PRODUCTS
Watch the videos
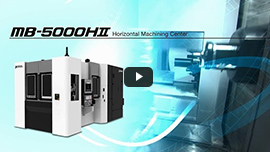
- MB-5000HⅡ
- That will enable various forms of fabrication, from mass production to variable-mix, variable-volume applications, to achieve optimum, full-scale processing at the fastest speed possible, with the MB-5000HⅡ.
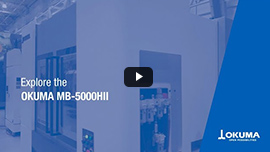
- Demonstration
- The MB-5000HⅡ offers quick acceleration, short tool changes, and high power to improve productivity.
- Achieving high-speed performance
in the world's fastest class - Fast machining of aluminum parts in mass production
- With fast acceleration/deceleration axis feeds for shorter positioning times, high-speed B-axis rotation (table), high-speed ATC, plus high-speed hole making
— all effective toward achieving world’s fastest class level cycle times. -
High-speed machining example of aluminum mass production
The cycle time became 34% less compared to the previous machine.
-
-
- Reduced positioning times
-
With fast accel/decel axis feeds designed to reduce positioning times:
- Rapid traverse acceleration (max) :
- X axis: 1.0 G
Y axis: 1.1 G
Z axis: 1.0 G
-
- Machining Time Shortening Function
-
MTSF shortens machining time in operations with repeated rapid traverse (G00) and cutting feed (G01) movements for parts with many drilled holes.
(The amount by which machining time is reduced will differ depending on machine setup, machined part shape, and part program.)
-
- Reduced table indexing times
-
A roller gear cam mechanism is used for the 0.001-degree indexing table (Optional), and that has minimized indexing time. Fast indexing has been achieved.
- 90° indexing: 1.0 sec*
- 180° indexing: 1.2 sec*
*With 0.001° indexing table (Optional)
-
- Reduced ATC times
-
The ATC disk magazine provides faster operations.
The farthest tool magazine indexing time possible is 5.1 seconds.- ATC tools: 48 (No. 40 spindle)
-
- T-T time:
- 0.9 sec (tool mass: 4kg or less)
1.3 sec (tool mass: 4kg or higher)
- Farthest pot indexing:
5.1 sec (With 48-tool magazine)
- The lineup of highly rigid and highly torqued spindles
- Also handles powerful cutting of steel
-
The lineup of spindles with roller bearings, compared to ball bearings, has higher rigidity. (Optional)
In addition to No. 40 spindles, No. 50 spindles are also available. With large-diameter side cutters and long boring bars etc, deep hole and protruding cut applications can be handled.
[Max tool length: 510 mm, max tool weight: 12 kg (No. 40 spdl), 15 kg (No. 50 spdl)]
- Power spindles (Nos. 40/50) (Options)
- For mass production of castings, cast steel
- Spindle speed: 12,000min-1 / Max output: 33/26kW (10 min/cont) / Max torque: 302N・m (10%ED)
Tool | Spindle speed min-1 |
Cutting m/min |
Feed rate mm/min |
Cut width mm |
Cut depth mm |
Chips cm3/min |
---|---|---|---|---|---|---|
ø100 face mill 5 blades | 955 | 300 | 1,910 | 70 | 4.7 | 628 |
ø20 roughing end mill 7 flutes | 4,029 | 253 | 8,800 | 4 | 20 | 704 |
(S45C)
- Standard spindle (No. 40)
- For highly efficient machining of general machine parts
- Spindle speed: 15,000min-1 / Max output: 26/18.5 kW (10 min/cont) / Max torque: 199/146N・m (5 min/cont)
Tool | Spindle speed min-1 |
Cutting m/min |
Feed rate mm/min |
Cut width mm |
Cut depth mm |
Chips cm3/min |
---|---|---|---|---|---|---|
ø80 face mill 8 blades (cermet) | 1,194 | 300 | 3,750 | 56 | 2.3 | 483 |
(S45C)
- High-speed spindle (No. 40) for aluminum applications (Optional)
- For fast machining of aluminum
- Spindle speed: 20,000min-1 / Max output: 30/22kW (10 min/cont) / Max torque: 57/42N・m (10 min/cont)
Tool | Spindle speed min-1 |
Cutting m/min |
Feed rate mm/min |
Cut width mm |
Cut depth mm |
Chips cm3/min |
---|---|---|---|---|---|---|
ø63 face mill 5 blades (carbide) | 15,000 | 2,949 | 20,455 | 44 | 3 | 2,700 |
(A5052)
*The data shown here represent "actual data," which may not be obtained under different specifications, tooling, cutting, and other conditions
- Chip discharge designed to achieve maximum operating times
- Machining chamber with accumulated chips and biting into covers — thoroughly removed
- In-machine covers renewed. Flat covers are used to drastically improve chip discharge. Moreover, with simpler designs, chip accumulation and biting-in troubles have been prevented. The machine has the high durability fully capable of withstanding the long continuous runs required for mass production at maximum rapid-traverse rates and machining capacity.
Highlighted Specs
Item | Unit | MB-5000HⅡ |
---|---|---|
Pallet size | mm (in) | 500 × 500 (19.69 × 19.69) |
Max work size | mm (in) | ø800 × 1,000 (ø31.50 × 39.37) |
Spindle speed | min-1 | 15,000 |
Tool storage | tools | 48 |
Motor | kW (hp) | 26/18.5 (10 min/cont) (35/25) |
Machine size (W × D × H) |
mm (in) | 2,540 × 5,620 × 2,893* (100.00 × 221.26 × 113.90) |
* With RDF drum filter lift-up chip conveyor