- HOME
- Okuma Technology Premium Solutions
- Hyper-Surface
Okuma Technology Premium Solutions
Auto machining data compensation, easy and improved die/mold surface quality
Hyper-Surface, in addition to the Sculptured-Surface Adaptive Acceleration Control featured in the
previous Super-NURBS, detects CAM-output machining data “disturbance,” and corrects that on the
Okuma CNC to improve surface quality while maintaining the required shape accuracy.
- Production floor issues
- Machining data command-point
disturbance adversely affects
surface quality -
- ・Machining data variations result in scratches on the machined surface.
- ・Correcting the supplied data is difficult.
- ・Removing cutter marks by hand finishing and polishing is time consuming.
- Machining data command-point
- User benefits
- Better surface quality without modifying the machining data
-
- ・Eliminates the time required for hand finishing.
- ・Reduce scratches and uneven edges.
Eliminating variations in command position and feed rate improve machined surface quality
Automatically corrects for small variations in machining data command positions of output from a CAM processor.
And passing speeds for each cutter path at corners are made consistent.
That stabilizes feed rates and improves surface quality.
Conditions | Tool | Spindle speed [min-1] |
Feed rate [mm/min] |
Pick feed [mm] |
Cutting depth [mm] |
---|---|---|---|---|---|
Scan-line machining |
ø10-mm ball end mill |
15,000 | 6,000 | 0.2 | 0.1 |
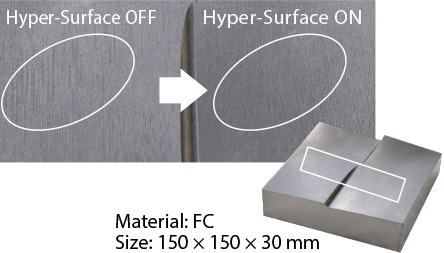
Aligning adjacent cutter paths, reducing ridges
Correcting uneven spaces between adjacent cutter paths, and reducing inconsistent valley depths and edge widths.
Tool | Spindle speed [min-1] |
Spindle feed rate [mm/min] |
Pick feed[mm] | Depth of cut [mm] |
---|---|---|---|---|
ø30-mm ball end mill |
10,000 | 5,000 | 0.5 | 0.1 |
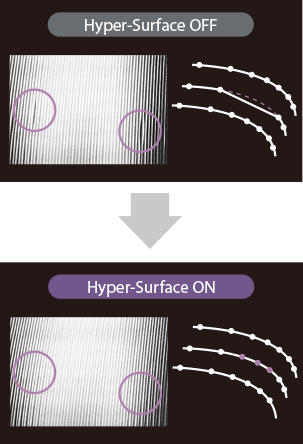