PRODUCTS
Watch the videos
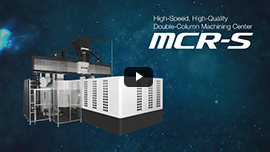
- MCR-S
- Double-column machining center MCR-S (Super) achives high accuracy and process-intensive machining of automobile press dies.
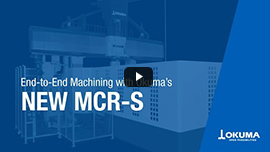
- Video Brochure
- The MCR-S roughs and finishes press dies in one setup and is designed for heavy-duty machining of process-intensive press dies for the automotive and aerospace industries.
Super fast, high-quality machine achieves
innovative production of press dies
Striving to provide the high speed, accuracy, and surface quality required for die/mold machining. Lead times are significantly reduced by reducing post-process polishing and upper/lower mold alignments.
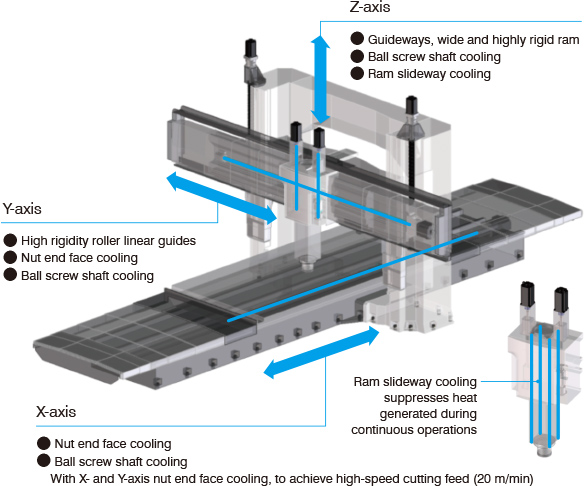
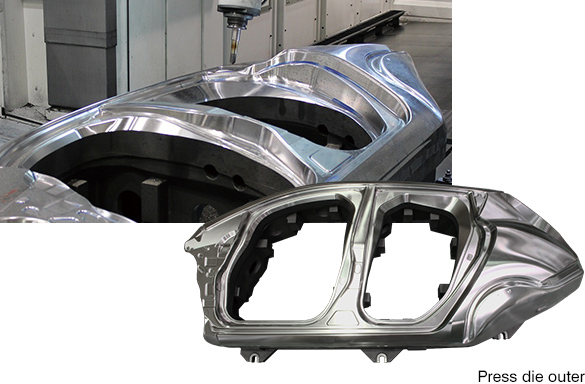
Industries
Installed in machine shops producing high-quality automobile press dies for sharp edge and smooth curve applications.
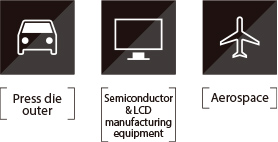
Feature
01 High speed Achieves class fastest continuous cutting feed while maintaining high shape accuracy and surface quality
Mechanical structure enables high-speed continuous cutting feed and 20,000 min-1 high-speed attachment head applications
Achieving 25% shorter cycle times while maintaining shape accuracy with optimum cooling. The machine design ensures minimal following error even at fast feed rates.
-
Average continuous cutting feed rates
X-, Y-axis: 20 m/min
Z-axis: 10 m/min -
Cycle times
25% less * (Previous machine: 7 hr 13 min; MCR-S: 5 hr 25 min)
* Automobile side panel machining compared to the previous machine.
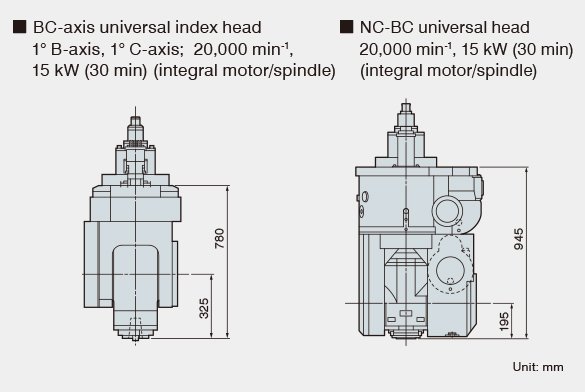
02 High surface quality Standard equipped specs achieve high surface quality dies
Hyper-Surface
Reducing hand finishing times
Achieving auto compensation of part program disturbances that lead to part defects, and high surface quality cuts that suppress machining surface ridges.
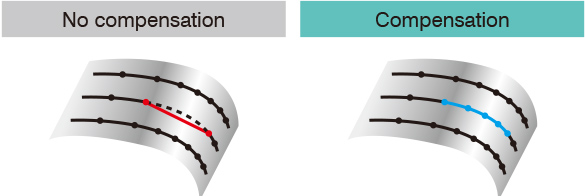
Thermo-Friendly Premium
Controlling thermal deformation in large machines
Z-axis tilt due to ambient temperature change reduced to 1.7 µm/200 mm, and step error to 10 µm or less.
AbsoScale (X-Y-Z-W axes)
Improved positioning accuracy for each axis
03 High efficiency From roughing to finishing,
machine rigidity withstands heavy cutting to reduce production lead times of complete molds with one machine
High torque and power integral motor/spindle
Heavy cutting with a powerful spindle reduces cycle times. Roughing to finishing with one machine also shortens setup change times significantly.
-
- Machining capacity:
- 710 cm3/min
(Workpiece: S45C; Z-axis protrusion: 800 mm, omnidirectional machining)
-
- Spindle speed:
- 10,000 min-1
-
- Max output:
- 26/22 kW (30 min/cont)
-
- Max torque:
- 735/622 N-m (30 min/cont)
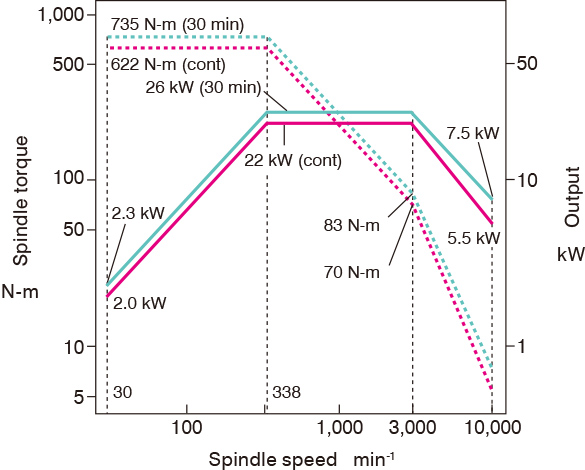
Note: The data shown here represent "actual data," which may not be obtained under different environmental, machine specifications, tooling, cutting, and other conditions.
Highlighted Specs
Item | Unit | MCR-S |
---|---|---|
Effective width between columns | mm (in) | 2,650, 3,150 (104.33, 124.02) |
Table working surface | mm (in) | 2,000 × 4,000 to 2,500 × 6,500 (78.74 × 157.48 to 98.43 × 255.91) |
Spindle speed | min-1 | 10,000 |
Tool storage | tools | 50 |
Motor | kW (hp) | 26/22 (30 min/cont) (35/30) |
Machine size (W × D × H) |
mm (in) | 7,370 × 10,730 × 6,420 to 7,870 × 16,430 × 6,700 (290.16 × 422.44 × 252.76 to 309.84 × 646.85 × 263.78) |