- HOME
- Technology & Solutions Case Studies
- MICRO-CUT Corporation
Case Studies
Okuma—A comprehensive CNC machine tool manufacturer.
Precision machining of difficult-to-cut parts for optical semiconductors
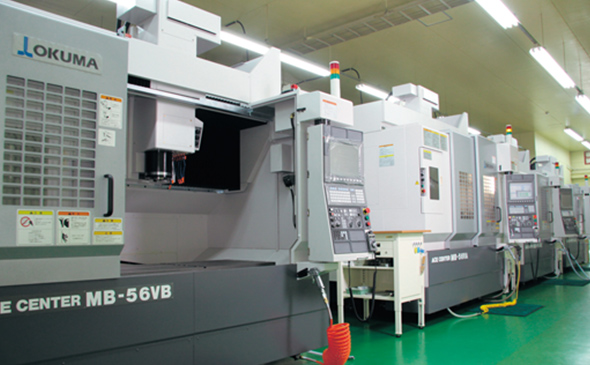
- Industry
- Metal cutting for communications industry applications
MICRO-CUT Corporation
The situation when interviewed
Most of the materials for optical semiconductor parts such as LEDs are difficult-to-cut materials, and machining requires micron-dimensional accuracy and strict surface roughness control.
-
- Issues
-
Machining centers with excellent dimensional stability
- We would like to achieve high-precision parts created with prototypes with high efficiency through mass production.
-
- Implementation
-
Installed the MB-46 and -56VA vertical machining centers with the Thermo-Friendly Concept as standard equipment.
-
- Effectiveness
-
Clears the required accuracy within the 5-micron tolerance.
Less chatter when machining difficult-to-cut materials- The required accuracy of a 5-micron tolerance was cleared, and compensation for thermal deformation became unnecessary.
- High-efficiency machining is now possible while suppressing chatter even on workpieces where the cutting speed cannot be reduced.
Customer Information
MICRO-CUT Corporation
- Head Office /
Factory - 12-2 Kokubu Uenohara Techno Park, Kirishima City, Kagoshima Prefecture
- Website
- http://www.microcut.jp/
- Incorporated
- 2003
- Business
- Focusing on precision metal cutting for the communication/optical communication industries, high-accuracy, composite shape, and metal press machining of various difficult-to-cut materials
- Employees
- 219
Okuma Products/Technology
- MB-46V
- MB-56V
- MB-5000H
- Thermo-Friendly Concept
- Collision Avoidance System • Linked pages may show later models.
Learn more from the customers in the USER'S VOICE Vol. 9 pamphlet.
Also see the Okuma product brochures.
• Member registration (free) is required for downloads.
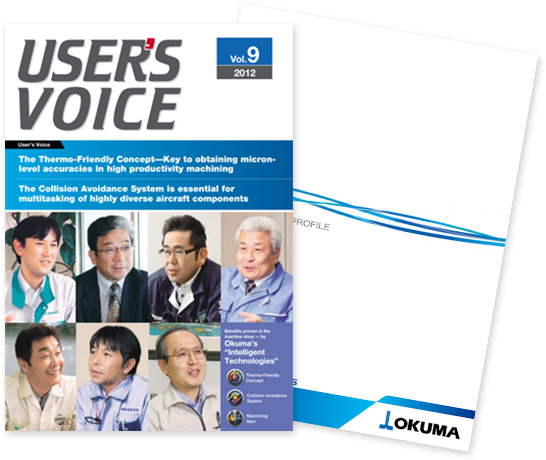