- HOME
- Technology & Solutions Premium Solutions
- Dynamic Tool Load Control
Technology & Solutions Premium Solutions
Dramatically improved productivity of
difficult-to-cut materials
difficult-to-cut materials
DTLC suppresses chipping of insert tools on difficult-to-cut materials like titanium alloy,
to achieve stable processing and longer tool life.
- Production floor issues
- Chipping when machining difficult-to-cut material
-
- • Difficult-to-cut material has poor machinability, can't use inexpensive inserts.
- • Solid tools chip less and cutting conditions can be raised, but they are expensive.
- User benefits
- Reduced chipping and lower tool costs, improved productivity
-
- • Suppress insert chipping, get more stable machining.
- • Significant reduction in tool cost.
- • Setups much easier.
- • Dramatic improvement in productivity of difficult-to-cut material.
Reduced tool cost and improved tool life
[Actual results] Stock removal per tool under the same cutting conditions (tool life)
![[Actual results] Stock removal per tool under the same cutting conditions (tool life) Tool life (titanium) 2.3 times (Okuma comparison)](/english/solution/images/synchro/p_synchro01.jpg)
![[Actual results] Stock removal per tool under the same cutting conditions (tool life) Tool life (SUS) 5.2 times (Okuma comparison)](/english/solution/images/synchro/p_synchro02.jpg)
Optimizing feed rate according to insert-tipped tool runouts
When machining difficult-to-cut materials, the slight shortage in swing from an insert will cause other inserts to receive more cutting force and become chipped.
With Dynamic Tool Load Control, the swing for each insert is measured to optimize feed rate relative to the tool runout.
By equalizing the cutting forces, chipping is reduced and tool life is improved. Cutting conditions don't have to be lowered and expensive solid tools don't have to be purchased.
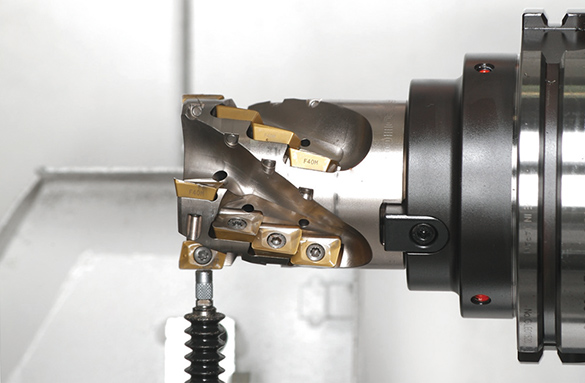
Depending on the tool runout, the feed rate can be controlled to equalize the cutting force among all the inserts.
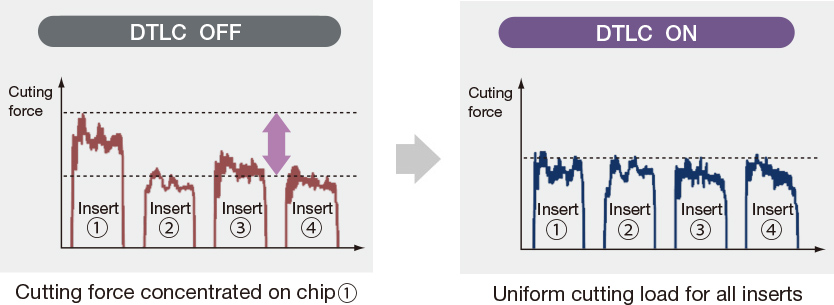