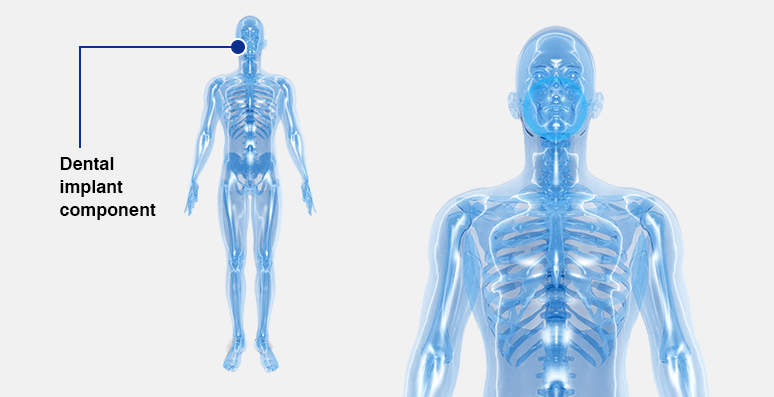
Quick and high-precision machining of complex-shaped components made of difficult-to-cut materials
POINT 01
- Simultaneous 5-axis machining of difficult-to-cut materials can be done while maintaining high productivity
-
- Highly rigid trunnion table allows for precise indexing and high-speed operation
- Top-level machining ability enables highly efficient machining
MU-5000V, MU-6300V Actual data- Face milling: 504 cm3/min (S45C)
End milling: 672 cm3/min (S45C)
- Face milling: 504 cm3/min (S45C)
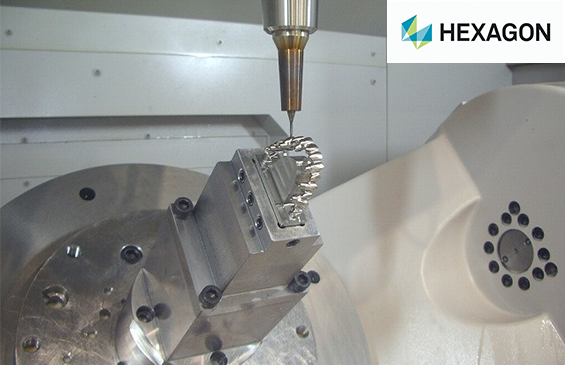
POINT 02
- Hyper-Surface Ⅱ improves the performance of freeform surface machining
-
- No need to modify CAM machining data
Ridgelines and uneven surface edges are reduced to improve the machined surface quality and shorten hand-polishing time. - Automatically compensates for fluctuations within the machining data, positioning errors at edges, and positioning errors between adjacent cutter paths. All while maintaining the required shape accuracy for the workpiece.
- Vibration is suppressed without slowing down at corners, shortening machining time and improving surface quality
- No need to modify CAM machining data
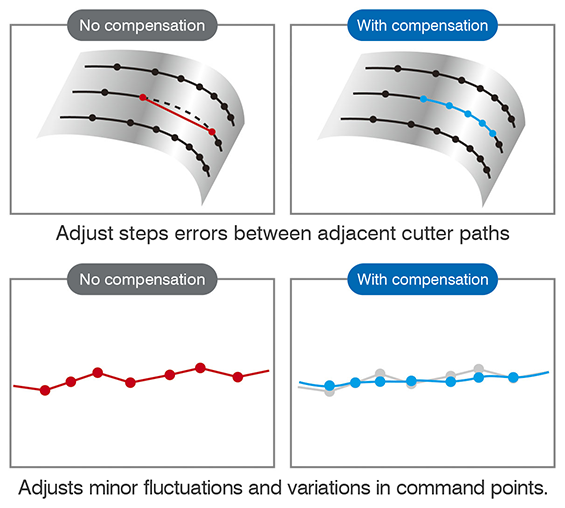
POINT 03
- Thermo-Friendly Concept enables outstanding dimensional accuracy even during simultaneous 5-axis machining
-
- High accuracy is achieved even on a 5-axis machining center that has complex axis configurations.
- Thermal deformation over time is less than 7 μm (MU-4000V actual data)
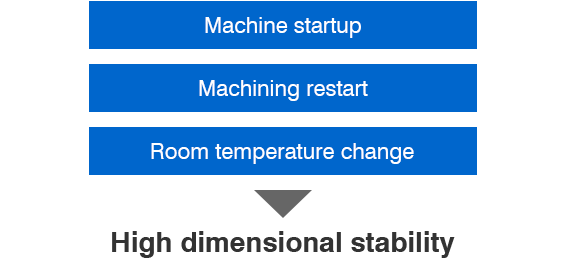