PRODUCTSNEW PRODUCTS
The innovation that accepts temperature changes
High accuracy can be achieved in normal factory environments
The machining accuracy of workpiece changes significantly due to the ambient temperatures around the machine, heat generated by the machine, and heat generated in machining.
The Thermo-Friendly Concept is a unique concept to “accepting” such temperature changes so that high accuracy can be achieved in normal factory environments with no special measures taken by the user.
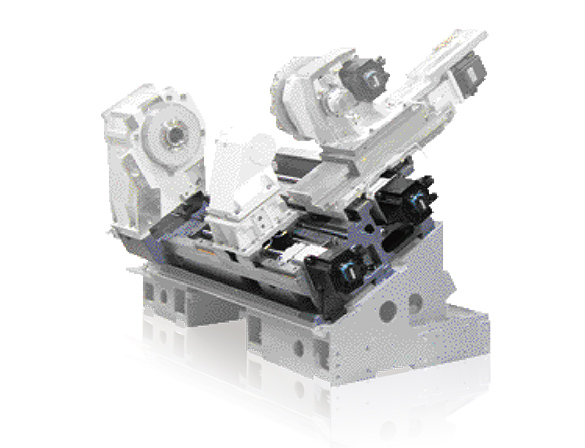
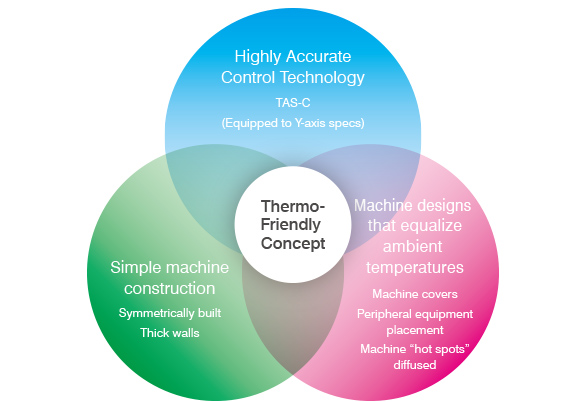
Achievement of both high accuracy and high productivity with emissions reduction and energy saving
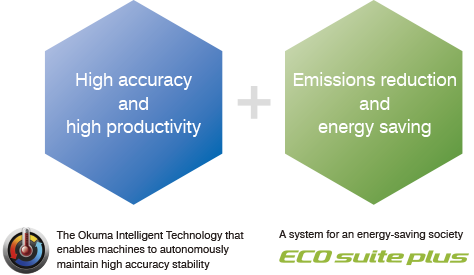
We chose the name “Green-Smart Machine” for our machine tool that achieves high accuracy and reduced energy consumption autonomously and realizes high productivity. With Green-Smart Machine, we will contribute to the solution of social issues faced by the global manufacturing industry, together with our customers.
High accuracy
The whole machine is designed to achieve high accuracy.
Outstanding dimensional stability enables stable machining of high-accuracy parts
and stable operation over long hours
Thermo-Friendly Concept is Okuma Intelligent Technology intended to achieve amazing machine accuracy with unique structual design and thermal deformation control technology.
It eliminates the need for cumbersome dimensional compensation and warm-up and demonstrates outstanding dimensional stability in long-term continuous machining, multitasking machine, front and back side machining with a sub spindle, and Y-axis machining.
Okuma Intelligent Technology to enable machines to autonomously maintain high accuracy in a stable mannerThermo-Friendly Concept
Machining dimensional change over time
ø5μm/Room temperature change of 8℃
* LB3000 EX Ⅲ (L specification) turning
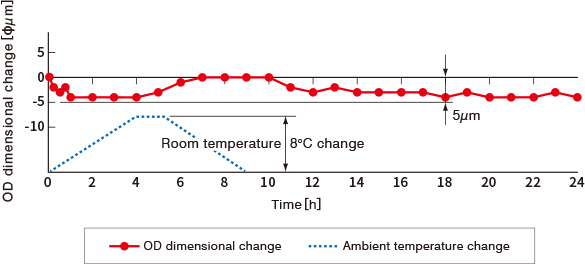
Note: The “actual data” referred above represent examples
and may not be obtained due to differences in specifications, tooling, cutting and other conditions.
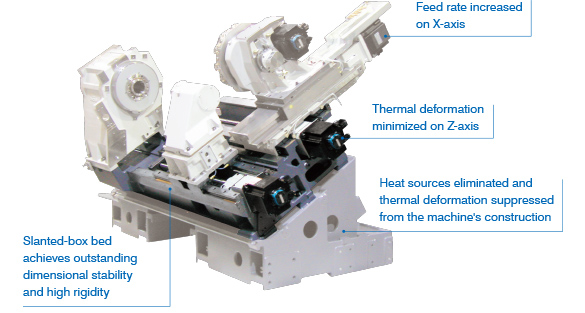
High productivity
Productivity is increased with powerful machining and quick machine movements
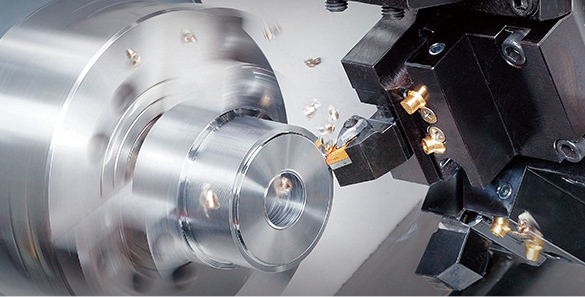
Equipped with a powerful motor |
LB3000 EX Ⅲ | LB4000 EX Ⅲ |
---|---|---|
Spindle size | Bearing ID ø120 mm (bore ø80 mm) |
Bearing ID ø140 mm (bore ø91 mm) |
Spindle speed | 5,000min-1 | 4,200min-1 |
Max output | 22kW | 30kW |
Turning capacity | LB3000 EX Ⅲ | LB4000 EX Ⅲ |
---|---|---|
Turning capacity (Material: S45C) |
4.4mm2〈actual data〉 | 6.6mm2〈actual data〉 |
Higher speed | LB3000 EX Ⅲ | LB4000 EX Ⅲ |
---|---|---|
Rapid traverse | X: 30m/min 20% shorter cycle time |
|
Z: 30m/min |
Highest milling performance in the class with high-speed movements and high accuracy
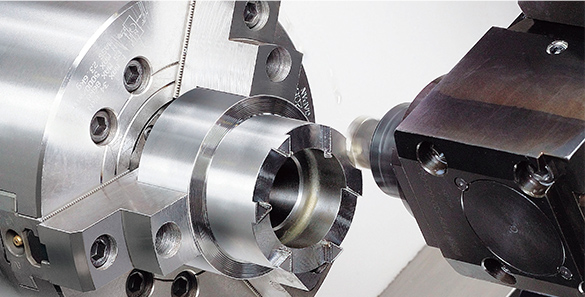
Equipped with a powerful motor | LB3000 EX Ⅲ | LB4000 EX Ⅲ |
---|---|---|
M spindle speed | 6,000min-1 | 6,000min-1 |
Max output | 7.1kW | 7.5kW |
Max torque | 40.4N・m | 58.1N・m |
Milling capacity | LB3000 EX Ⅲ | LB4000 EX Ⅲ |
---|---|---|
Milling capacity (Material: S45C) |
200cm3/min〈actual data〉 |
High-speed movements | LB3000 EX Ⅲ | LB4000 EX Ⅲ |
---|---|---|
Turret rotate | 0.1 sec/index | 0.2 sec/index |
M-spindle start/stop | 0.3sec (6,000min-1) |
0.4sec (6,000min-1) |
M-M switch (1 index) |
0.7sec | 1.5sec |
Automation
Optimal cell for mass-production machining of similar parts Loader
- It is effective for mass-production machining of similar parts
- The workflow line in front of the machine is secured by using the space above it
- It is possible to load/unload in a short time and achieve machining with a short takt time
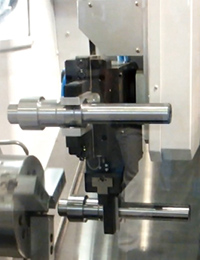
Compact, flexible, and labor-saving cell LB3000 EX Ⅲ ARMROID
- Automation is possible in existing spaces
- Ability to switch between automatic and manual operations depending on the production situation
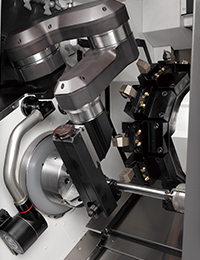
Highly versatile and applicable to irregularly shaped parts and high-mix workpiecesStand-alone articulated robot
- Highly versatile and applicable to irregularly shaped parts and high-mix workpieces
- Layout of peripheral devices is freely configurable
- Transfer between different machines, such as a lathe and a machining center, is possible
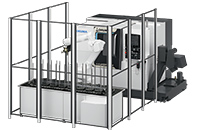
Photograph shows LB3000 EX Ⅲ
Realizing flexible productionA wide variety of peripheral devices
The automation and manpower saving of production lines is supported by workpiece turnover and other devices that are indispensable for connecting processes
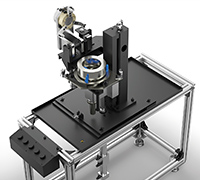
OSP
A next-generation CNC that makes customer manufacturing DX (digital transformation) a reality
Next-generation CNC 
Improved productivity and stable production
As Your Single Source for merging M-E-I-K (Mechanics - Electronics - IT - Knowledge) technologies, Okuma offers this CNC to build an advanced “digital twin” that faithfully reproduces machine control and machining operations and creates new value.
In addition, the product helps improve productivity and achieve stable production, featuring ease of use that allows customers to use their machining know-how. Additional features are: control technology that achieves high-speed and high-accuracy machining, energy-saving solutions that achieve both high accuracy/productivity and eco-friendliness, and robust security functions to protect against the increasing threat of cyber attacks.
- Faithful digital reproduction of machines and processing Ground-breaking concept of a digital twin
- Realizing high-speed and high-accuracy machining Leading-edge machining
- Novice-friendly smart operation Innovative operability
- Reducing environmental impact Energy-saving solutions
- Increasing cyber resilience Robust security
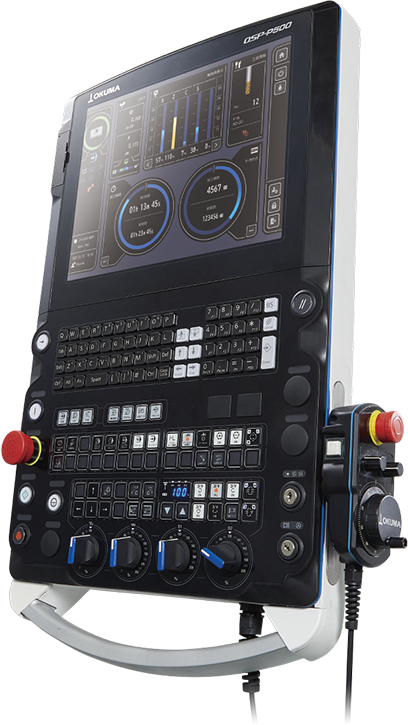
-
Home screen -
Virtual machining -
Preparation of the process chart -
Operation with the process chart -
MacMan plus
Highlighted Specs
Item | Unit | LB3000 EX Ⅲ | LB4000 EX Ⅲ |
---|---|---|---|
Standard chuck size | in | 8 | 10 |
Max turning dia | ømm (øin) | 410 (16.14) | 480 (18.90) |
Max work length | mm (in) | 500, 1,000, 1,300 (19.69, 39.37, 51.18) | 750, 1,500, 2,150 (29.53, 59.06, 84.65) |
Spindle speed | min-1 | 5,000 | 4,200 |
Turret | V12 | V12 | |
Motor | kW (hp) | 22/15 (30 min/cont) (30/20) | 30/22 (30 min/cont) (40/30) |
Machine size (W × D × H) |
mm (in) | 2,340 × 1,899 × 1,770 (92.13 × 74.76 × 69.69) 3,420 × 2,083 × 1,820 (134.65 × 82.01 × 71.65) 4,344 × 2,083 × 1,820 (171.02 × 82.01 × 71.65) |
3,100 × 2,059 × 1,955 (122.05 × 81.06 × 76.97) |
Specification Variations | M, W, MY, MW, MYW | M, MY, MW, MYW |
*M: milling specs, W: sub spindle specs, Y: Y-axis specs