PRODUCTSNEW PRODUCTS
Increased machining capacity with a powerful 10,000 min-1 spindle (option)
Handling a wide range of applications from heavy-duty to high-feed machining
Delivering high machining capacity across a wide range of low to high speeds.
Effectively handles a wide range of workpieces from heavy-duty cutting of steel to aluminum machining.
Powerful new spindle: 10,000 min-1 No.50 (option)
- Spindle speed: 10,000 min-1
- Max output: 45/30 kW (20 min, 60% ED/cont)
- Max torque: 652/349 N-m (15% ED/cont))
- Milling capacity 1,157 cm3/min (S45C), 1,389 cm3/min (FCD450)
Note: The "actual data" referred to above represent examples, and may not be obtained due to differences in specifications, tooling, cutting condition, and others.
Spindle variations
Mainly for steel workpieces
Standard spindle No. 50
- Spindle speed: 6,000 min-1
Machines materials from aluminum to steel
Wide-range spindle No. 50 (option)
Max output: 45 kW (1.2 times more than previous model)
- Spindle speed: 12,000 min-1
Machines inconel, titanium and other difficult-to-cut materials
High-torque spindle No. 50 (option)
Max torque: 1,071 N-m
- Spindle speed: 6,000 min-1
Higher floor space productivity with larger work envelope
Optimal travels for the large parts applications
With longer X-, Y-, and Z-axis travels, a wider range of applications can be handled.
Larger work envelope
X-axis travel: 1,400 mm (longer than previous machine)
Y-axis travel: 1,200 mm (longer than previous machine)
Z-axis travel: 1,350 mm (longer than previous machine)
Load capacity
3,000 kg (option) (more than previous machine)
Max workpiece size
ø1,450 × 1,450mm
Max tool length
800 mm (option)
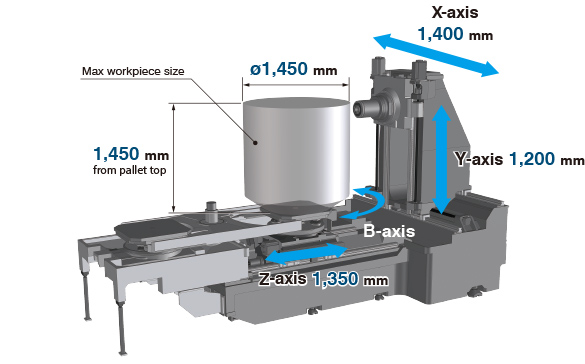
Chip discharge that maximizes uptime
With simple workspace covering and reinforced coolant applications, efficient chip discharge and long-run machining possible
Just Z-axis travel single cover and a smooth X-, Y-axis telescopic covers suppress chip accumulation.
Moreover, in dry machining without coolant, washing only the lower workspace area with coolant is possible.
In-machine washing prevents likely areas of chip accumulation, by cleaning away chips to maintain long-run production runs.
Chip discharge and workspace area designed to prevent chip accumulation
-
Stronger workspace lower area with large-volume coolant wash and hinge conveyor smoothly removes accumulated chips out of the machine.
-
From the upper area of the workspace, a shower coolant system (option) and coolant from the X-, Y-axis telescopic covers suppress chip accumulation.
"Sludgeless Tank" enhances stable operations (recommended option)
Suppresses sludge accumulation in the coolant tank Dramatically reducing troublesome tank cleaning work
It is important to remove impurities (sludge) contained in the coolant for stable operation of the machine, and coolant tank cleaning is indispensable. The Sludgeless Tank (recommended option) effectively removes sludge and reduces coolant contaminants. By suppressing sludge accumulation in the tank, the frequency of troublesome tank cleaning can also be drastically reduced, enabling stable operations over long runs.
Coolant sludge removal, less environmental impact when disposing coolant
- Sludge removal rate
- 99%*
(for castings) - 97%*
(for aluminum)
Note: After tertiary filtration (bag filter) permeation
Okuma evaluated removal rate
Automation support to further improve productivity
Flexible automation support
Equipped with a large number of thru-pallet fixture ports (option)
The setup station pallet base can be equipped with up to 16 fixture ports for hydraulic and pneumatic pressure, and the workspace area table base can have up to 8 ports for flexible automation applications. Simplifying complex hydraulic circuits is possible, making it easier to design auto-clamp fixtures. Customers benefit from more agile system building to handle diverse automation requirements.
Auto Setup Station Pallet Rotate (option)
This feature automatically rotates the setup station pallet in 90° increments by stepping on the foot switch.
Operator efficiency has been improved, and robotic part load/unload can be done from multiple fixtures.
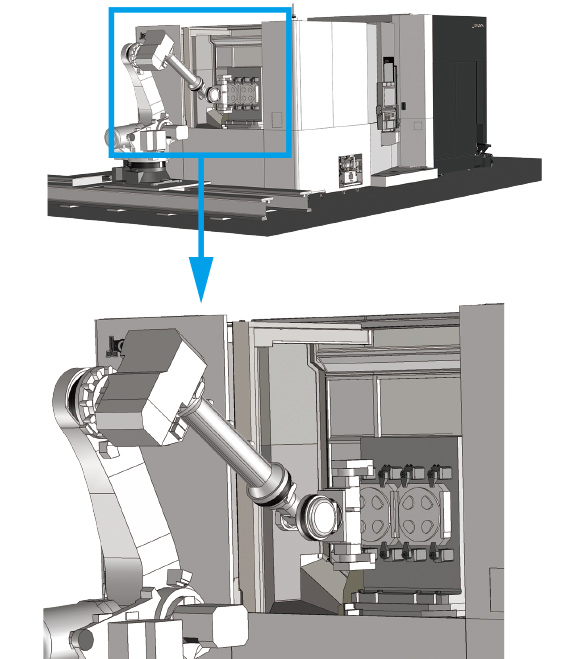
An impressive lineup of automation systems
Flexible APC systems
Multi-pallet APCs allow the operator to single setup a large number of workpieces, and use the extra time available for other jobs. Setups at the end of the day for untended operations are also a benefit.
- Multi-pallet APC connects to standard 2-pallet rotary-shuttle APC
- Pallet change time is the same as in the standard APC
- Can be adapted to match plant layout and type of production
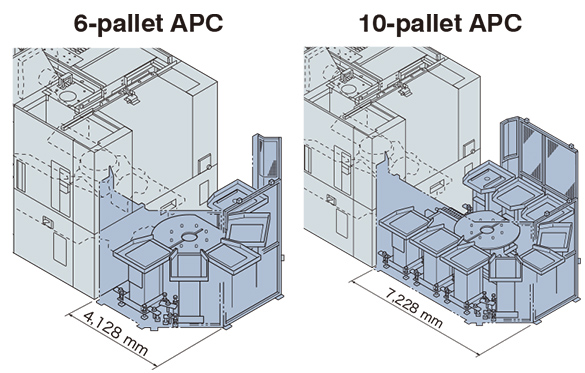
Auto tool changer
The standard number of tools that can be stored is 60. Flexible, high-volume tool storage systems available for adding more types of workpieces.
Matrix magazines store larger numbers in compact, quick tool-change arrangements.
Highlighted Specs
Item | Unit | MA-8000H |
---|---|---|
Pallet size | mm (in) | 800 × 800 (31.50 × 31.50) |
Max work size | mm (in) | ø1,450 × 1,450 (ø57.09 × 57.09) |
Spindle speed | min-1 | 6,000 |
Tool storage | tools | 60 |
Motor | kW (hp) | 30/22 (10 min/cont) (40/30) |
Machine size (W × D × H) |
mm (in) | 3,960 × 8,178* × 3,442 (155.91 × 321.97 × 135.51) |
*Off-machine chip discharge; hinge + scraper with drum filter (Recommended).