PRODUCTS
Supporting a wider range of applications with a new spindle lineup
Powerful new spindle: 10,000 min-1 No.50 (option)
Handling a wide range of applications from heavy-duty to high-feed machining
- Spindle speed: 10,000min-1
- Max output: 45/30 kW (20 min, 60% ED/cont)
- Max torque: 652/349 N-m (15% ED/cont)
- Machining capacity: 1,240cm3/min (S45C), 1,496cm3/min (FCD450)
Note: The "actual data" referred to above represent examples, and may not be obtained due to differences in specifications, tooling, cutting condition, and others.
Other spindle variations
Mainly for steel workpieces
Standard spindle No. 50
- Spindle speed: 6,000 min-1
Machines materials from aluminum to steel
Wide-range spindle No. 50 (option)
Max output: 45 kW (1.2 times more than previous model)
- Spindle speed: 12,000 min-1
Machines inconel, titanium and other difficult-to-cut materials
High-torque spindle No. 50 (option)
Max torque: 1,071 N-m (heavy duty cutting)
- Spindle speed: 6,000 min-1
Steel machining
Wide-range spindle No. 40 (option)
- Spindle speed: 15,000 min-1
Die/mold and aluminum machining
High-speed spindle HSK-A63 only (option)
- Spindle speed: 20,000 min-1
Optimal travels for the large parts applications
Higher floor space productivity with larger work envelope
Work envelope
X-axis travel: 1,050 mm (longer than previous machine)
Y-axis travel: 900 mm
Z-axis travel: 1,000 mm
Max load workpiece size
ø1,050 × 1,200 mm*1, *2 (larger than previous machine)
*1. Standard 2-pallet APC only
*2. From pallet top to 120 mm up, max workpiece diameter is ø1,000 mm
Max tool length
630 mm*3 (option) (longer than previous machine)
*3. Chain magazine only
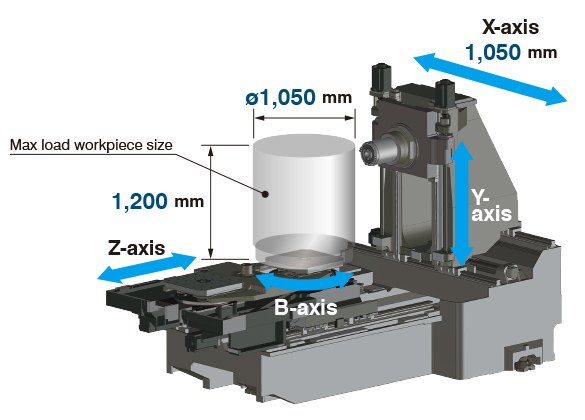
Outstanding dimensional stability even for long-run machining of large workpieces
Thermo-Friendly Concept
The unique approach of "accepting temperature changes."
Okuma's Thermo-Friendly Concept achieves high dimensional stability not only when the room temperature changes, but also at machine startups or when machining is resumed. To stabilize thermal deformation, warming-up time is shortened and the burden of dimensional correction during machining restart is reduced.
MA-600HⅢ Thermal deformation over time:
7 µm (room temperature change: 8℃)
Note: The "actual data" referred to above represent examples, and may not be obtained due to differences in specifications, tooling, cutting condition, and others.
Productivity improved by shortening non-cutting time
Shorter tool change times are possible when using thru-spindle coolant
- Suction of excess coolant in spindle
Removes residual coolant in the tool and spindle in one draw: 0.4 seconds *1 (drill actual data). In-spindle coolant suction eliminates the need for an air blow (minimum 15 seconds) to remove residual coolant, shortening tool change time.
*1. Coolant suction time varies depending on the tool.
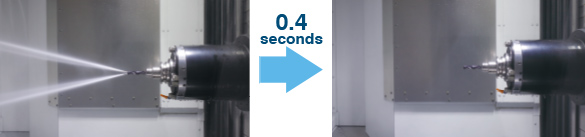
Shorter table indexing times
Table indexing time is shortened by the SERVONAVI Rotary Axis Inertia Auto Setting function.
Table indexing time [1 degree indexing]
1.6 sec/90°*2 20% reduction (compared to previous model)
Table indexing time [0.001 degree indexing]
1.4 sec/90°*2 44% reduction (compared to previous model)
*2. At low inertia
Chip discharge that maximizes uptime
With simple workspace covering and reinforced coolant applications,
Just Z-axis travel single cover and a smooth X-,Y-axis telescopic covers suppress chip accumulation.
Moreover, in dry machining without coolant, washing only the lower workspace area with coolant is possible.
In-machine washing prevents likely areas of chip accumulation, by cleaning away chips to maintain long-run production runs.
Chip discharge and workspace area designed to prevent chip accumulation
In-machine wash coolant: 450 L/min (18% improvement compared to previous machine)
Stronger workspace lower area wash and hinge conveyor smoothly removes large-volume coolant and accumulated chips out of the machine.
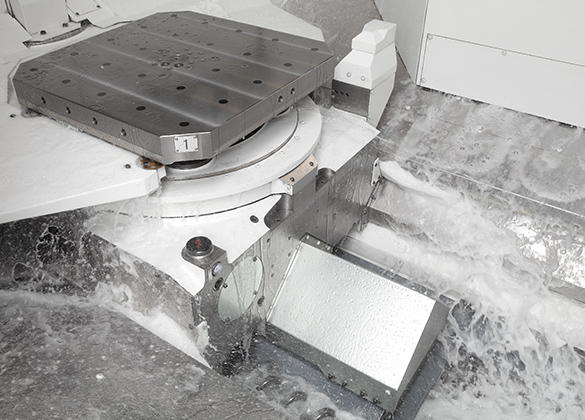
From the upper area of the workspace, a shower coolant system (option) and coolant from the X-,Y-axis telescopic covers suppress chip accumulation.
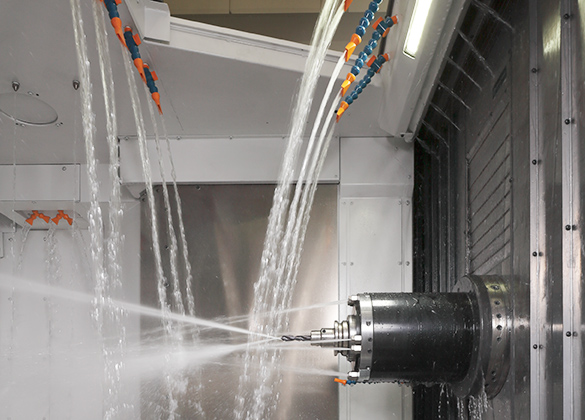
“Sludgeless Tank” enhances stable operations (recommended option)
Suppresses sludge accumulation in the coolant tank.
Dramatically reducing troublesome tank cleaning work
It is important to remove impurities (sludge) contained in the coolant for stable operation of the machine, and coolant tank cleaning is indispensable. The Sludgeless Tank (recommended option) efficiently collects 99% of the amount of sludge and reduces coolant contaminants. By suppressing sludge accumulation in the tank, the frequency of troublesome tank cleaning can also be drastically reduced, enabling stable operations over long runs.
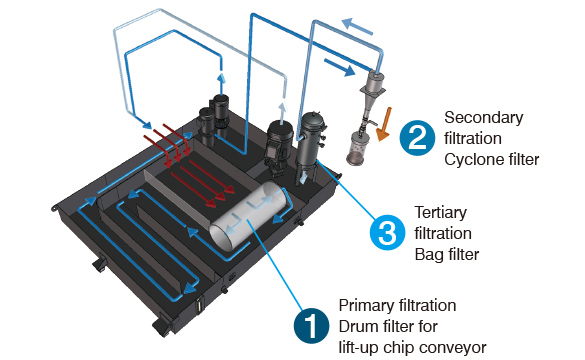
Highlighted Specs
MA-600HⅢ | ||
---|---|---|
Pallet size | mm (in) | 630 × 630 (24.80 × 24.80) |
Max work size | mm (in) | ø1,050 × 1,200 (ø41.34 × 47.24) |
Spindle speed | min-1 | 6,000 |
Tool storage | tools | 60 |
Motor | kW (hp) | 30/22 (10 min/cont) (40/30) |
Machine size (W × D × H) |
mm (in) | 3,435 × 7,068* × 3,174 (135.24 × 278.27 × 124.96) |
* With EC drum filter lift-up chip conveyor