-
01 Capabilitiesof 5-axis machining
centers and
multitasking machines -
02 Why Okuma is chosenOkuma, a manufacturer of
5-axis machining centers
and multitasking machines -
03 Case studiesof installing 5-axis
machining centers and
multitasking machines. -
04 Lineupof 5-axis machining
centers and
multitasking machines -
05 Q&Aabout 5-axis machining
centers and
multitasking machines
03
Case studies of installing 5-axis machining centers and multitasking machines.
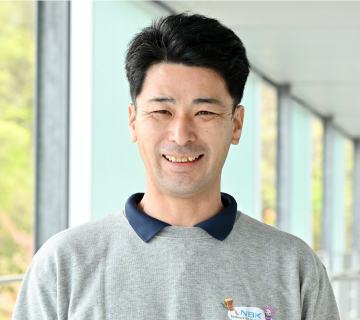
Nabeya Bi-tech Kaisha
- Employees: Approx 400
- 5-Axis Vertical Machining Center
- MU-4000V-L/MU-5000V-L
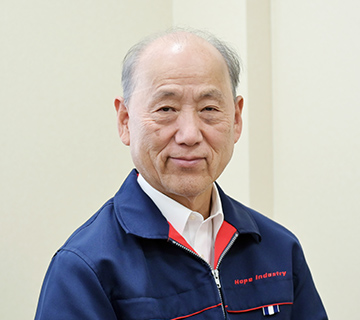
Hope Industry
- Employees: 66
- 5-Axis Vertical Machining Center
- MU-5000V 2-pallet APC specification
Here are case studies of customers who have installed 5-axis machining centers and multitasking machines.
Use these as case studies to assist in problem-solving
Nabeya Bi-tech Kaisha
The effort required for additional machining of pulley shaft holes has been dramatically reduced, boosting productivity
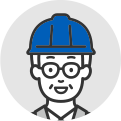
We manufacture power transmission pulleys (castings) used in blowers and commercial air conditioners. We also provide a “shaft hole additional machining service”, which is an additional service to machine shaft holes, screw holes, and keyways to the workpiece. Within a day, machining process is done and product is shipped out. For 30 years, we relied on three machine tools, including a lathe and an in-house-built special-purpose machine, to perform pilot hole drilling, turning, and screw tapping. However, the numerous processes and the need for skilled labor for tasks like diagonal hole machining made it challenging to reduce time. We concluded that investing in a 5-axis machining center was essential to boost productivity.
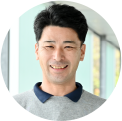
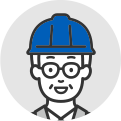
Given these circumstances, what made you choose Okuma?
While comparing the performance and features of 5-axis machines on the websites of various machine tool manufacturers, my boss encouraged me to visit Okuma and see the machines in person. Therefore, we visited Okuma to thoroughly examine the machining precision, range, and cycle time, as well as operability and ease of use.
In addition to its high basic performance, what stood out to us was the excellent accessibility to the machine, which eliminates the need for climbing stairs. We were particularly concerned about other manufacturers' machines, which required workers to go up and down stairs during setup, creating additional strain for them. Another feature that caught our attention was the collision avoidance system. We were convinced that this feature would significantly reduce preparation time by eliminating the need for operators to perform interference checks on the actual machine. Additionally, we found it highly appealing that measurement results of machining accuracy, maintenance information, and operation manuals could be easily checked on the large operation screen.
Furthermore, since we plan to utilize the machining center not only for additional shaft hole machining but also for custom product manufacturing in the future, we determined that Okuma's 5-axis vertical machining center "MU-V" was the optimal choice. This decision was based on a comprehensive evaluation of machining quality, workability, cost, applicability, and other factors.
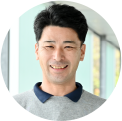
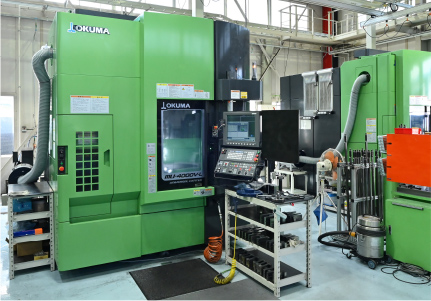

Machining that previously required three machines is now completed by a single machine.
Machining time has been reduced to around 1/2 to 1/3, and machining productivity has approximately doubled.
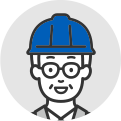
Now that you have installed the MU-4000V-L and MU-5000V-L, how would you rate their productivity and ease of use?
The preparatory hole drilling, lathe machining, and drilling machine operations, which previously required three separate machines, can now be completed by a single MU-V machine. This has halved the machining time per piece from 15–20 minutes to 5–10 minutes. As a result, the daily production limit, which was previously capped at 35 pieces, has increased to approximately 60 pieces.
The improved accessibility of the machine has also reduced the operator's strain, making setup work much easier and more efficient.
In addition, the “3D Virtual Monitor” enables us to check for interference on a PC in advance, significantly reducing preparation time before actual machining. The operation screen of the “Collision Avoidance System” also allows us to check for interferences in advance, eliminating the risk of collisions. This has made first-part machining, which previously required a slower feed rate, much more efficient. Maintenance information is also accessible through the OSP, with maintenance and inspection schedules clearly visualized. This ensures proper machine maintenance, helping to prevent breakdowns and unexpected shutdowns.
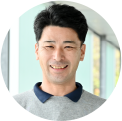
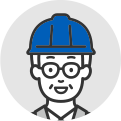
Thank you very much.
Hope Industry
Advancing into new fields utilizing manufacturing expertise gained through machining of precision parts for semiconductors
The MU‑5000V: optimized for high‑mix, low‑volume production
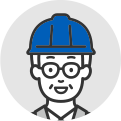
Please share why you decided to install a 5-axis machining center.
Our 3‑axis vertical and horizontal machining centers have enabled prototype and precision‑parts machining, but the global surge in semiconductor demand has left us operating at maximum capacity.
Times like these call for acquiring new technologies and making investments to secure future growth.
When we solicited ideas and opinions from the shop floor, one proposal stood out. It was to install a 5‑axis machining center to take on more advanced machining challenges.
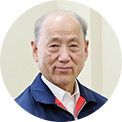
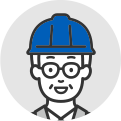
Given these circumstances,
what made you choose Okuma?
Although we had high expectations for integrating multiple processes into one machine, we were concerned about the complexity of programming, the difficulty of interference checks, and about the risks of machine stoppages caused by collisions.
Nevertheless, with an eye on our next stage of growth, we pushed ahead with the installation plan of the two-pallet APC configuration after realizing the need to boost productivity by raising our capability to do more unmanned operation.
During model selection, we compared 5-axis machines from Okuma and two other suppliers, and ultimately selected the MU-5000V.
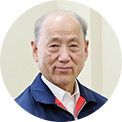
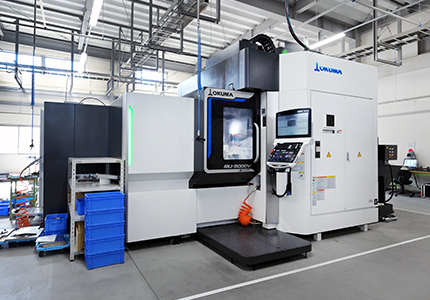
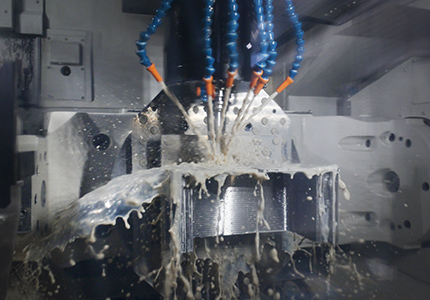
By integrating multiple machining processes into a single machine, time used for setup change was reduced by 35 percent
Consistent dimensional stability and high machining performance—even in 5-axis machining
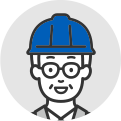
Now that you have installed the MU-5000V, how would you rate its productivity and ease of use?
With 3-axis machines, each step is split across several setups, so every setup change consumes time and effort. A 5-axis machine can integrate those steps into one machine, allowing us to complete multiple processes within a one-chucking setup which dramatically lightens the workload.
In particular the MU-5000V can handle workpieces requiring angled holes or back-side chamfers in a single-chucking operation, greatly improving overall efficiency.
Because 5-axis machines have more complex kinematics, we expected the effects of thermal deformation to make tight-tolerance work difficult. However, thanks to Okuma's Thermo-Friendly Concept, the MU-5000V delivers the same dimensional stability as our 3-axis Okuma models and requires virtually no thermal-related compensation work.
We have also experienced its outstanding machining capability—it is a machine that cuts exceptionally well.
Components for semiconductors require to have exceptional surface quality. Hyper-Surface Ⅱ automatically corrects tool marks and edge unevenness caused by CAM data, resulting in improved machined surface quality.
Having the idea of doing long hours of unmanned operations overnight in the future, we equipped the machine with a 2-pallet APC configuration which allows workpiece setup to be done even while the machine is running. This is to enable us to increase machine utilization and meet the to meet the growing demand for semiconductor related parts.
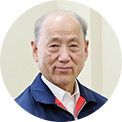
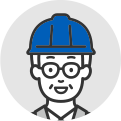
Thank you very much.
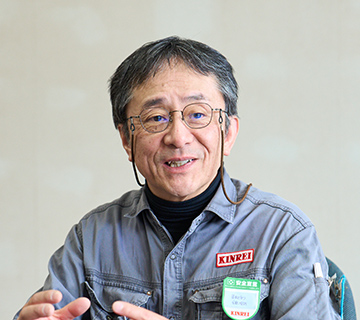
KINREI MACHINERY
CO., LTD.
- Employees: 79
- Multitasking Machine + Built-in Robot
- MULTUS B300Ⅱ ARMROID
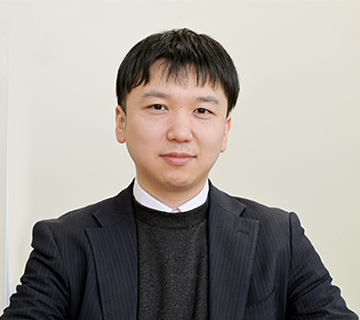
Tamatec Co., Ltd
- Employees: 100
- Multitasking Machine
- MULTUS B300Ⅱ (Sub spindle Spec)
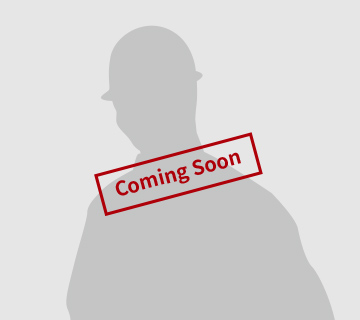
Here are case studies of customers who have installed 5-axis machining centers and multitasking machines.
Use these as case studies to assist in problem-solving
KINREI MACHINERY CO., LTD.
We have achieved lead time reduction and space savings by integrating the machining processes of core components, which were previously handled using a lathe and external robot.
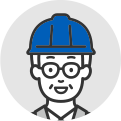
Please share why you decided to install a Multitasking Machine + Built-in Robot.
We are a manufacturer of wire stranding machines (bunchers), which are used to produce cables and wire harnesses for automobiles, aircraft, mobile devices, and medical equipment. Our machines are delivered to numerous customers, including those in over 20 countries worldwide.
All core components of the bunchers are manufactured in-house. One such component is the guide wheel, a pulley used to feed metal wire.
Its V-groove must be machined with high precision in order to smoothly feed ultra-fine metal wires—which are thinner than a human hair—at high speeds.
Until now, machining the guide wheel required five steps: two performed by an automated system consisting of an NC lathe and external robot, followed by drilling and finishing processes.
Setup changes were both labor and time intensive, while the safety fences consumed valuable floor space. Reducing lead time and achieving space efficiency had been ongoing challenges.
At that time, Okuma proposed consolidating several machining processes into one machine using the MULTUS B300Ⅱ ARMROID, a multitasking machine with a built-in robot.
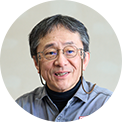
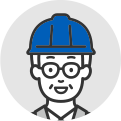
Given these circumstances, what made you choose Okuma?
We have used many Okuma machines. We actually already have two multitasking machines which we have been using for some time now: the MULTUS B300 and the MULTUS U4000.
Given the situation, the proposal to consolidate several processes—previously performed with multiple machines and material handling equipment—into a single machine was very appealing, as it offered significant reductions in lead time and space usage.
What made the MULTUS B300Ⅱ ARMROID especially attractive was its built-in robot arm. Compared to our previous methods of machining, this machine would allow us to increase productivity while only requiring minimum space to install the machine and mobile workpiece stocker. In addition, the ability to ensure operator safety without installing safety fences made us feel this machine would be the perfect solution to the challenges we were facing.
However, we were unsure whether a single MULTUS B300Ⅱ ARMROID could ensure the required machining accuracy for the V-groove of the guide wheels.
Trial cuts revealed that chips scattered within the machining chamber negatively affected the groove’s machining quality.
In response, we collaborated with Okuma to develop a solution. Okuma modified the jaw shape, while we revised some of the guide wheel’s machining process. These adjustments successfully reduced the effects caused by chip scattering and allowed us to overcome this problem.
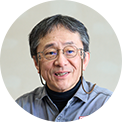
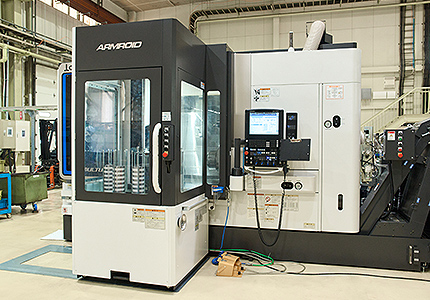
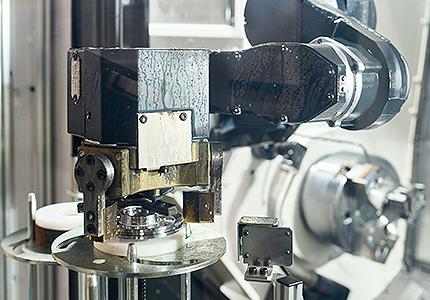
Lead time has been significantly shortened by merging five processes (which were done across two machines) into two processes (that can be done on one machine)
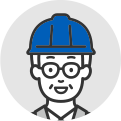
Now that you have installed the MULTUS B300Ⅱ ARMROID, how would you rate their productivity and ease of use?
Previously, machining of guide wheels required five separate processes, involving considerable time and effort for attaching, detaching, and transferring workpieces during each setup change.
With the introduction of the MULTUS B300Ⅱ ARMROID, operators simply load the workpieces into the mobile work stocker (a 10-station elevating multi-level worktable) attached to the machine. From there, the machine handles the entire operation, completing everthing in just two processes.
As a result, lead time has been drastically reduced and the extra time can now be used for program creation and setup for the next machining task. This has contributed to improving overall productivity.
The machining chamber contains two spindles (main and sub), a turret, a robot, and various structural components, making it difficult to track all movements and perform comprehensive interference checks.
However, by using the collision avoidance system after creating the program, interference can be checked visually and allows automatic operation to be done with confidence.
To increase productivity with limited personnel, we plan to perform short-cycle turning and small-lot machining manually during the day, while using the MULTUS B300Ⅱ + ARMROID for unmanned nighttime operation of medium-lot, time-intensive complex machining. We are actively working toward realizing this vision as soon as possible.
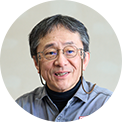
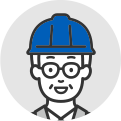
Thank you very much.
[ Tamatec Co., Ltd ]
Reducing setup and machining preparation time required when using a lathe and machining center to manufacture components, and eliminate accuracy variations during setup.
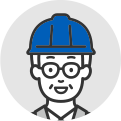
Please share why you decided to install a multitasking machine
We manufacture precision parts for industries such as aerospace, medical and optical equipment, and semiconductor manufacturing equipment. Many of these parts have complex geometries and are made from difficult-to-machine materials such as inconel and titanium alloys. All have strict dimensional tolerances and require to be machined within a 10-micron accuracy range. Before installing the MULTUS BⅡ series, we machined these parts using both NC lathes and machining centers. Accuracy becomes difficult to maintain when using several machines to machine a single component, but we made sure we always met each industries’ quality assurance standards.
However, in order to grow our business, improve productivity by shortening lead time used during for precision machining processes. We determined that introducing multitasking machines would allow us to consolidate processes, reduce setup changes and related tasks, and eliminate accuracy variations during setup.
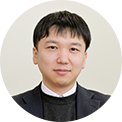
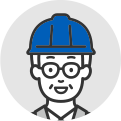
Given these circumstances, what made you choose Okuma?
Among the available options, we chose the MULTUS B300Ⅱ (sub-spindle specification) for its high level of fundamental performance and compatibility with workpiece sizes.
The main decisive factor for choosing the machine was its high rigidity. This was an essential requirement for machining difficult-to-cut materials with high accuracy and speed.
Another key factor was the Thermo-Friendly Concept, a thermal displacement control technology that ensures stable machining dimensions. Although we operate using a two-shift operation schedule to keep utilization rates of machinery as high as possible, machine operations stop between 4:00 a.m. to 8:00 a.m. due to an opening between shifts. However, the MULTUS B300Ⅱ is capable of maintaining stable machining accuracy even after a cold start at the beginning of the day shift. This applies even during seasons when outside temperatures are extreme. When machining difficult-to-cut materials, cutting tools are subjected to high loads, resulting in quicker replacement cycles. One superb feature of the machine is that tool life for each indivudual tool can be managed on the OSP system.
Additionally, we had experience of using Okuma’s NC lathes, so we were confident that it would not be diffficult to learn how to program and operate an Okuma multitasking machine.
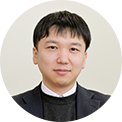
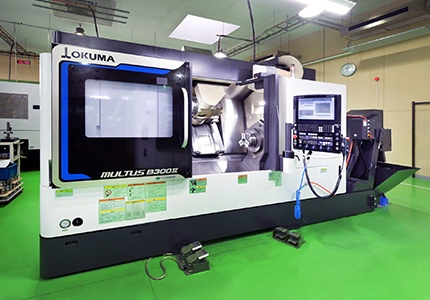
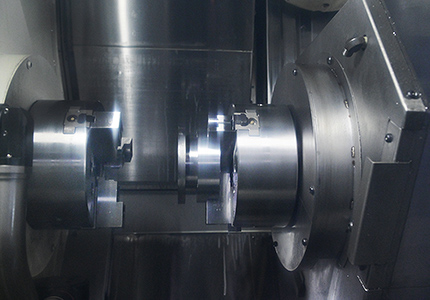
All machining processes can be completed with a single multitasking machine, resulting in approximately 30% improvement in productivity.
Both high quality and high productivity can be achieved while reducing labor.
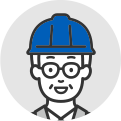
Now that you have installed the MULTUS B300Ⅱ (sub-spindle spec), how would you rate its productivity and ease of use?
When processes are divided between a NC lathe and a machining center, significant time and effort are required for tasks such as dimensional inspection, setup changes, and workpiece cleaning. With the MULTUS B300Ⅱ (sub-spindle specification), parts that previously required four processes on two separate machines can now be completed in just two processes on a single machine due to the abiltiy to transfer workpieces between spindles. This has eliminated the need to handle work-in-progress workpieces between machines and has improved the overall production flow.
In addition, because there is minimal phase error during transfer, positioning jigs are no longer necessary. Also, issues that occurred during setup changes—such as scratches, dents, and the need to remachine due to size errors—have been drastically reduced. As a result, we have been able to significantly reduce tasks that were required between processes, resulting in a productivity improvement of approximately 30%. All this is done while maintaining micron-level machining quality. Even when machining complex parts that require various cutting and drilling operations, the MULTUS can be left unattended for approximately 30 to 60 minutes. During that time, operators can focus on preparing for the next process or conduct quality checks, which helps reduce the workload for operators managing multiple machines.
There was a motor shaft job that our competitors had refused because they could not meet its strict accuracy requirements. However, we took the job and were able to succesfully meet the various tolerances that were required for the workpiece.
In addition, the MULTUS B300Ⅱ (sub-spindle specification) features a highly rigid milling spindle, allowing it to machine tough-to-cut materials such as Inconel and titanium alloys with ease. Even at high spindle speeds. The machine also offers exceptional repeatability, enabling stable machining of precision components with tight tolerances—such as medical device parts—with dimensional accuracy in the 10-micron range.
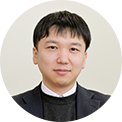
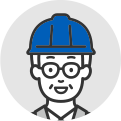
Thank you very much.
Please share why you decided to install a 5-axis machining center.