03
5軸制御マシニングセンタ・複合加工機の導入事例
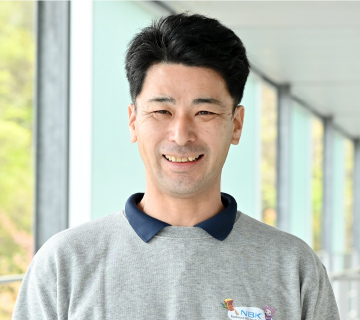
鍋屋バイテック会社 様
- 従業員数:約400名
- 5軸制御立形マシニングセンタ
- MU-4000V-L/MU-5000V-L
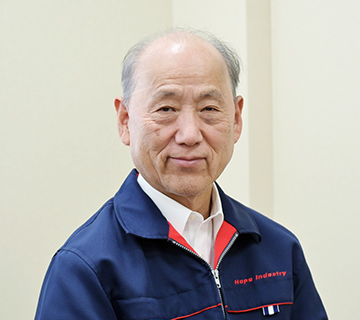
有限会社ホープ・インダストリー 様
- 従業員数:66名
- 5軸制御立形マシニングセンタ
- MU-5000V 2面APC仕様
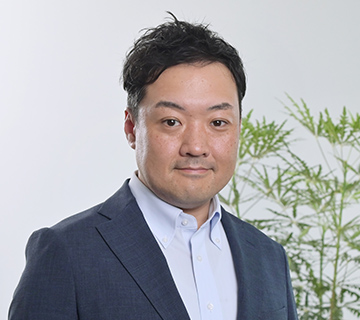
シンセメック株式会社 様
- 従業員数:78名
- 5軸制御立形マシニングセンタ
- MU-8000V-L
実際に5軸制御マシニングセンタ・
複合加工機を導入されたお客様の事例です
課題解決のケーススタディーとしてお役立てください
[ 鍋屋バイテック会社 様 ]
プーリーの軸穴追加工を
劇的に省力化して生産性向上
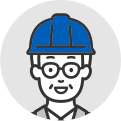
当社は送風機や業務用空調機に用いる動力伝達用プーリー(鋳物)を製造し、注文に応じて、軸穴・押しネジ穴・キー溝を施して1日で出荷する「軸穴追加工サービス」を展開しています。これまで30年間、旋盤や自社製の専用機など3台の工作機械で下穴・旋削・タップねじ加工を行っていましたが、工程が多いうえ斜め穴など熟練を要する加工もあって時間短縮が難しく、生産性を高めるには「5軸加工機の導入が不可欠」と考えたのです。
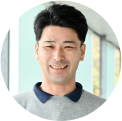
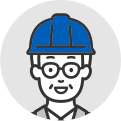
そのような中で、
オークマをお選びいただいた理由は何ですか?
複数の工作機械メーカーのウェブサイトで、5軸加工機の性能や特徴を見比べていると、上司から「オークマで実機を見てきたら」と勧められました。そこで、オークマを訪問して加工精度・加工範囲・加工時間をはじめ操作性や作業性に至るまで詳細に確認しました。
基本性能の高さに加え注目したのは、ステップの昇降を伴わない機械への寄り付きの良さです。他社の機械は段取り作業でステップを昇降する必要があり、作業者の負担になる点が気になっていました。次に衝突を防止するアンチクラッシュシステムです。この機能によって作業者が実機で行っていた干渉チェックを省けるので、準備時間が大幅に削減できると確信しました。また、加工精度の計測結果やメンテナンス情報、取扱説明書が大きな操作画面で確認できるのも魅力に感じました。
さらに、将来は軸穴追加工だけでなく、特注品加工にも活用したいと考えていることから、加工品質・作業性・コスト・応用性などを総合的に勘案し、オークマの5軸制御立形マシニングセンタ「MU-V」が最適と判断しました。
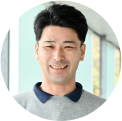
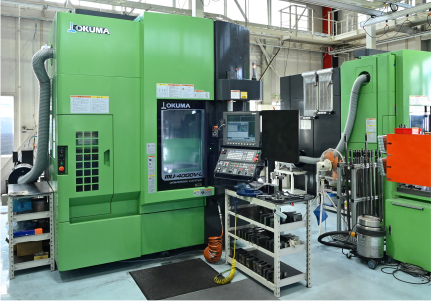
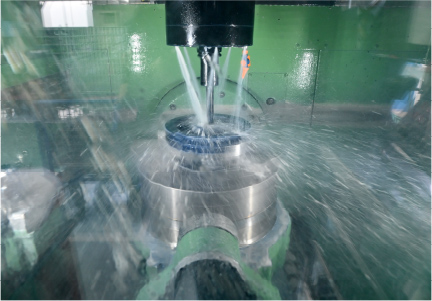
3台の機械で行っていた加工が1台で完結
加工時間は1/2~1/3に、
加工数量は約2倍に
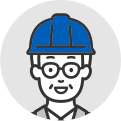
実際にMU-4000V-L、MU-5000V-Lを導入されて
生産性や使い心地はいかがでしたか?
導入前は3台の機械で行っていた下穴加工、旋盤加工、ボール盤加工が1台のMU-Vで完結し、1個当たり15~20分を要した加工時間が5~10分に半減しました。これによって従来は1日35個の加工が限界でしたが60個前後まで増加しました。
機械への寄り付きが良いため、オペレータの負担が低減され、楽に段取作業ができるのも助かっています。
また、「3Dバーチャモニタ」で事前にパソコンで干渉確認ができるため、機械での加工前の準備時間が大幅に短縮できました。「アンチクラッシュシステム」の操作画面でも干渉の確認ができ、衝突の心配がないので、従来は送り速度を落として加工していた初品加工も効率的に行えるようになりました。 メンテナンス情報もOSPで確認でき、保守・点検時期も見える化されるため、機械メンテナンスを確実に行うことで故障や停止を未然に防ぐことができます。
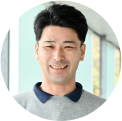
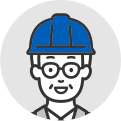
ありがとうございました。
[ 有限会社ホープ・インダストリー 様 ]
半導体の精密部品加工で培った技術をベースに新たな分野へ
多品種少量生産に応える「MU-5000V」
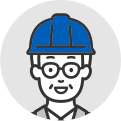
5軸制御マシニングセンタを導入するキッカケを
教えてください
当社はこれまで3軸の立形・横形マシニングセンタを駆使して、半導体向け関連検査装置部品の試作加工や精密部品加工に対応してきました。近年は世界的な半導体需要の高まりから繁忙を極めていますが、こうした時こそ次の成長に向けた新たな技術の習得や先行投資が必要です。
そこで製造現場から意見を募ったところ「5軸加工機の導入による新たな加工へのチャレンジ」という案が浮上しました。
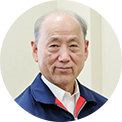
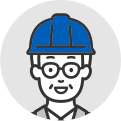
そのような中で、
オークマをお選びいただいた理由は何ですか?
5軸加工機による工程集約への期待は高いものの初めて導入するため、複雑なプログラム作成や干渉チェックの難しさ、機械の衝突による機械停止などの不安はありました。次の成長を見据えた時、長時間の無人運転による生産性向上の必要性を感じ2面APC仕様での導入計画を進めました。
機種選定では、オークマ機のほか2社の5軸加工機を比較・検討し、最終的に選んだのが「MU-5000V」です。決め手は、精密加工に不可欠な3軸機に劣らない高い5軸加工精度、加工能力、OSP-P500の21.5インチ操作盤やインターフェイスの操作性です。もちろん導入前後のサポート体制やメンテナンス対応は重要ですが、この点については、他のオークマ機で実証済みですから不安はありませんでした。
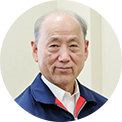
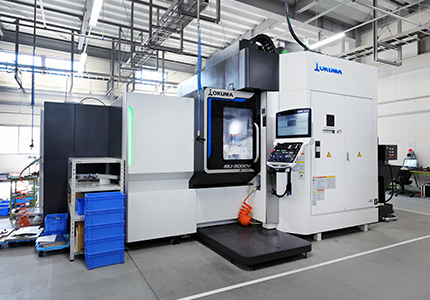
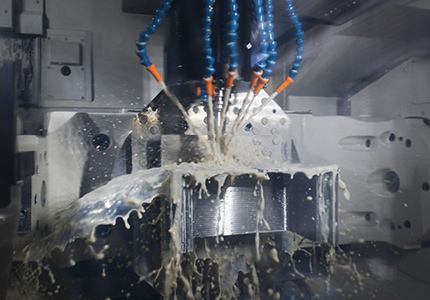
ワンチャッキングで複数の工程を加工できるため、
段取り替え時間を35%削減
5軸でも変わらぬ寸法安定性と加工能力の高さを実感
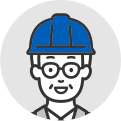
実際にMU-5000Vを導入されて生産性や使い心地はいかがでしたか?
3軸加工では工程が分割されるため段取り替えに時間や手間を要しますが、5軸加工では工程集約によりワンチャッキングで複数の工程を加工できるため、作業負担が大幅に軽減できました。
特にワンチャッキングで斜め穴や裏面取りの加工が必要なワークに対応でき作業の効率化に繋がっています。
また、5軸加工機は軸構成が複雑なため熱変位の影響で安定した精度維持が難しいと思っていましたが、「MU-5000V」はサーモフレンドリーコンセプトのおかげで3軸のオークマ機と変わらない寸法安定性で稼働することができ、熱変位に起因する補正作業はほとんどありません。
加工能力についても"よく削れる機械"を実感しています。
また、半導体向けの部品には高いクオリティが求められますが、「Hyper-SurfaceⅡ」がCAMの加工データに起因するスジ目やエッジの不揃いを自動補正してくれるため、加工面品位向上にも繋がりました。
将来の夜間の長時間無人運転を意識して外段取りでワーク取り付けができる2面APC仕様(自動パレット交換)を採用していますので、今後機械の稼働率を高めていき半導体関連部品の生産拡大に応えていきます。
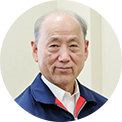
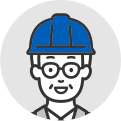
ありがとうございました。
[ シンセメック株式会社 様 ]
ø500~ø1,000mm部品の多品種少量生産で
リードタイム50%削減
機械任せで高いレベルの5軸加工を実現
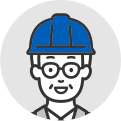
5軸制御マシニングセンタを導入するキッカケを
教えてください
当社が設計から部品加工・組立・制御まで一貫生産する自動省力化装置は、大きさが千差万別、部品も多品種少量です。ø500~ø1,000㎜の部品加工では自社設備にちょうど良いテーブルサイズの加工機がなく、旋削とマシニング加工を分割し、時には外注していました。この領域に適した5軸加工機があれば、工程集約によってリードタイムを短縮でき、外注に伴うコスト・時間の削減が図れると考えました。
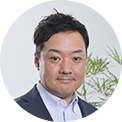
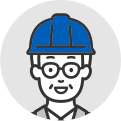
そのような中で、
オークマをお選びいただいた理由は何ですか?
対象加工範囲を加味した上で、重切削と高精度加工を両立できる剛性を備えた「MU-8000V-L」を選びました。内製化の判断が難しかったø500~ø1,000mmのワークサイズに焦点を絞り、ワークサイズのほかにオークマの旋盤に劣らない旋削加工能力に対応していることも大きな理由です。
既設の「MU-500VⅢ」はø700mmまでの加工ができる5軸加工機のため、「MU-8000V-L」が加われば加工の領域が広がり、より付加価値の高い受託加工や自動省力化装置の製作にも役立ちます。
また、5軸加工機の幾何誤差を簡単に補正でき、加工精度を高めるファイブチューニングをはじめとした機能も魅力で、若手オペレータが5軸加工に挑戦しやすい設備環境を整えるという狙いもありました。
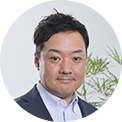
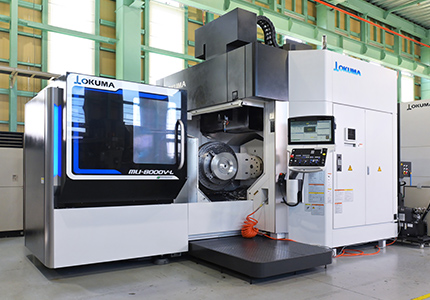
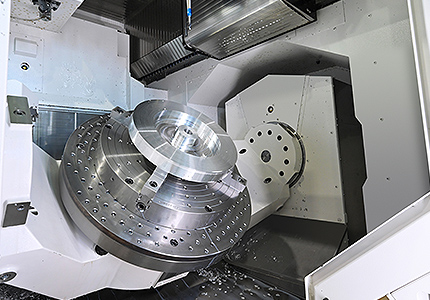
工程集約によりリードタイムを約50%削減
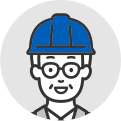
実際に「MU-8000V-L」(旋削仕様)を導入されて
生産性や使い心地はいかがでしたか?
これまでø500~ø1000㎜の部品加工は、NC旋盤や大型の複合加工機で旋削し、その後マシニングセンタで加工していましたが、「MU-8000V-L」の導入により1回のセッティングで旋削もミ―リングも完結できるため、段取り替えに伴う準備作業、精度確認、ワークの移動時間などを含めると生産リードタイムを約50%削減できました。
導入前は複雑な構造の5軸加工機での加工能力や長時間稼働時の精度のバラつきに一抹の不安がありましたが、稼働してみると「MU-8000V-L」は既設の50番テーパの3軸のマシニングセンタに劣らない加工能力があり、加工精度の安定性も申し分なく、機械剛性の高さを実感しています。
また「サーモフレンドリーコンセプト」による寸法安定性も他のオークマ機と変わりなく高いレベルを安定的に維持することができ、氷点下が当たり前の北海道の厳しい冬でも補正作業はほとんど必要ありません。以前はワークの熱膨張率を計算した上で加工していましたが、計算する手間がなくなり、他のことを考える時間ができたことも大きなメリットです。
また、ボタンを押すだけで幾何誤差を自動で計測・補正する「ファイブチューニング」機能(特別仕様)を使うと約10分でチューニングが完了します(フルモード設定の場合)。精度が良いので安心して使うことができ、面倒な計測・補正作業から解放され、機械停止時間も激減しています。
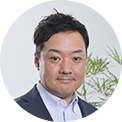
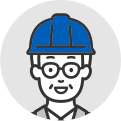
ありがとうございました。
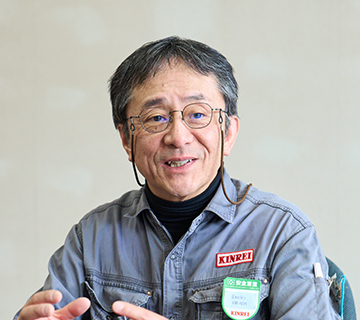
株式会社キンレイ 様
- 従業員数:79名
- 複合加工機+ビルトインロボット
- MULTUS B300Ⅱ ARMROID
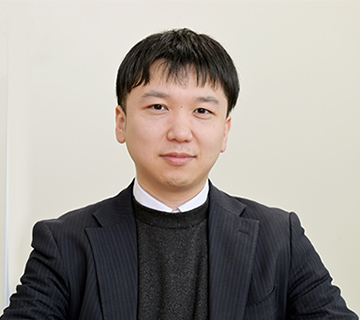
株式会社タマテック 様
- 従業員数:100名
- 複合加工機
- MULTUS B300Ⅱ(対向主軸仕様)
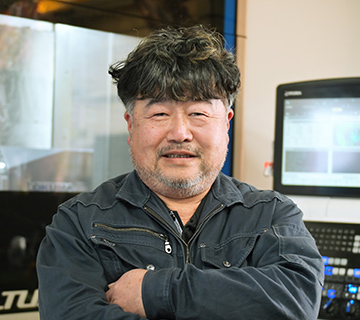
株式会社𠮷田鐵工所 様
- 従業員数:5名
- 複合加工機
- MULTUS U3000
実際に5軸制御マシニングセンタ・
複合加工機を導入されたお客様の事例です
課題解決のケーススタディーとしてお役立てください
[ 株式会社キンレイ 様 ]
旋盤+外付けロボットで加工していた基幹部品加工を
工程集約しリードタイム短縮と省スペース化を実現
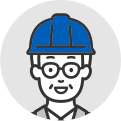
「複合加工機+ビルトインロボット」を導入する
キッカケを教えてください
当社は、自動車・航空機・携帯端末・医療機器用のケーブルやワイヤ―ハーネスを製造する「撚線機(バンチャー)」のメーカーで、海外20ケ国を含む多数の取引先に納入しています。
撚線機の基幹部品は全て内製していますが、その一つが「案内車(あんないしゃ)」という金属線を送る滑車です。そのV溝は、髪の毛より細い金属線を高速で円滑に送るため、厳格な加工精度が必要です。加工には、NC旋盤+ローダ+外付けロボットで2工程、穴あけや仕上げを加えて5工程かかり、段取り替えに手間・時間がかかるうえに安全柵が場所を取り、リードタイムの短縮やスペースの有効活用が課題でした。そんな時にオークマから複合加工機にロボットを内蔵した「MULTUS B300Ⅱ ARMROID」による工程集約を提案されました。
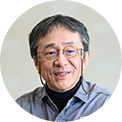
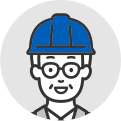
そのような中で、
オークマをお選びいただいた理由は何ですか?
当社ではこれまで多数のオークマ機を使っており、複合加工機では既にMULTUS B300、MULTUS U4000の2台を導入し、活用してきました。そうした中で、複数の加工機やマテハン機器で加工してきた工程を1台に置き換えることができ、大幅なリードタイム短縮と省スペース化を図るという提案は魅力的でした。
「MULTUS B300Ⅱ ARMROID」は機内にロボットアームが入っているため、これまでの工程に対し、機械本体と付属の移動式ワークストッカという必要最小限のスペースで生産性の向上が期待でき、安全柵を設置しなくても作業員の安全性を確保できる点が当社の抱えていた課題解決につながると感じました。
ただ、「MULTUS B300Ⅱ ARMROID」の1台だけで「案内車」のV溝の加工精度を確保できるのか確信が持てませんでした。テストカットしてみると加工室内を飛散する切粉が溝の加工品質に影響を与える。そこで当社とオークマでアイデアを出し合い、オークマ側で爪の形状を変更し、当社は「案内車」の加工工程を一部入れ替え、切粉の飛散による影響を抑えて難題を乗り切りました。
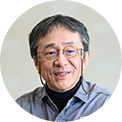
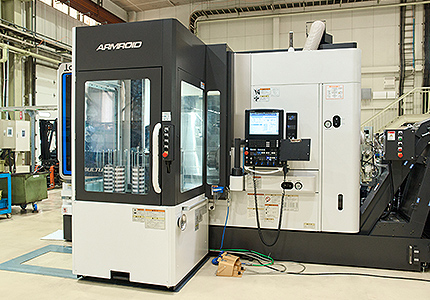
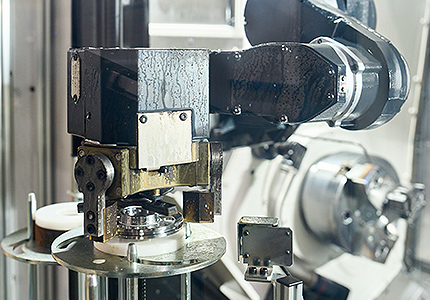
5工程(2台)を2工程(1台)に集約し、
リードタイムを大幅に短縮
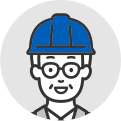
実際に「MULTUS B300Ⅱ ARMROID」を導入されて生産性や使い心地はいかがでしたか?
これまで「案内車」の加工には5工程が必要で、段取り替えに伴う加工物の着脱や移動に相当の手間と時間を費やしていました。それが「MULTUS B300Ⅱ ARMROID」の導入によって、機械本体に付属した移動式ワークストッカ(昇降式多段積みワークテーブル 10ステーション)に加工物をセットすれば、あとは機械任せで仕上げ工程を加えても2工程で完結します。これによりリードタイムが大幅に短縮でき、空いた時間をプログラム作成や次の加工の段取りに充てられ生産性の向上につながっています。
また、加工室内には2つの主軸(メイン・対向)・刃物台・ロボットと複数の構造物があり、すべての動きを把握して干渉チェックをすることは難しいです。しかし、プログラム作成後にアンチクラッシュシステムを使うことで視覚的に干渉チェックができるため、安心して自動運転を行うことができます。
現在、限られた人員で生産性を上げるため、加工時間が短い旋盤加工や小ロットのマシニング加工は昼間に人の手で、時間を要する中ロットの複合加工は「MULTUS B300Ⅱ+ARMROID」で夜間無人運転をという構想のもとで、早期実現に向けて取り組みを進めています。
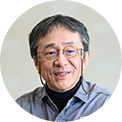
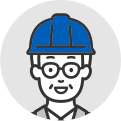
ありがとうございました。
[ 株式会社タマテック 様 ]
NC旋盤+マシニングセンタでの段取り・加工準備を削減し
リードタイムの短縮とともに、段取り時の精度バラつきも解消
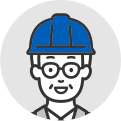
「複合加工機」を導入するキッカケを教えてください
当社は航空・宇宙、医療・光学機器、半導体製造装置などの精密加工部品を手掛けているが、その多くがインコネル・チタン合金といった難削材の複雑形状部品で、要求精度は10μm台と厳格です。これらをNC旋盤とマシニングセンタを駆使して、各分野の品質保証規格に適合するよう仕上げます。
そうした中で、加工部品の領域を広げつつ成長していくには、精密加工においてもリードタイムの短縮により生産性を高める必要があります。複合加工機を導入して工程集約を図り、段取り替えなどの作業を削減するとともに段取り時の精度バラつきも解消すべきと考えました。
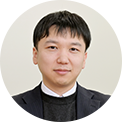
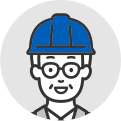
そのような中でオークマをお選びいただいた理由は何ですか?
機種選定では、基本性能やワークサイズとの適合性から「MULTUS B300Ⅱ(対向主軸仕様)」を選びました。
一番の決め手は機械剛性の高さです。これは難削材を高精度かつ速く削るための絶対条件でした。
そして、熱変位制御技術「サーモフレンドリーコンセプト」による加工寸法の安定性も魅力でした。「MULTUS」なら厳しい外気温の季節でも日勤一番の加工立ち上げ時に安定した精度を保ち稼働することができます。難削材加工においては工具に負荷がかかるため交換サイクルが早いのですが、OSP上で工具ごとに寿命管理ができる点も魅力でした。
また、プログラム作成や操作性については、オークマのNC旋盤の使用実績から違和感なく使いこなせると判断しました。
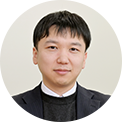
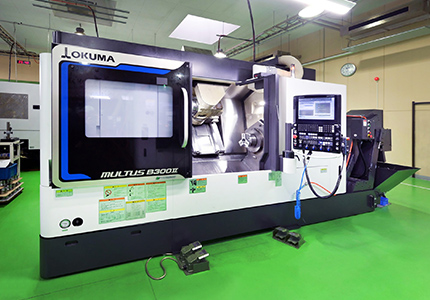
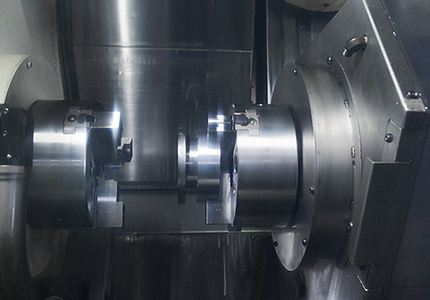
複合加工機1台で全加工ができ、生産性を約30%向上
高品質・高生産性と省人化の両立が可能に
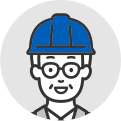
「MULTUS B300Ⅱ(対向主軸仕様)」の生産性や使い心地はいかがですか?
NC旋盤+マシニングセンタの工程分割では、寸法確認、段取り替え、ワーク洗浄などに時間と手間を取られますが、「MULTUS B300Ⅱ(対向主軸仕様)」では、対向主軸による加工物の受け渡しによりこれまで2台4工程で仕上げていた部品を1台2工程で完結することができ、中間仕掛品がなくなり、生産の流れがスムーズになりました。
また、受け渡しの位相誤差が少ないため位置決め治具が不要になったほか、段取り替えに伴う傷・打痕(へこみ)や寸法調整が必要な再加工が激減しました。これによってミクロン単位の加工品質を確保しながら工程間作業を大幅に削減でき、生産性を約30%向上させることができました。複雑形状の部品加工では多様な切削や穴あけを約30分~60分機械任せにできるため、加工中は、その分次の加工準備や品質チェックの時間に充てることができ、オペレータの作業負担軽減にもつながっています。
開発品のモータシャフトでは、厳しい精度要求に競合先は「対応不可」と回答したのに対し、当社はすべての公差を達成。また、光学系レンズの鏡筒では、両端からのネジ切り加工で同軸度ø0.01といった厳しい幾何公差があり、これを満たさないとレンズの光軸がずれて不良品になってしまいますが、当社は同軸度ø0.01を難なく達成しました。
また、「MULTUS B300Ⅱ(対向主軸仕様)」はミ―リング主軸の剛性が高く、主軸回転速度を上げた状態で硬く粘り気の強いインコネルやチタン合金なども難なく加工することができます。また、繰り返し精度が非常に高く、医療機器部品をはじめ厳しい公差の精密部品も10µm台の寸法精度で安定して加工ができています。
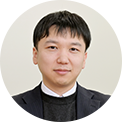
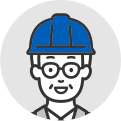
ありがとうございました。
[ 株式会社 𠮷田鐵工所 様 ]
外注していたマシニング加工を内製化し、
高生産性と高精度を両立
初めて導入した複合加工機「MULTUS U3000」により事業拡大
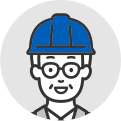
「複合加工機」を導入するキッカケを教えてください
創業時から鍛えた旋削技術で工作機械の部品加工を中心に40年以上の歴史を積み上げてきましたが、取引先の拡大を図る中で、複雑形状部品の受注が増加し、旋削加工の後工程であるマシニング加工を外注する比重が高くなっていきました。
長男が家業を継ぐことを決意したのを機に経営を見直し、マシニング加工を内製化して付加価値の高い部品を一気通貫で納入できる企業に成長しようと考えました。しかし、限られた工場のスペースの活用、オペレータの作業負担軽減、ランニングコストの削減など課題が山積する中、高い生産性と省人化を両立しながら多品種少量に対応するには、どのような機械を導入すべきか検討を重ねていきました。
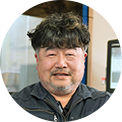
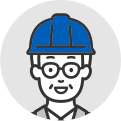
そのような中で、オークマをお選びいただいた理由は何ですか?
新型機の導入は経営を左右する大きな設備投資だけに機種選定には慎重を期し、まず取引先10社に「5軸制御マシニングセンタまたは複合加工機を検討しているが、どのような部品の受注が見込めるか」を聞き取りしたところ、10社から提示された部品はø400mm程度のフランジ形状部品が多くありました。また、初めての導入であれば5軸制御マシニングセンタよりも使い慣れた旋盤ベースの複合加工機の方が自社に適していると考え、複数の工作機械メーカーの複合加工機を検討し、最終的に生産性の観点でオークマの複合加工機「MULTUS U3000」が当社にとって最適な部品加工ができる1台と判断しました。
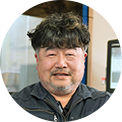
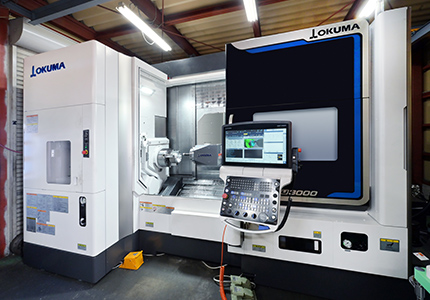
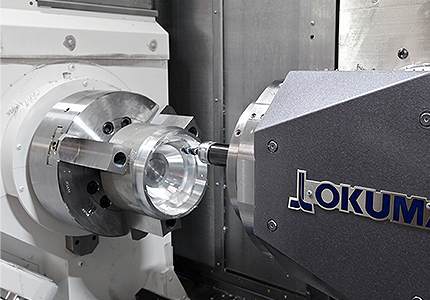
「MULTUS U3000」により生産性が30%以上アップ
過去40年間で最大の月間売上を記録
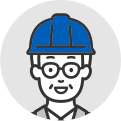
「MULTUS U3000」の生産性や使い心地はいかがですか?
従来は当社で旋削加工をして後工程のマシニング加工は外注していましたが、「MULTUS U3000」であればワンチャッキングで全加工が可能です。旋削加工に加えてマシニング加工を取り込めたことで付加価値の高い複雑形状部品の受注が増えています。そうした加工も外注することなく納入できるので、まとまった数量の注文が入れば効果は絶大です。例えば、ある月に同一部品150個の注文が入った時は、1度プログラムをつくってしまえば、機械にワークをセットするだけのため、月間売上が過去最高を記録しました。搬送の手間と時間を削減し、作業者の負担を最小限にしながらも精度のバラつきなども抑えることができ、生産性は30%以上アップしています。
新規の取引先から「『MULTUS U3000』なら、こんな加工ができないか」という新規案件の問い合わせも多く、以前に比べて加工できる部品は20~25種類ほど増えています。例えば、ステンレス材を肉厚3㎜まで削り出す半導体関連の試作部品です。容易に加工できる部品ではありませんが、量産につながる可能性があるので、40本ATCの工具をフル活用して稼働率をさらに高めることができるように注力しています。
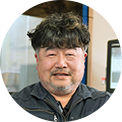
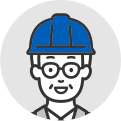
ありがとうございました
5軸制御マシニングセンタを導入するキッカケを
教えてください