- HOME
- Technology & Solutions Case Studies
- TSUBAMEX Co., Ltd.
Case Studies
—Why Okuma was chosen
MCR-BⅤ was introduced to manufacture high-quality dies and deliver them over a short period to meet immediate the demands of the automobile industry, which is undergoing revolutionary changes
TSUBAMEX Co., Ltd.
- Industry
- Manufacturing of press dies and mold dies
Machine Shop Issues
Decreases in production rate due to operating aging equipment,
the need for increases in productivity in the machining of large outer parts, and downtime in slope machining using 5-face machining are challenges to be solved urgently.
While orders for large outer parts are growing sharply from car manufacturers, which are the main customers for Tsubamex, they continue to require high quality and accuracy of the machined surfaces. Our company takes the time and trouble to maintain the accuracy of the machining equipment and hand-finishing in the post-process. It is especially important to increase productivity in slope machining using 5-face machining. However, it is difficult to deal with these challenges with the existing machines and equipment alone.
The Okuma machine we selected to solve these issues.
Introduction of the machine
Our machine selection team selected
Okuma's MCR-BⅤ from a long-term perspective
A project team of young employees was formed to select the new machine. They were asked to select a machine with the viewpoint: “What kinds of dies do you want to be producing in 20 years' time? You don't need to be bound by past equipment choices. What machine is needed to produce these dies? And what kind of manufacturer should we be having a business relationship with?”
The manufacturer they selected was Okuma, which can internally develop equipment ranging from main bodies to control devices, and offers total solutions. For their preferred equipment the team selected MCR-BⅤ, a cutting-edge double-column machining center [5-face machining], chosen for its rigidity, machining accuracy, and ease of use.
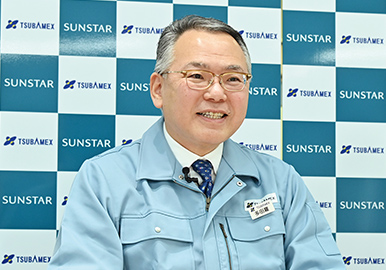
Kuniyoshi Tatara
Results after Installation
Hand-finishing process Reduced by about 20%
Surface quality was improved substantially with high-accuracy 5-face machining, which dramatically reduced man-hours for filing during the finishing work in post-process. The machine makes an especially great contribution to increases in productivity in the production of large outer parts of automobiles.
Reduction of man-hours for alignment and machine downtime
Precision measurement and alignment for large machine require attaching and detaching of workpieces, and required the manufacturer to undertake this part of the process. However, this process can be skipped thanks to MCR-BⅤ's intelligent technology and the automatic compensation function, which significantly reduces machine downtime.
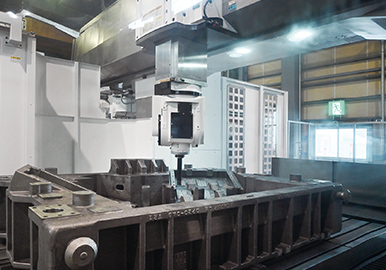
Impressions after installation
Various automatic compensation functions including Hyper-Surface and Auto Attachment Head Compensation have improved surface quality even more than expected
The power of Hyper-Surface is the first feature that creates an impression. This function compensates for any disturbances in the machining data
output from CAM (dispersion of command positions and feed rates) on NC to reduce ridge and uneven edges. It dramatically improved surface quality, increased productivity in slope machining using 5-face machining, and reduced man-hours for finishing and alignment in post-process.
The Auto Attachment Head Compensation function is also reassuring because it allows the operator to complete the automatic setting for the rotation compensation of the attachment head, which is essential for high accuracy, within about 20 minutes. In the past, the task had to be assigned to the manufacturer and it took a whole day.
Seasonal temperature changes in Niigata City can be large, including diurnal temperature changes in summer. Thermal deformation control based on the Thermo-Friendly Concept enables the operator to concentrate on machining without being concerned about such temperature changes. (Masami Ono)
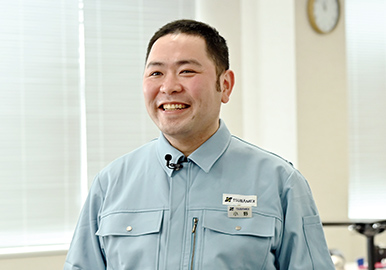
Production Machinery Die & Mold Business
Masami Ono
Further improvements in machine utilization rate and productivity are being pursued, to meet the demand for fast delivery of difficult-to-machine dies
The automobile industry, which is the main destination of our products, is in the midst of once-in-a-century changes including the acceleration of the shift to electric, automated, and connected vehicles. Accordingly, the shapes and materials for the parts are changing radically and customers are demanding dies of increasingly complex shapes and higher quality, with ever shorter delivery periods. As a member of the Sunstar Group, we also have a mission to supply a variety of dies to production sites around the world.
To meet such needs immediately, our most important challenge is to increase the machine utilization rate and productivity. We will also continue to develop unmanned operation of machines, working night and day. And we will make full use of integrated manufacturing, maximizing our strength in covering the whole process from design with digital transformation (DX) to machining and assembly. To achieve this, we are looking forward to further evolution of Okuma's machines, which offer such strength in die machining. (Kuniyoshi Tatara)
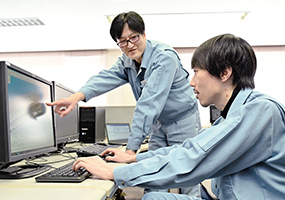
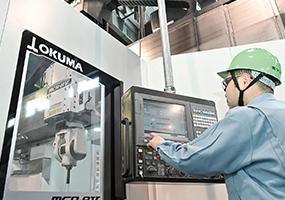
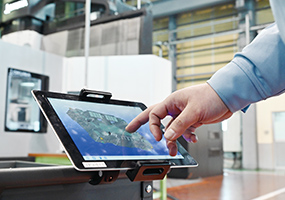
3-dimension modeling data to allow the operator to check detailed instructions on machining
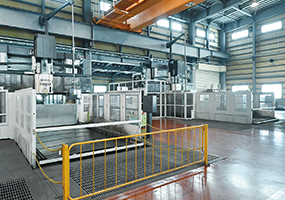
Customer Information
TSUBAMEX Co., Ltd.
In 1892, the company was founded as a file manufacturer in Tsubame City. It launched die manufacturing and metal stamping in 1946 and then began to manufacture dies for automobile parts in the 1960s. Since the introduction of the 3D CAD/CAM system for the first time in the die industry in the 1980s, Tsubamex has promoted the digitization of manufacturing and established original design and manufacturing systems to expand its business. It operates in various fields including the manufacturing of press dies and mold dies for automobile parts, home appliances, building materials, etc., stamping of metal parts, and mass-production machining with injection molding of plastics.
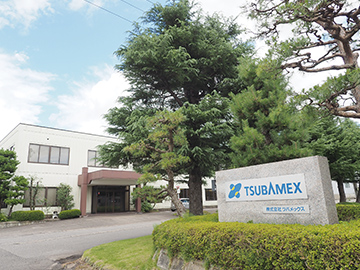