PRODUCTS
The innovation that accepts temperature changes
High accuracy can be achieved in normal factory environments
The machining accuracy of workpieces changes significantly due to the ambient temperature around the machine, heat generated by the machine, and heat generated in machining. The Thermo-Friendly Concept is a unique concept to “accept” such temperature changes so that high accuracy can be achieved in normal factory environments with no special measures taken by the user.
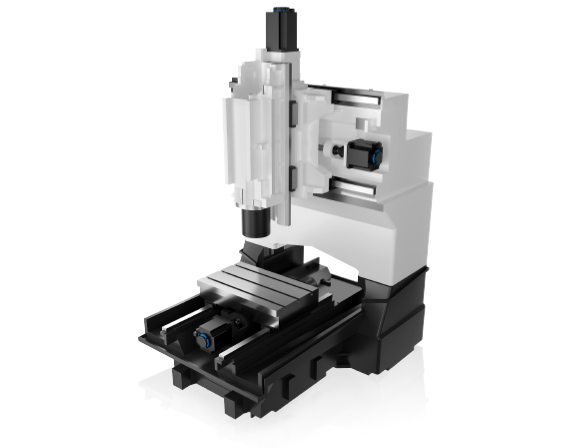
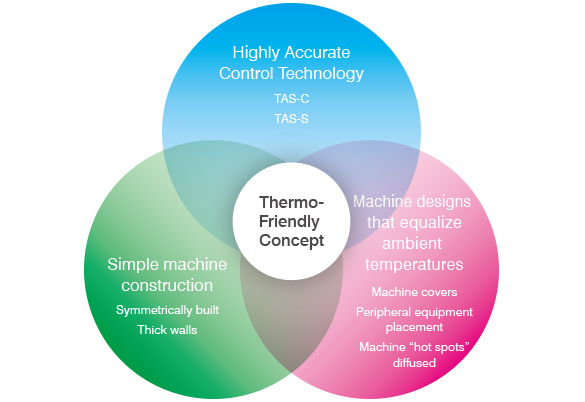
Achievement of both high accuracy and high productivity with emissions reduction and energy saving
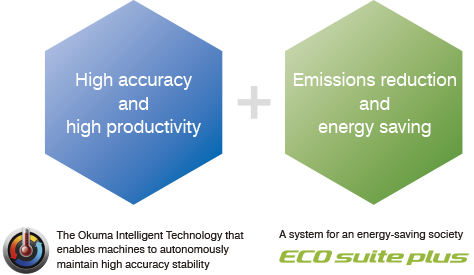
We chose the name “Green-Smart Machine” for our machine tool that achieves high accuracy and reduced energy consumption autonomously and realizes high productivity. With Green-Smart Machines, we will contribute to the solution of social issues faced by the global manufacturing industry, together with our customers.
High accuracy
Outstanding dimensional stability enables stable machining of high-accuracy parts
and stable operation over long hours
In the MB-V Ⅱ series, the Thermo-Friendly Concept has been further evolved and dimensional stability has been improved. By further enhancing the machine's structural design, MB-46V Ⅱ offers an improved dimensional changeover time in a typical factory environment, from 8μm (conventional machine) to 5μm, an improvement of 38% (compared to conventional machines), allowing it to maintain high accuracy with greater stability. Since there is no need maintain a constant ambient temperature, factory equipment costs and power consumption can be significantly reduced.
The Okuma Intelligent Technology that enables machines to autonomously maintain high accuracy stabilityThermo-Friendly Concept
Machining dimensional change over time (actual data)
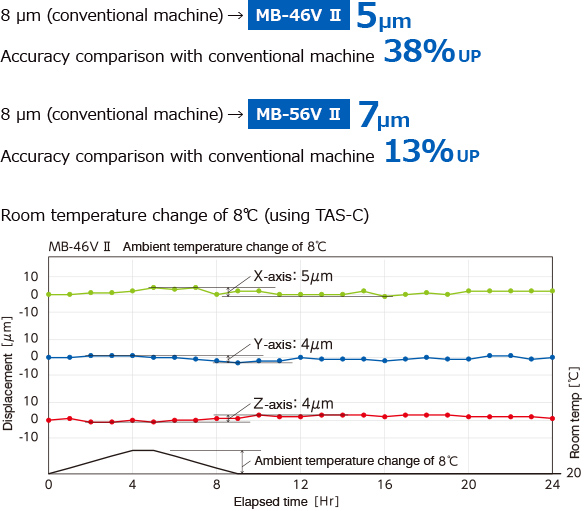
Note: The "actual data" referred to above represent examples, and may not be obtained due to differences in specifications, tooling, cutting condition, and others.
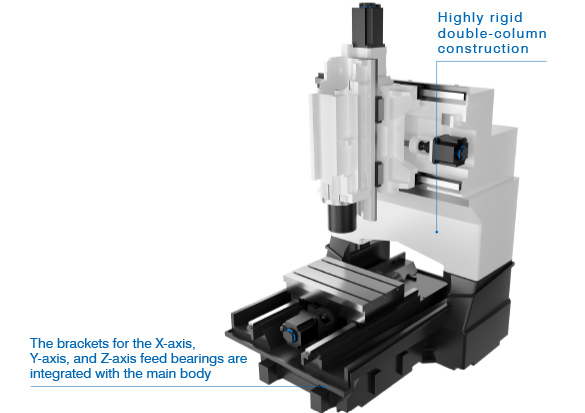
High productivity
Applicable to a wide range of machining situations
From parts machining to die machining, from aluminum materials to difficult-to-cut materials
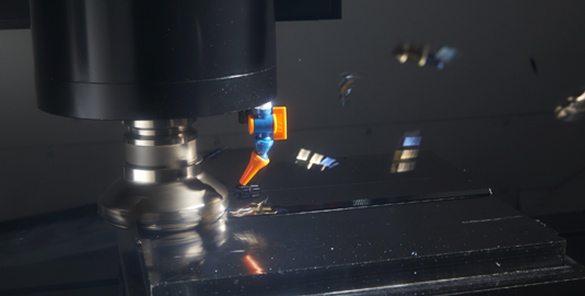
No. 40 spindle | Wide-range spindle (standard) | 15,000min-1 | 22/18.5 kW (10 min/cont) | 199/146N・m (5 min/cont) |
---|---|---|---|---|
High power spindle | 8,000min-1 | 11/7.5kW (10 min/cont) | 198/135N・m (5 min/cont) | |
High-speed spindle | 20,000min-1 | 30/22kW (10 min/cont) | 83/54N・m (5 min/cont) | |
No. 50 spindle | High power spindle | 6,000min-1 | 11/7.5kW (10 min/cont) | 198/135N・m (5 min/cont) |
Wide-range spindle | 12,000min-1 | 26/18.5kW (10 min/cont) | 199/146N・m (5 min/cont) | |
High power spindle | 12,000min-1 | 33/26kW (10 min/cont) | 302/148N・m (10%ED/cont) | |
HSK-F63 spindle | High-speed spindle | 30,000min-1 | 15/11kW (10 min/cont) | 29.1/20N・m (10 min/cont) |
High-speed spindle | 35,000min-1 | 15kW (cont) | 4.09N・m (cont) |
Cutting time and non-cutting time are shortened to increase productivity and reduce power consumption
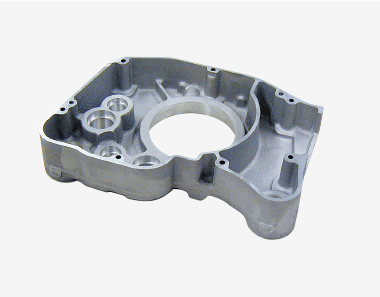
The machining time can be shortened with an increase in the acceleration of the feed axis to reduce the cutting time, as well as with an increase in the rapid traverse and the reduction of the time for tool changes and other actions. The reduction of the machining time leads to an increase in productivity over the same amount of time and enables the saved time to be used for other operations. It also leads to the reduction of the power used for machining.
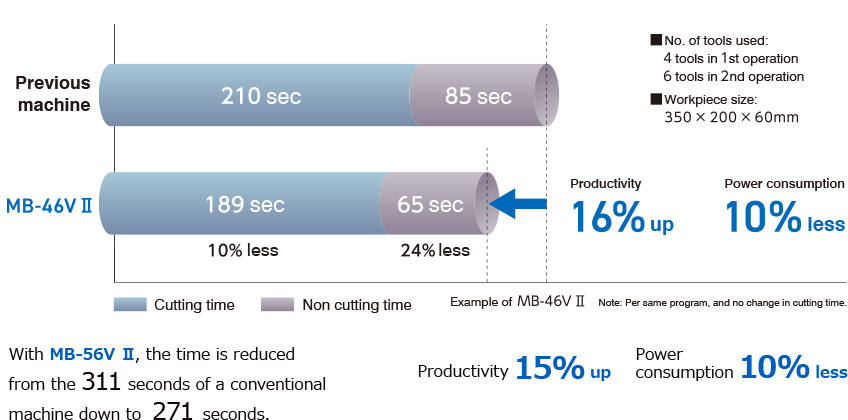
Manpower saving
Various solutions are offered to reduce the operator's burden
ATC Matrix Magazine
This magazine saves space and shortens the time for tool changes when multiple tools are used.
Standard | 20 tools (chain magazine) |
---|---|
Option | 32 tools (chain magazine) |
48 tools (chain magazine) | |
Over 64 tools (matrix magazine) |
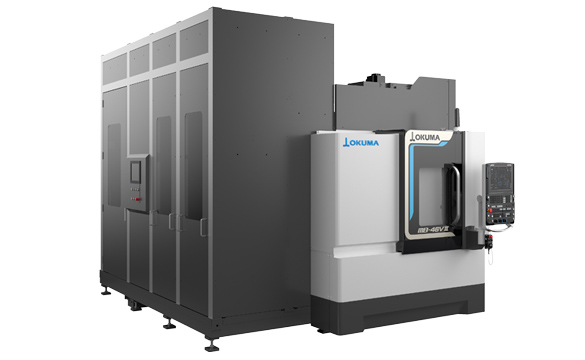
OSP
A next-generation CNC that makes customer manufacturing DX (digital transformation) a reality
Next-generation CNC 
Improved productivity and stable production
As Your Single Source for merging M-E-I-K (Mechanics - Electronics - IT - Knowledge) technologies, Okuma offers this CNC to build an advanced “digital twin” that faithfully reproduces machine control and machining operations and creates new value.
In addition, the product helps improve productivity and achieve stable production, featuring ease of use that allows customers to use their machining know-how. Additional features are: control technology that achieves high-speed and high-accuracy machining, energy-saving solutions that achieve both high accuracy/productivity and eco-friendliness, and robust security functions to protect against the increasing threat of cyber attacks.
- Faithful digital reproduction of machines and processing Ground-breaking concept of a digital twin
- Realizing high-speed and high-accuracy machining Leading-edge machining
- Novice-friendly smart operation Innovative operability
- Reducing environmental impact Energy-saving solutions
- Increasing cyber resilience Robust security
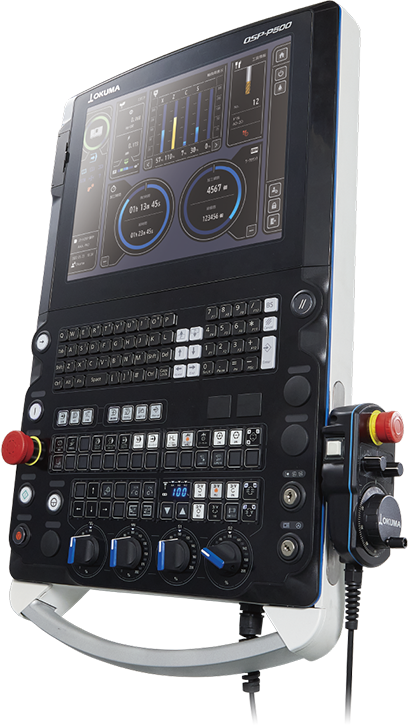
-
Home screen -
Virtual machining -
Preparation of the process chart -
Operation with the process chart -
MacMan plus
Highlighted Specs
MB-46V Ⅱ〈MB-46VE Ⅱ〉 No. 40 spindle |
MB-46V Ⅱ〈MB-46VE Ⅱ〉 No. 50 spindle |
|||
---|---|---|---|---|
Table | Max work dimension | mm (in) | 760 × 460 〈1,000 × 460〉 (29.92 × 18.11 〈39.37 × 18.11〉) | |
Floor to table top | mm (in) | 800 (31.50) | ||
Max load capacity | kg (lb) | 500 〈700〉 (1,100 〈1,540〉) | ||
Spindle | Spindle speed | min-1 | 15,000 [8,000, 20,000, 30,000, 35,000] | 6,000 [12,000, 12,000] |
Tapered bore | 7/24 taper No. 40 | 7/24 taper No. 50 | ||
Feed rate | Rapid traverse | m/min (ipm) | X-Y: 42 (1,654) Z: 36 (1,417) | |
ATC | Tool capacity* | tool | 20 [32] 〈20 [32, 48]〉 | 20 [32] |
Machine size | Height | mm (in) | 2,746 (108.11) | |
Floor space | mm (in) | 1,950 × 2,810 〈2,210 × 2,810〉 (76.77 × 110.63 〈87.01 × 110.63〉) |
2,000 × 2,810 〈2,210 × 2,810〉 (78.74 × 110.63 〈87.01 × 110.63〉) |
|
Mass | kg (lb) | 7,300 〈7,500〉 (16,060 〈16,500〉) |
7,550 〈7,750〉 (16,610 〈17,050〉) |
〈 〉: E (extension type)
[ ] : Option
* Tools are stored in a matrix magazine when the number of tools is no less than 60
MB-56V Ⅱ No. 40 spindle |
MB-56V Ⅱ No. 50 spindle |
|||
---|---|---|---|---|
Table | Max work dimension | mm (in) | 1,300 × 560 (51.18 × 22.05) | |
Floor to table top | mm (in) | 800 (31.50) | ||
Max load capacity | kg (lb) | 900 (1,980) | ||
Spindle | Spindle speed | min-1 | 15,000 [8,000, 20,000, 30,000, 35,000] | 6,000 [12,000, 12,000] |
Tapered bore | 7/24 taper No. 40 | 7/24 taper No. 50 | ||
Feed rate | Rapid traverse | m/min (ipm) | X-Y: 42 (1,654) Z: 36 (1,417) | |
ATC | Tool capacity* | tool | 20 [32] | |
Machine size | Height | mm (in) | 2,746 (108.11) | |
Floor space | mm (in) | 2,520 × 3,123 (99.21 × 122.95) | ||
Mass | kg (lb) | 8,700 (19,140) | 8,900 (19,580) |
[ ] : Option
* Tools are stored in a matrix magazine when the number of tools is no less than 60