The "Top Runner" for Thermal Deformation Control
Thermo-Friendly
Concept
Delivering high accuracy to machine shops
around the world
Thermo-Friendly Concept (TFC) is a thermal deformation control technology for machine tools,
and was developed from Okuma's unique idea of accepting temperature changes.
Since its development in 2001, the number of applicable models has now reached 120.
The high dimensional stability which TFC provides has been well received by customers,
and we have achieved a cumulative shipment of 60,000 units.
Okuma will continue to deliver high accuracy and ease operator's mind to machine shops around the world.
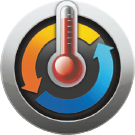
Thermo-Friendly Concept in Numbers
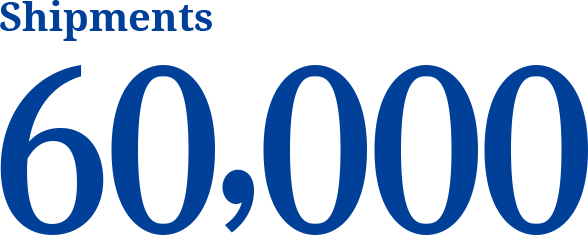
It has been more than 20 years since 2001, when we first launched the MB-46V vertical machining center designed with the Thermo-Friendly Concept.
In 2022, cumulative shipments surpassed the 60,000 mark.
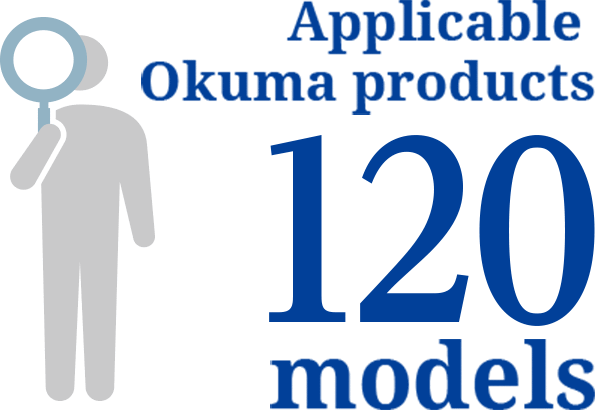
TFC has been well received by customers for its high dimensional stability during temperature changes and has been applied to 120 models so far.

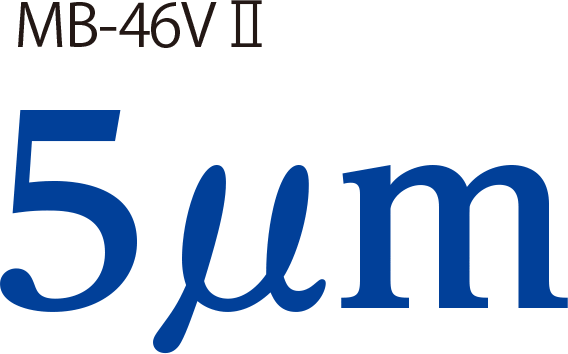
With the MP-46V VMC, the dimensional change over time is 5 µm (at room temperature change of 8 ˚C). It also accurately compensates for the thermal deformation of the spindle even during applications where the spindle speed changes frequently.
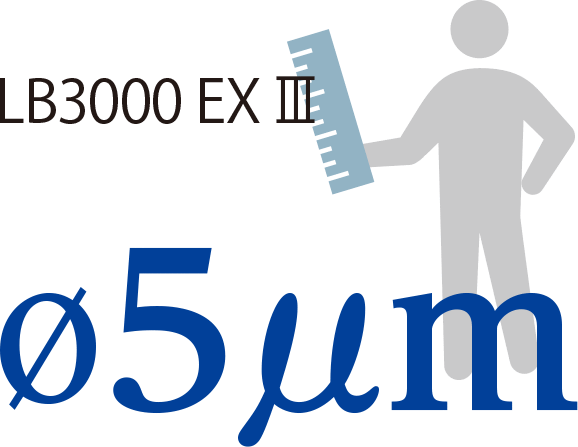
The LB3000 EX Ⅲ CNC lathe achieved a dimensional change of ø5 µm over time (8°C room temp change). This lathe achieves outstanding dimensional stability even during runs and environmental temperature changes in the factory.
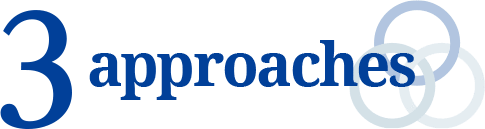
- Simple machine construction
- Columns are constructed symmetrically with a simple building block approach, so the machine can be controlled to deform in-line with complicated bending and tilt, making it possible to predict the thermal deformation.
- Machine designs that equalize ambient temperatures
- That includes the arrangement of covers and the control cabinet to maintain heat conduction evenly.
- Highly Accurate Control Technology
- Okuma's OSP CNC accurately controls not only the influence of room temperature changes, but also spindle thermal deformation due to frequent speed changes and coolant temperature variations.
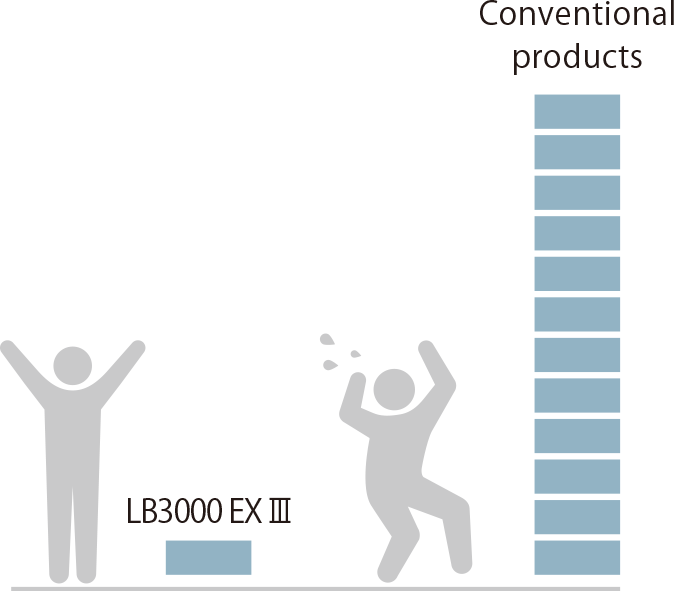
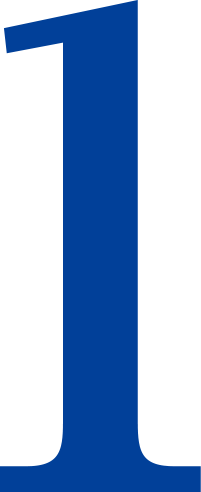
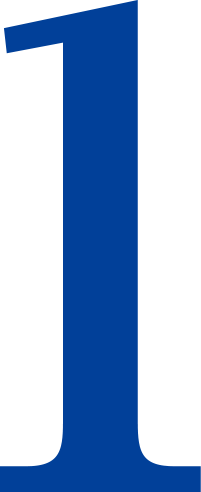
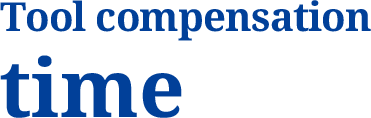
With excellent dimensional stability, if you check the dimensions first in the morning, there is no need for tool compensation even after the ambient temperature has changed or the machine has been temporarily stopped.
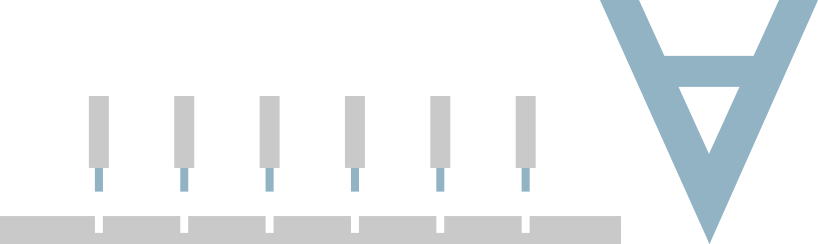
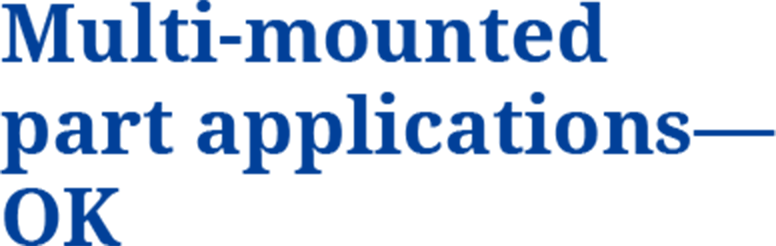
With thermal deformation control of the table position, dimensional errors due to varying workpiece mounting positions are reduced. Machining dimensional accuracy improves even for applications with a multiple of parts mounted on the table.
ABOUT OKUMA
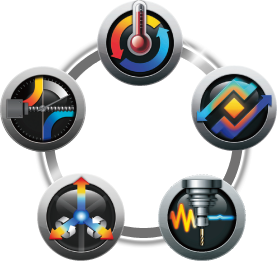
Okuma's Intelligent Technology
Advanced machining infrastructure that revolutionizes the manufacturing environment
This intelligent machining infrastructure supports high accuracy and high productivity, geting the best out of each machine with no thermal deformation, no collisions, no chatter, and automatic adjustment to the best cutting conditions.
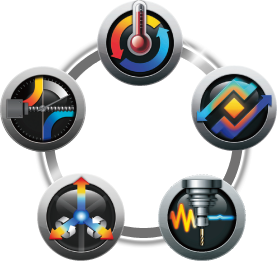
Realization of high precision


Manageable Deformation-
Accurately Controlled
Thermo-Friendly Concept


Gauging and compensatiom
of geometric error
5-Axis Auto Tuning System


Optimized Servo Control
SERVO NAVI
Improvement of ease of use


Collision prevention
Collision Avoidance System


Cutting condition search
Machining Navi
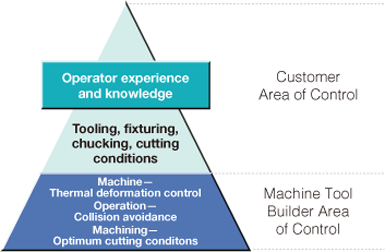
Shop floors with Okuma's Intelligent Technology transform manufacturing.
Until now, thermal deformation has been understood as a “machine peculiarity” and the search for cutting conditions and confirmation of collision prevention as “operator skills.” It was thought quickly overcoming these problems was dependent on machining know-how and seasoned skills.
However, tremendous energy was spent before such machining know-how could be displayed—the headache of dealing with thermal deformation of the machine from temperature changes, lowering of cutting conditions to avoid chatter, and expenditure of time to check collision prevention.
Okuma, in the process of analyzing these shop floor issues, understood several of them to be in the technical sphere of machining infrastructure that machine tool manufacturers should provide to customers, and revolved to revolutionize this field.
We combined original machine technology, electronics and electrical technology, and the information technology to integrate them at a high level and achieve on actual machines the “desktop theory” that was thought to be impossible in practice.
The “intelligent technology” born of these efforts greatly increases the level of shop floor machining infrastructure and creates a manufacturing environment in which customers can fully display their essential machining know-how.
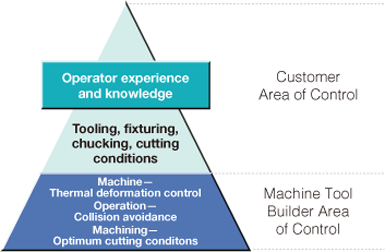