high machining accuracy can be maintained by minimizing variations in accuracy that can occur when mounting workpieces.
3-axis machining
Setup is performed multiple times, leading to drops in machining accuracy.

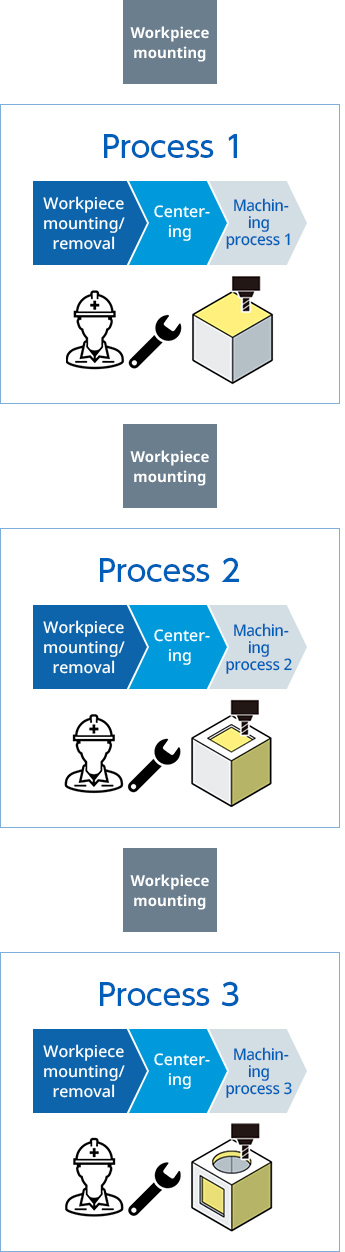
5-axis machining
Setup is performed only a few times, allowing high machining accuracy to be maintained.
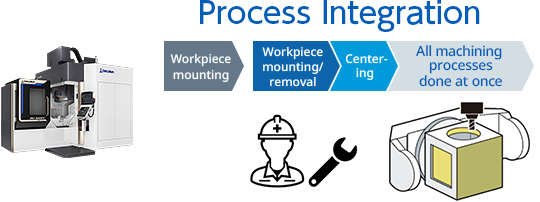
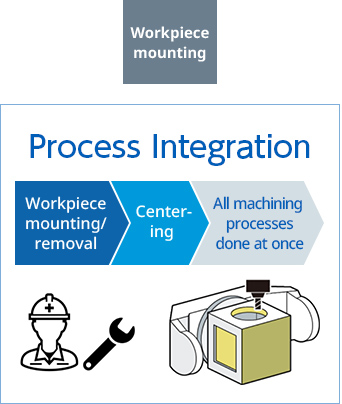
- Shorter production lead time by reducing setup and transfer work
- Labor savings achieved by reducing number of times setup performed
- Reduced running costs such as electricity
- Minimization of variations in accuracy with multi-face machining requiring only single setup
- Flexible response to changes in workpiece type and qty with diverse range of tools
- Shorter tool protrusion for improved surface quality
- Reduced jig costs
What processes can be integrated with a 5-axis machining center?
Milling, turning, gear cutting, grinding, and gauging processes can be integrated into a single machine (incl. options, also).
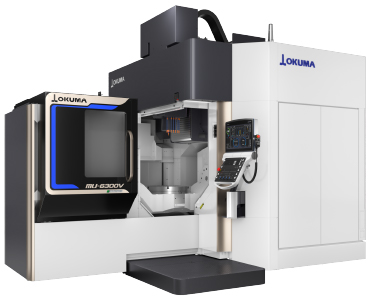
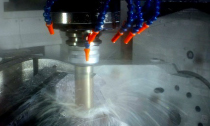
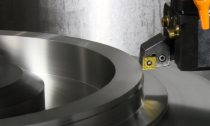
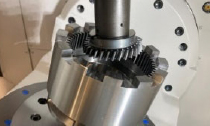
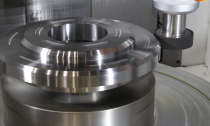
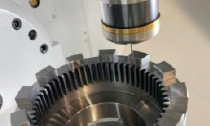
* Specifications other than milling are optional.
How do I choose a 5-axis machining center?
A 2-axis rotary table with outstanding productivity is perfect for small to medium-sized parts, a single-axis rotary table that does not tilt workpieces and single-axis rotary spindle are perfect for medium to large parts, and a stable 2-axis rotary spindle is perfect for large parts.
Applicable parts | Small to medium-sized parts | Medium to large parts | Large parts |
---|---|---|---|
Rotary axis | 2-axis on the table side | 1-axis on the table side, 1-axis on the spindle side | 2-axis on the spindle side |
Structural drawing | ![]() |
![]() |
![]() |
Features | The spindle has no rotary axes, allowing a high-rigidity spindle similar to that on 3-axis machining centers to be mounted. | The table does not tilt, allowing high-speed, high-accuracy positioning even for heavy medium to large parts. | The table does not tilt or rotate, allowing high-speed, high-accuracy positioning for even heavier large parts. |
Applicable parts:Small to medium-sized parts ![]() The spindle has no rotary axes, allowing a high-rigidity spindle similar to that on 3-axis machining centers to be mounted. |
Applicable parts:Medium to large parts ![]() The table does not tilt, allowing high-speed, high-accuracy positioning even for heavy medium to large parts. |
Applicable parts:Large parts ![]() The table does not tilt or rotate, allowing high-speed, high-accuracy positioning for even heavier large parts. |
What is the difference between the MU-100V series and MU-1000V series?
The MU-100V series is capable of high-accuracy 5-axis machining in the same space as a 3-axis vertical machining center.
The MU-1000V series is capable of high-accuracy, high-efficiency simultaneous 5-axis machining. Process integration is also possible with turning.
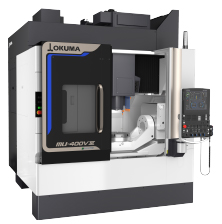
5-axis machining in same minimal space as 3-axis vertical machining center. Perfectly suited for step up to 5-axis machining. |
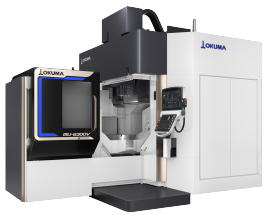
High-accuracy, high-efficiency simultaneous 5-axis machining. Turning (option) can also be integrated, making it perfect for improving 5-axis machining productivity. |
About Machine and Machining Capability
I'm worried about whether a 5-axis machining center will fit in my factory.
The MU-100V series can be installed in the same space as a 3-axis vertical machining center.

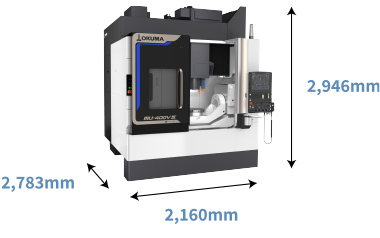

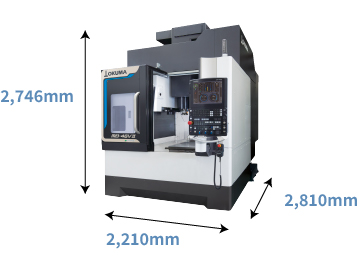

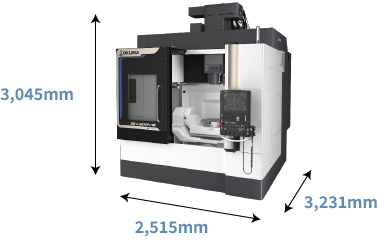

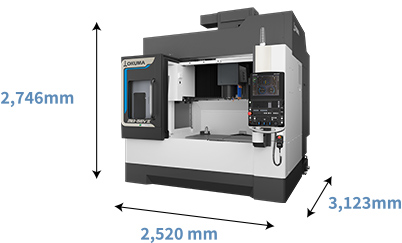
The complex structure of 5-axis machining centers makes me wonder whether I can carry out the same machining work as I can with a 3-axis machining center.
Productivity is improved with the same high machining capability as 3-axis machining centers.

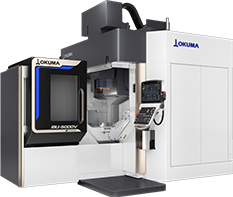
ø20 end mill machining capability |
672cm³/min |

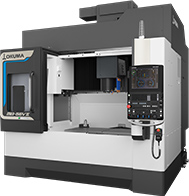
ø20 end mill machining capability |
672cm³/min |
Results obtained machining S45C workpiece
I want to know the machining accuracy of 5-axis machining centers.
5-axis machining centers offer the same level of stable machining accuracy as 3-axis machining centers.
5-axis machining centers

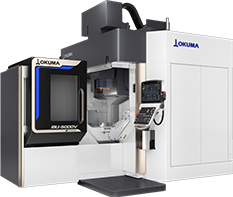

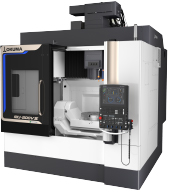
Thermal deformation over time | Thermal deformation over time |
7 μm or less | 7 μm or less |

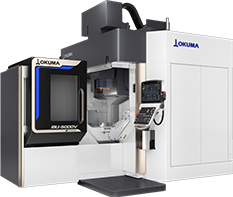
Thermal deformation over time |
7 μm or less |

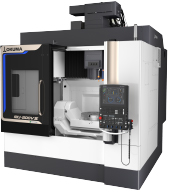
Thermal deformation over time |
7 μm or less |

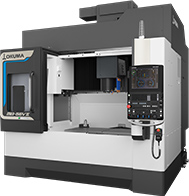
Thermal deformation over time |
7 µm or less |
(actual data obtained at environmental room temperature change of 8 °C)

Thermo-Friendly Concept
Based on Okuma's unique concept of "accepting temperature changes",
stable accuracy is realized in a normal factory environment even without operators being aware.
Based on Okuma's unique concept of "accepting temperature changes", stable accuracy is realized in a normal factory environment even without operators being aware.
The complex structure of 5-axis machining centers makes me worry about whether machining accuracy will deteriorate with use?
High machining accuracy can be maintained using functions to gauge and compensate axis position and tilt error.

5-Axis Auto Tuning SystemⅡ
- High accuracy maintained by compensating axis position and tilt error with simple operation.
- Troublesome manual tuning work reduced.
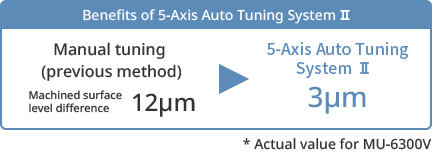
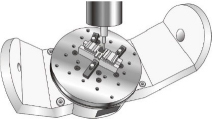
I want to machine dies/molds and free-form surfaces with higher quality.
By automatically compensating command trajectories output from CAM, surface quality can be improved while reducing machining time.
The complex structure of 5-axis machining centers makes me worry about collisions occurring during machine operation.
The Collision Avoidance System allows operators to operate machines without having to worry about collisions, and to focus on machining with peace of mind.

Collision Avoidance System
Automatic operation
- NC program is read in advance to check for collisions.
Machine stops before collision occurs.
Manual operation
- Operation is stopped immediately before collision even when performing manual operation
during setup work.
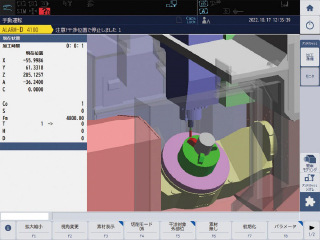
It looks difficult to create machining programs for 5-axis machining centers.
Programs for indexed machining can be created easily interactively.
Interactive programming
Index the machining surface, and specify zero setting interactively with ease.
After setting, interactive programming is possible with same feel as 3-axis machine.
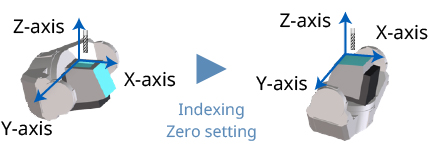
I want to integrate a gear machining process.
The high-accuracy gear machining process is integrated easily with 5-axis machining centers.
By entering basic information and dimensions of gear component, program output can be done.
About Maintenance
There are many maintenance items, and I forget some unintentionally.
Items requiring maintenance are all managed at the Maintenance Monitor.
Operators are notified of when they should perform inspection.
Daily pre-work inspection and periodic inspection items, and inspection timing guides are displayed.
By touching the information button, an instruction manual for maintenance items is displayed.
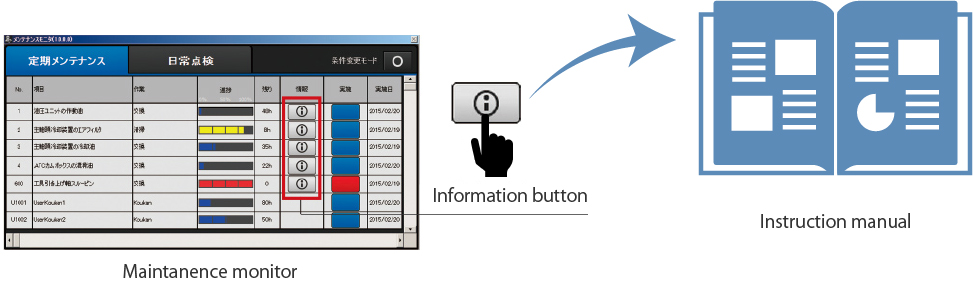
Machine faults occur suddenly, and production becomes chaotic.
Signs of faults are detected, helping prevent machine stoppages before they happen.
Production plans can be maintained, and maintenance costs reduced with systematic maintenance.
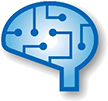
- · AI identifies machine spindle or feed axis abnormalities, abnormality locations.
- · Easy operation simply by touching diagnosis button.
Diagnosis results
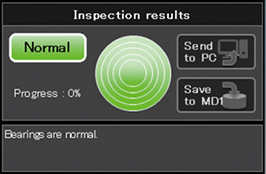
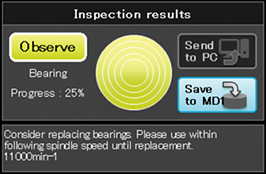
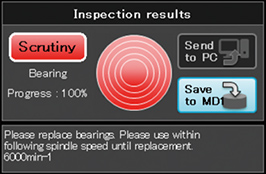
Sludge builds up in the coolant tank, and cleaning it takes a lot of time.
With a sludgeless tank, sludge does not build up, allowing cleaning work to be significantly reduced.
Sludgeless tank sludge removal rate: 99%
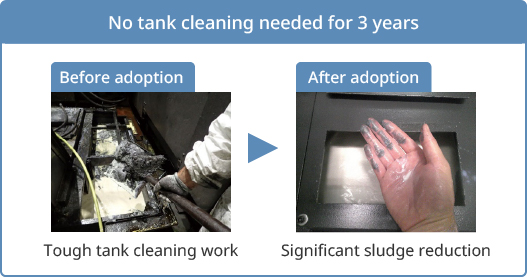
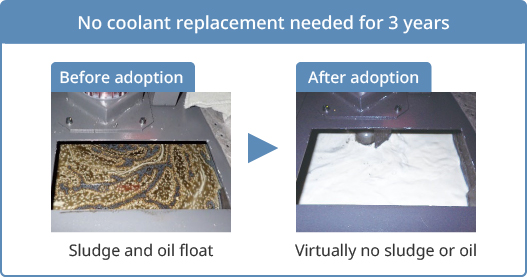
* All values achieved at OKUMA.
About Automation
How to automate 5-axis machining centers?
OKUMA has prepared a variety of automated systems such as robots and APCs tailored to the type of production.
Workpiece transfer systems
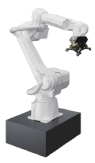
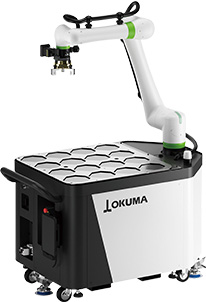
robot
Pallet transfer systems
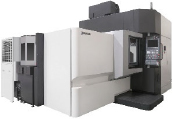
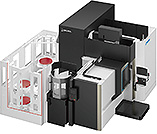
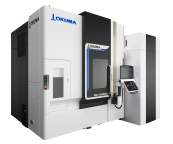
* Mainly for □400 mm pallets or smaller.
I have no experience of robot operation.
Robot operation and machining startup with a robot cell can be performed easily without any expertise.
Automated system capable of easily operating robot by setting parameters according to guidance
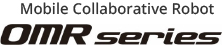
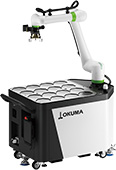
I have no space to install an automated system.
Automation is possible even when space is limited.
Automation of workpiece loading/unloading in minimum space
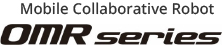
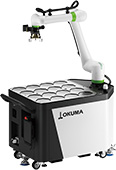
Pallet stocker for space saving
Tower APC
Many pallets can be stored in minimum of space by stacking pallets upward.
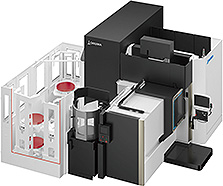
Even with automation, I still have to carry out frequent dimensions gauging and compensation,
and can't seem to get away from the machine.
Dimensional accuracy is stable, meaning that a periodic dimensions check only is sufficient.
This means that users can adopt automated systems in which operators are away from the machine for a long time with peace of mind.

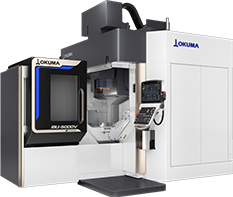

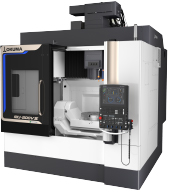
Thermal deviation over time | Thermal deviation over time |
7 μm or less | 7 μm or less |
(actual data obtained at environmental room temperature change of 8 °C)

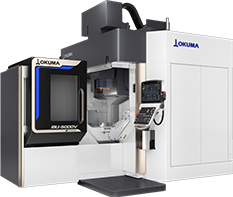
Thermal deviation over time |
7 μm or less |

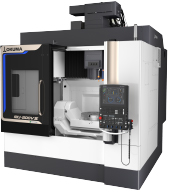
Thermal deviation over time |
7 μm or less |
(actual data obtained at environmental room temperature change of 8 °C)
I want to use hydro-pneumatic jigs to save on labor, but don't have enough jig ports.
The pallet upper surface is equipped a sufficient number of hydro-pneumatic jig ports*.
Further labor saving possible in combination with APC (Automatic Pallet Changer) spec.*
Loading/unloading workpieces is automated with robot*.
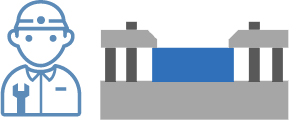

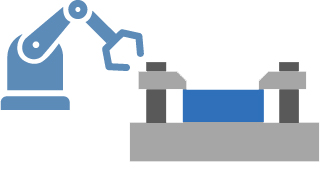
* Option
About Decarbonization
I want to reduce power consumption and CO2 emissions, but don't know where to start.
Most power used in part machining factories is consumed by production equipment (machines).
Let's reduce power consumption by understanding how much power production equipment is actually using.
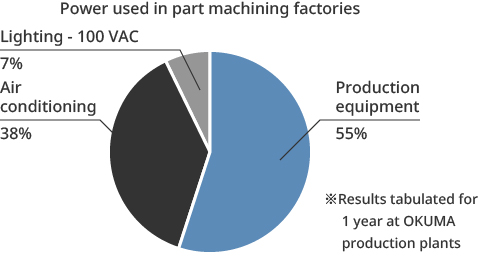
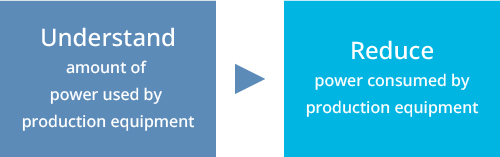
I want to be able to visualize machine power consumption and CO2 emissions.
Power consumption, CO2 emissions can be visualized, recorded, and analyzed with the ECO suite plus ECO Power Monitor.

Monitoring
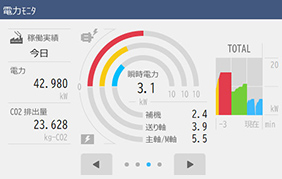
Recording
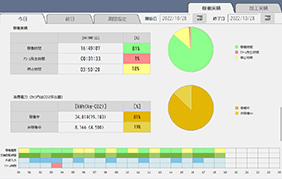
Analysis
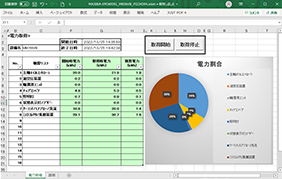
I want to reduce power consumption and CO2 emissions.
It is important to be aware of the following 3 points in order to reduce power consumption and CO2 emissions.
① Reduce machining time ② Reduce energy during machine operation ③ Stop unnecessary equipment proactively
Reducing power consumption and CO2 emissions
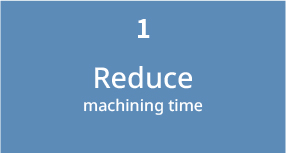
- · Use machines with high cutting capability.
- · Integrate processes.
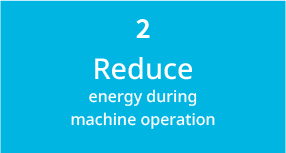
- · Stop excessive air conditioning control.
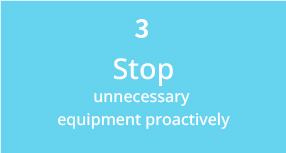
- · Stop unnecessary air conditioning equipment.

Basics of Multitasking Machines
- What is a multitasking machine?
-
A multitasking machine is a machine tool equipped with an auto tool changer (ATC), and is capable of machining processes such as turning and milling.
- What kind of machining is possible with a multitasking machine?
-
A diverse range of workpieces can be machined using many tools.
Turning Milling Gear cutting (option) Grinding (option) Gauging (option)
What are the merits of adopting a multitasking machine?
By integrating various processes into a single machine, shorter production lead time, labor saving, cost reductions, space saving, suppression of accuracy variations, and compatibility with changes in type and quantity of machined parts is possible.
- Shorter production lead time by reducing setup and transfer work
- Labor savings achieved by reducing number of times setup performed
- Reduced equipment adoption costs
- Reduced running costs such as electricity
- No need to install multiple machines, saving space
- Accuracy variations minimized by performing multiple processes with one chucking
- Flexible response to changes in workpiece type and qty with diverse range of tools
How do I choose a multitasking machine?
First select a machine based on the size of the part you want to machine.
We recommend the MULTUS BⅡseries as a step up from a lathe, and the MULTUS U series for even greater productivity improvements.
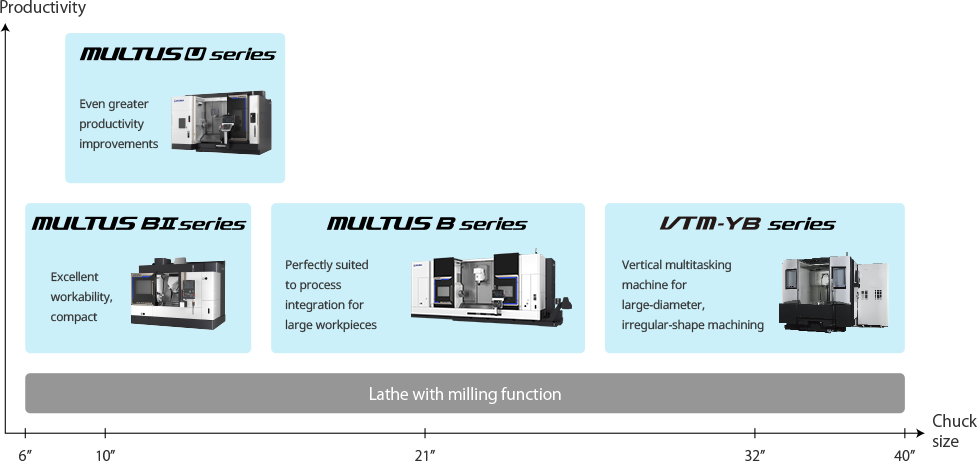
About Machine and Machining Capability
I'm worried about whether a multitasking machine will fit in my factory.
Our multitasking machines can be installed with the same machine height as lathes and machining centers.
Multiple processes can be integrated into a single machine for space saving.
Multitasking machine
W spec DBC 750
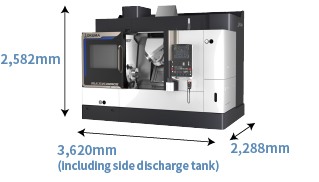
Lathe
MYW spec DBC 800
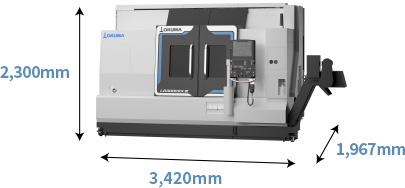
Vertical machining center
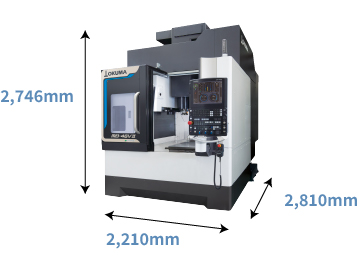
I want to know the machining capabilities of multitasking machines.
Productivity is improved with the same high machining capability as lathes, machining centers.
Multitasking machine
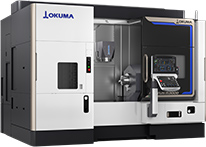
Turning, heavy-duty (S45C) |
4.8mm2 |
Milling, Chip volume (S45C、ø20 end mill) |
604cm3/min |
Turning, heavy-duty (S45C) |
4.8mm2 |
Milling, Chip volume (S45C、ø20end mill) |
604cm3/min |
Lathe
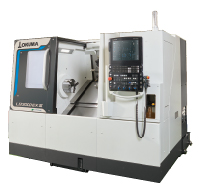
Turning, heavy-duty (S45C) |
4.4mm2 |
Vertical machining center
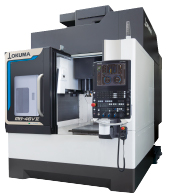
Milling, Chip volume (S45C、ø20end mill) |
672cm3/min |
4.4mm2 | ― |
― | 672cm3/min |
I want to know the machining accuracy of multitasking machines.
Multitasking machines offer the same level of stable machining accuracy as lathes and machining centers.
Multitasking machine
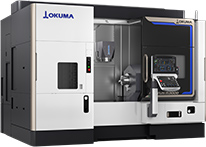
Thermal deformation over time |
10 μm or less |
Lathe
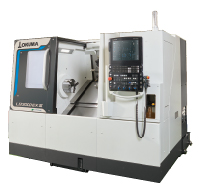
Machining dimensional change over time |
ø5 μm or less |
Vertical machining center
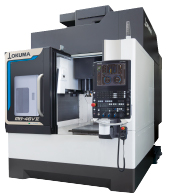
Machining dimensional change over time |
5 μm or less |
(actual data obtained at environmental room temperature change of 8 °C)

Thermo-Friendly Concept
Based on Okuma's unique concept of "accepting temperature changes",
stable accuracy is realized in a normal factory environment even without operators being aware.
Based on Okuma's unique concept of "accepting temperature changes", stable accuracy is realized in a normal factory environment even without operators being aware.
The complex structure of multitasking machines makes me worry about collisions occurring during machine operation.
The Collision Avoidance System allows operators to operate machines without having to worry about collisions, and to focus on machining with peace of mind.

Collision Avoidance System
- Automatic operation
-
NC program is read in advance to check for collisions.
- Manual operation
-
Operation is stopped immediately before collision even when performing manual operation during setup work.
It looks difficult to create machining programs for multitasking machines.
Programs for turning, grooving, machining inclined surfaces can be created easily interactively.
- Interactive programming
-
Turning, grooving, and contour machining and/or drilling of inclined surfaces can be programmed interactively with ease.
Grooving Machining of inclined surfaces
I want to integrate a gear machining process.
The high-accuracy gear machining process is integrated easily with 5-axis machining centers.
By entering basic information and dimensions of gear component, program output can be done.
About Maintenance
There are many maintenance items, and I forget some unintentionally.
Items requiring maintenance are all managed at the Maintenance Monitor.
Operators are notified of when they should perform inspection.
Daily pre-work inspection and periodic inspection items, and inspection timing guides are displayed.
By touching the information button, an instruction manual for maintenance items is displayed.
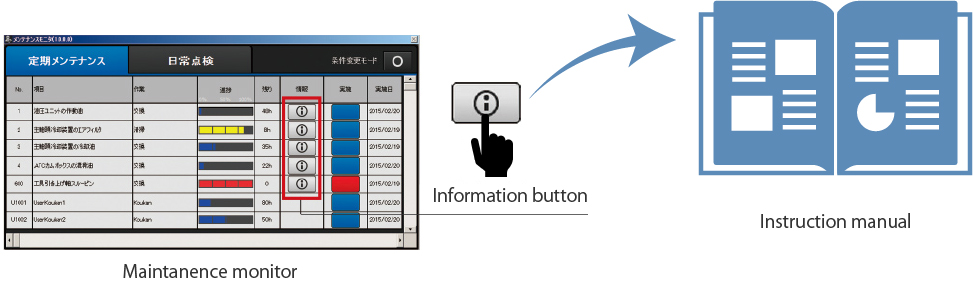
Machine faults occur suddenly, and production becomes chaotic.
Signs of faults are detected, helping prevent machine stoppages before they happen.
Production plans can be maintained, and maintenance costs reduced with systematic maintenance.
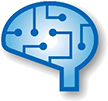
- · AI identifies machine spindle or feed axis abnormalities, abnormality locations.
- · Easy operation simply by touching diagnosis button.
Diagnosis results
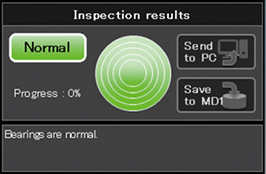
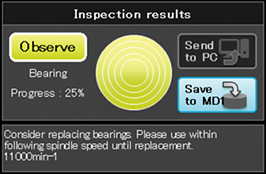
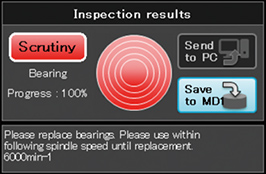
Sludge builds up in the coolant tank, and cleaning it takes a lot of time.
With a sludgeless tank, sludge does not build up, allowing cleaning work to be significantly reduced.
Sludgeless tank sludge removal rate: 99%
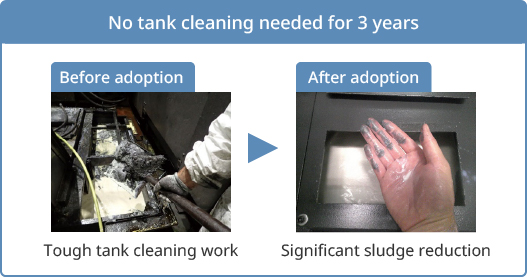
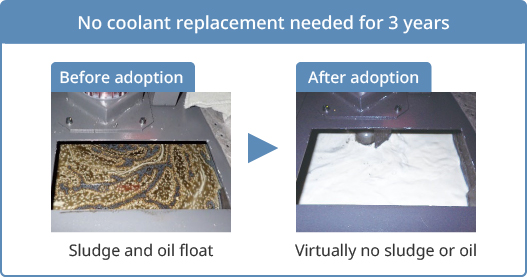
* All values achieved at OKUMA.
About Automation
How to automate multitasking machines?
OKUMA has prepared a variety of automated systems such as robots and barfeeders tailored to the type of production.
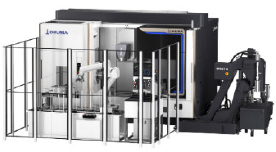
Robot
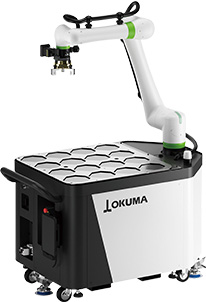
Mobile collaborative robot
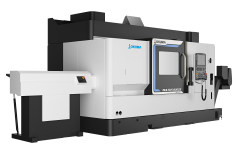
Bar feeders
Unloading units
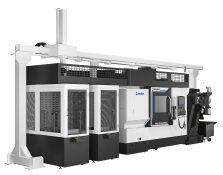
Loader
I have no experience of robot operation.
Robot operation and machining startup with a robot cell can be performed easily without any expertise.
Automated system capable of easily operating robot by setting parameters according to guidance
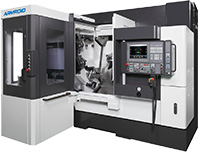
Automation of workpiece loading/unloading, chip cleaning work by built-in robot integrated with machine
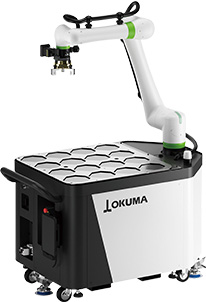
Immediate automation of workpiece loading/unloading
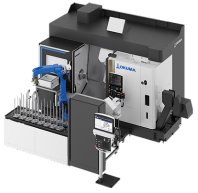
Machining cell that can be easily operated by machining operator
I have no space to install an automated system.
Automation is possible even when space is limited.
Automation of workpiece loading/unloading, chip cleaning work by built-in robot integrated with machine
No need for robot installation space.
Space only necessary for workpiece stocker.
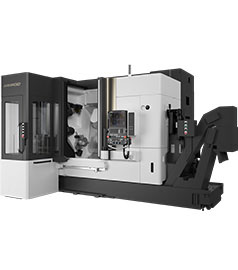
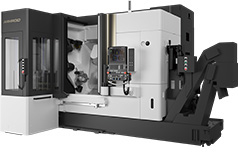
Automation of workpiece loading/unloading in minimum space
Compact size that allows operator to carry out work without retracting robot.
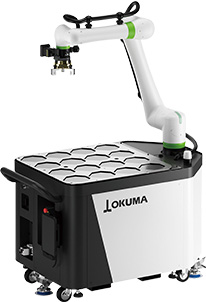
Even with automation, I still have to carry out frequent dimensions gauging and compensation,
and can't seem to get away from the machine.
Dimensional accuracy is stable, meaning that a periodic dimensions check only is sufficient.
This means that users can adopt automated systems in which operators are away from the machine for a long time with peace of mind.
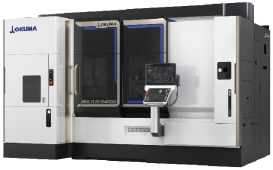
Thermal deviation over time |
10 μm or less |
(actual data obtained at environmental room temperature change of 8 °C)
About Decarbonization
I want to reduce power consumption and CO2 emissions, but don't know where to start.
Most power used in part machining factories is consumed by production equipment (machines).
Let's reduce power consumption by understanding how much power production equipment is actually using.
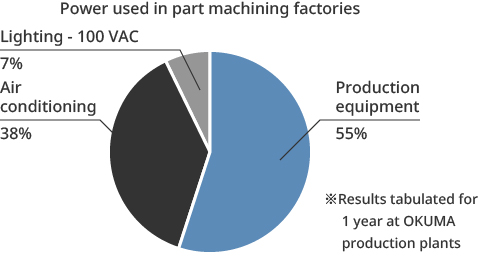
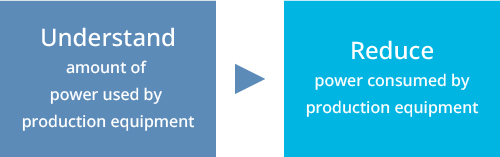
I want to be able to visualize machine power consumption and CO2 emissions.
Power consumption, CO2emissions can be visualized, recorded, and analyzed with the ECO suite plus ECO Power Monitor.

Monitoring
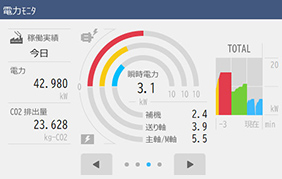
Recording
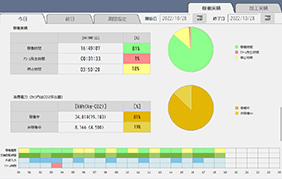
Analysis
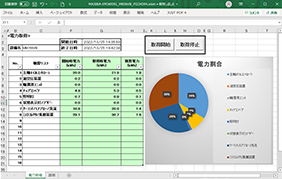
I want to reduce power consumption and CO2 emissions.
It is important to be aware of the following 3 points in order to reduce power consumption and CO2 emissions.
① Reduce machining time ② Reduce energy during machine operation ③ Stop unnecessary equipment proactively
Reducing power consumption and CO2 emissions
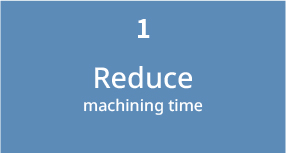
- · Use machines with high cutting capability.
- · Integrate processes.
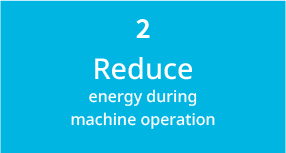
- · Stop excessive air conditioning control.
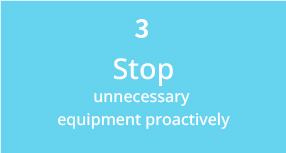
- · Stop unnecessary air conditioning equipment.
