PRODUCTSNEW PRODUCTS
AutomationCompact automation for all types of production
Stable operation for long runs of automatic operation in a minimal space
Compact base machine for automation
Handles machining of small and medium-sized parts (250 mm or less) with a 56% smaller footprint compared to conventional machines.
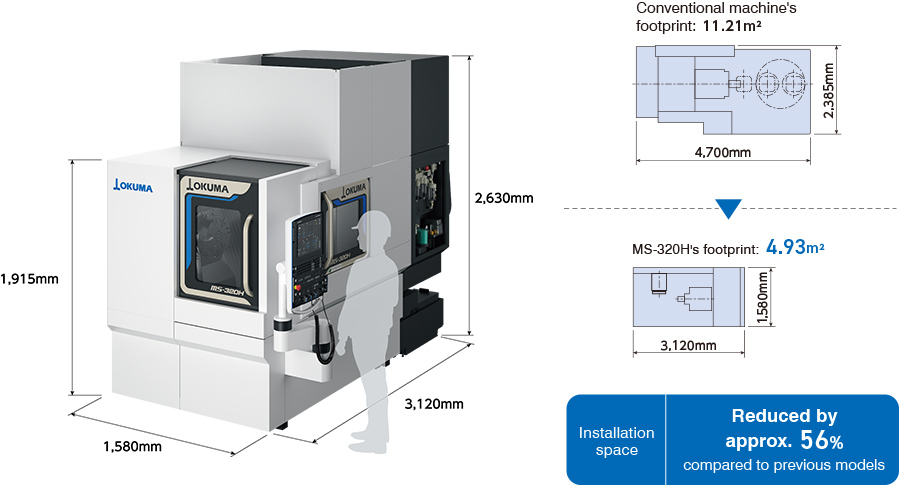
Flexible automation support
8 ports (hydraulic and pneumatic)
Equipped with eight fixture ports for supplying hydraulic and pneumatic pressure as standard specification. Enables flexible fixture compatibility and automatic attachment/detachment of various-shaped workpieces.
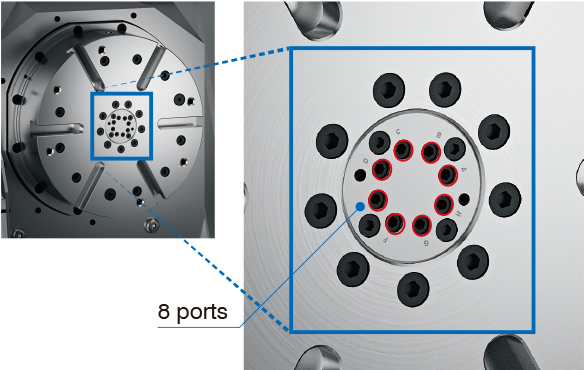
A versatile lineup of automation systems
We have developed a structure that allows for flexible automation, accommodating a wide range of production formats, from high-mix, low-volume production to mass production. Our lineup supports everything from a single-machine machining cell to a mass production line with multiple machines.
Machining cell designed to enhance productivity in mass production machining
Loader
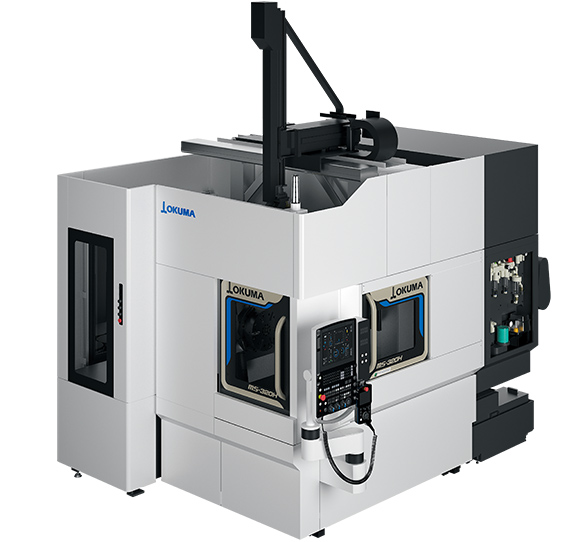
Electric ceiling shutter shortens loader line takt time
The electric ceiling shutter, which opens and closes as the loader enters, enables precise monitoring of the shutter’s position, eliminating unnecessary movements. Additionally, it operates smoothly without shocks during opening and closing, achieving both high speed and reliability.
Loader workpiece loading/unloading time |
5.3 sec |
---|---|
Work size |
ø250 × L80mm ø150 × L120mm |
Ceiling shutter opening/closing time |
0.5 sec |
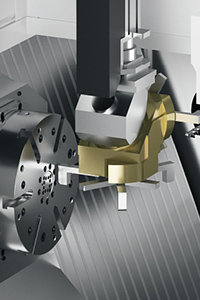
Stocker with high visibility
The 10-station work table features large acrylic windows, allowing the quantity of workpieces and finished products to be checked at a glance. This design helps in preventing machining stoppages caused by insufficient workpiece preparation.
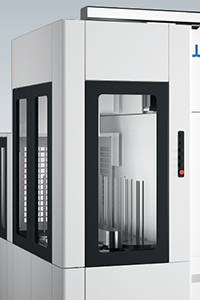
A machining cell that enables the switching of machines according to busy conditions
Mobile collaborative robot OMR series
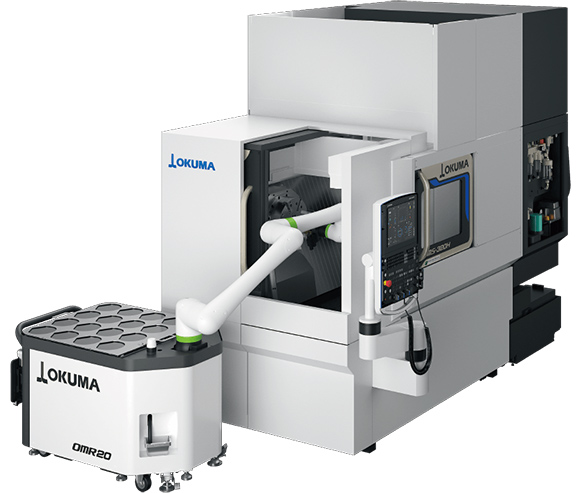
Easy and compact automation
The mobile Collaborative Robot, which automates the loading and unloading of workpieces, achieves the automation of high-mix, low-volume production. With no need for safety fences, the robot can be moved freely within the factory, enabling flexible automation according to busy conditions. Machine switching is completed in just 4.5 minutes, significantly reducing start-up time. Moreover, no teaching or programming is required, allowing for easy operation of the robot without the need for specialized knowledge or skills. It can be installed within the operator’s workspace of a single machine, enabling compact automation.
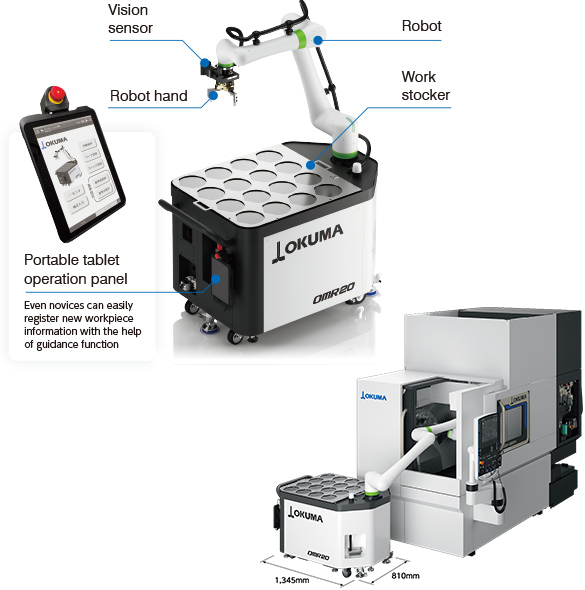
Stable operationChip troubles are eliminated to maintain stable operation over long hours
Innovative machine structure to prevent chip accumulation in the machine
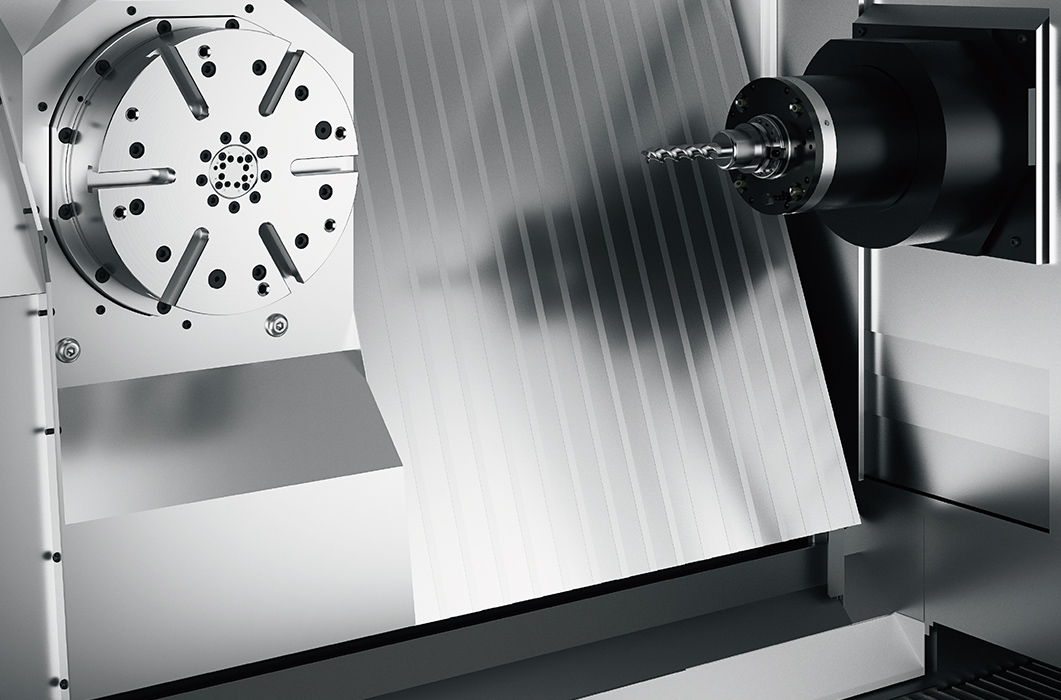
In-machine cover structure to prevent chips from accumulating in the machine
The slope angle of the stainless steel machine covers around and beneath the table has been increased (up to a maximum of 81°) to prevent chip accumulation.
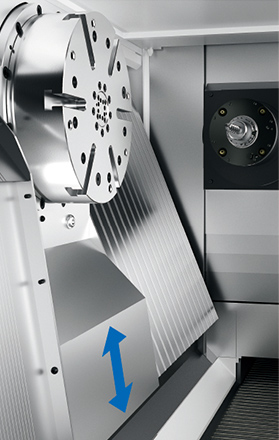
The moving part of the Z-axis has been designed to eliminate any areas where chips could get trapped. Also, the single stainless steel cover design of the X-axis cover and a flat Y-axis telescopic cover with minimal unevenness prevents chip accumulation.
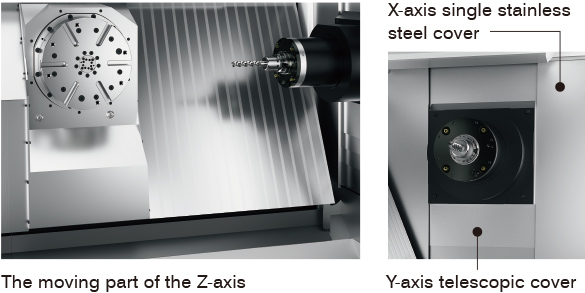
Full-center trough that collects chips across the entire machining chamber area, and a vertical surface table
The full-center trough structure, which enables chip discharge from the entire machining area, significantly enhances chip disposal capacity. By positioning the table vertically, chips fall directly on the in-machine chip conveyor located beneath the machining point and are discharged outside the machine, preventing accumulation on the workpiece or table. This ensures stable, long-term continuous machining without concerns about chip accumulation.
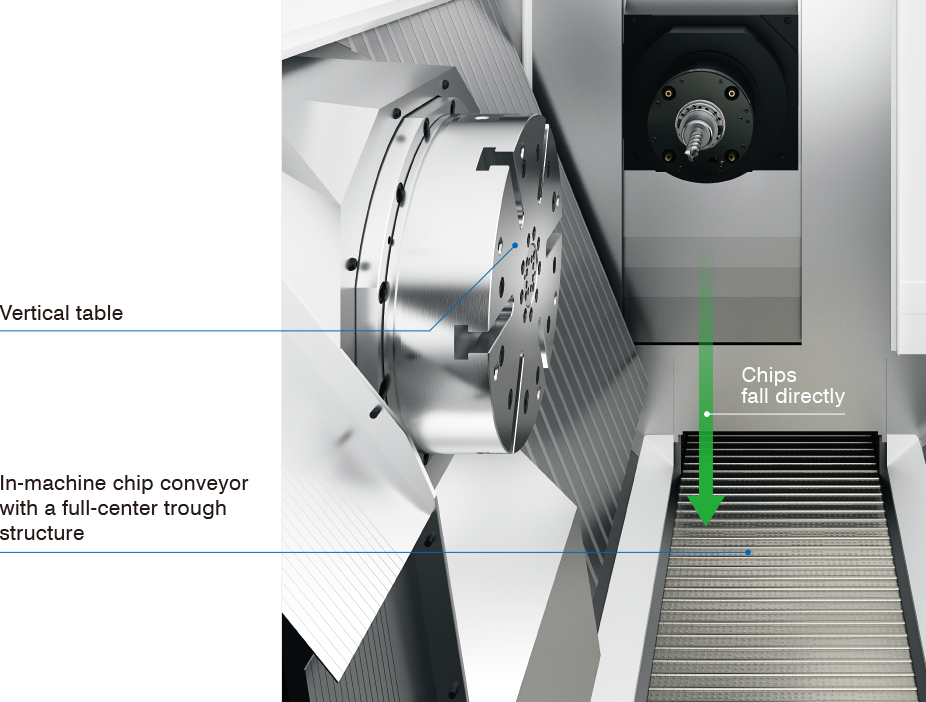
High productivity Compact yet capable of powerful cutting
This compact machine delivers precise cutting performance while reducing wasted time
Equipped with a powerful No. 40 spindle as standard, capable of machining steel parts with ease
The machine features a powerful No. 40 spindle, standard-equipped to effortlessly machine steel parts, delivering high-power cutting performance despite its compact size.
Spindle speed |
15,000min-1 |
---|---|
Max output |
25/11 kW (15%ED/Cont) |
Max torque |
73.1N・m(15%ED) |
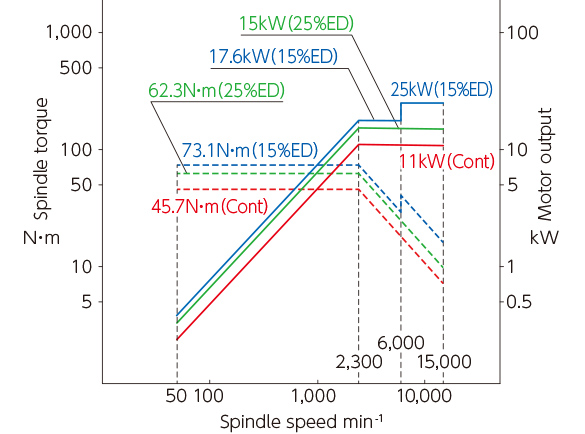
Non-cutting time is shortened through high-speed movements
An ATC electric shutter, which shortens non-cutting time, is installed as standard
ATC electric shutter
The ATC shutter opening/closing time is shortened
Tool change time is reduced through the synchronous control of the shutter and the tool change arm
The standard-equipped ATC electric shutter allows precise positioning of the shutter, enabling synchronous control with the tool change arm to eliminate wasted movements and reduce tool change time. Furthermore, it eliminates issues caused by shock during shutter operation, which were common with air-driven types, contributing to more stable machine performance.
ATC shutter operating time: |
0.4 sec |
---|
The standard-equipped ATC electric shutter reduces non-cutting time
Feed axes (X, Y, Z-axis)
Rapid traverse |
X・Y-axes 50m/min |
---|---|
Rapid traverse acceleration (max) |
1.0G |
Table (A-axis)
Rapid traverse |
X・Y-axes 50m/min Z-axis 60m/min |
---|---|
A-axis indexing accuracy / repeatability |
±3 sec / 2 sec |
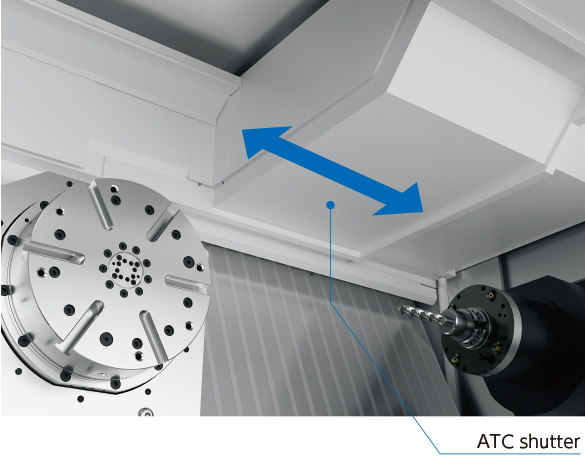
Highlighted Specs
Item | Unit | MS-320H | |
---|---|---|---|
Travel | X-axis travel | mm (in) | 250 |
Y-axis travel | mm (in) | 250 | |
Z-axis travel | mm (in) | 570 | |
Table (A-axis) | Pallet size | mm (in) | ø320 |
Max load capacity | kg (lb) | 100 | |
Max workpiece dimensions | mm (in) | ø500 × 400 | |
Spindle | Spindle speed | min-1 | 15,000 |
Tapered bore | 7/24 taper No.40 [HSK-A63] | ||
Feed rate | Rapid traverse | m/min (ipm) | X・Y・Z:60 |
Motors | Spindle | kW (hp) | 25/11 (15%ED/Cont) |
ATC | Tool shank | MAS403, BT40 [HSK-A63] | |
Pull stud | MAS2 [MAS1, CAT, DIN, JIS] | ||
Magazine capacity | tools | 10 [24] | |
Machine Size | Height | mm (in) | 2,630 |
Floor space; width × depth | mm (in) | 1,580 × 3,120 | |
Mass | kg (lb) | 7,000 | |
Controller | OSP-P500M |
[ ]: option