- HOME
- Green-Smart Machine
"Green-Smart Machine" Declaration
As a step towards turning the decarbonized society into reality, Okuma has defined "Green-Smart Machine" as intelligent machine tools that contribute to resolving environmental issues by autonomously achieving both stable dimensional accuracy and reduced energy usage, and the company offers a full product lineup.
Okuma has been using automation and process integration as a part of its effort to reduce energy usage while still achieving high-productivity, high-accuracy machining for becoming carbon neutral at three Japan plants which are its main production bases. In addition to these measures, Okuma will start using green energy from October 2022, and its three plants in Japan will become carbon neutral plants ahead of schedule.
Okuma will produce these products in its carbon-neutral factories and provide them to the world, and together with its customers, Okuma will contribute to offering solutions for the social issues faced by the manufacturing industry.
Achieve higher productivity
and reduced carbon emissions at the same time
Decarbonization solutions only Okuma can provide
Okuma supports the reduction of power consumption and carbon dioxide emissions
from customer production plants by providing machine tools equipped with energy-saving technology,
to achieve a decarbonized society.
Green-Smart Machine
for realizing a decarbonized society
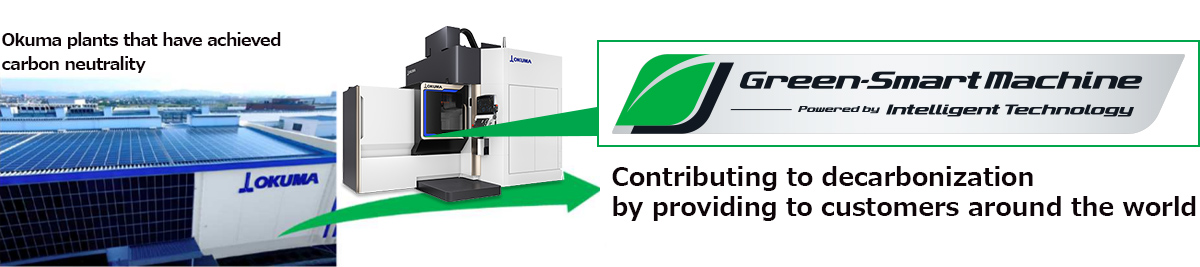
Reduction of power usage
by Green-Smart Machine
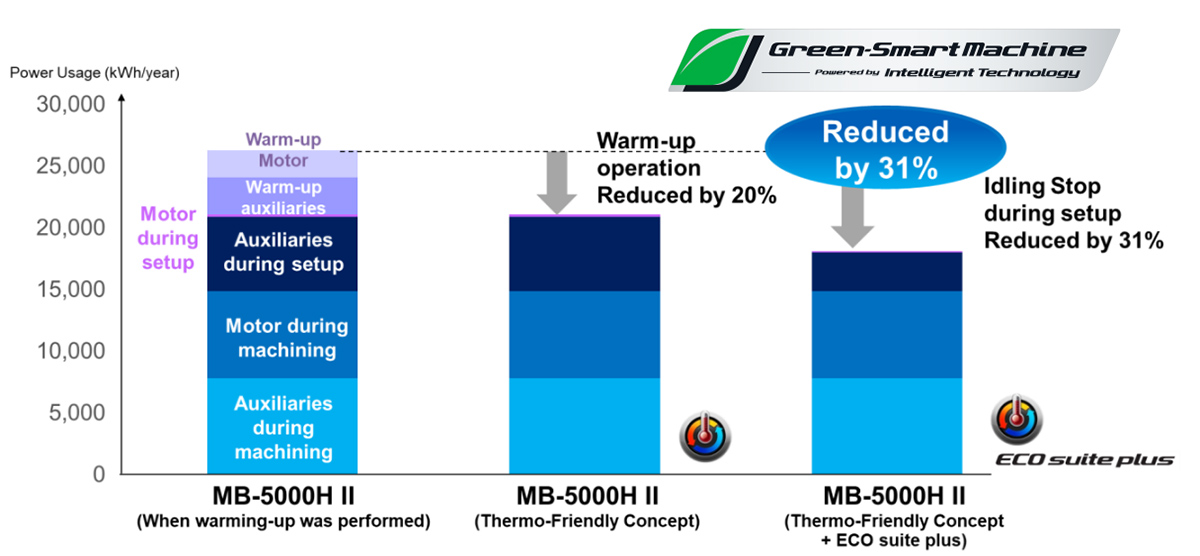
- [Calculations]
- MB-5000HⅡ
50% utilization (8 hr/da, 20 da/mo, 1 yr)- Assuming 50% of setup and standby time with ECO Idling Stop.
- Workpiece: Aluminum casing
- Average load: 30% rating
- Warm-up: 2 hr/da
- Calculated from measured regenerative power
Both stable accuracy and reduction of carbon dioxide emissions
Manageable Deformation—Accurately Controlled Thermo-Friendly Concept
From 2001 to September 2022
More than 60,000 units were produced
The workpiece machining accuracy changes significantly due to machine ambient temperatures, heat generated from in-machine components and cutting. The idea behind Okuma's Thermo-Friendly Concept is simply "accepting" these temperature changes so that high accuracy can be achieved in normal factory environments without requiring special customer preparations. Maintaining excellent accuracy stability is possible without relying on excessive ambient temperature control from machine cooling systems and factory air conditioners.
Next-Generation Energy-Saving System
From 2014 to August 2022
More than 42,000 units were produced*
* Including ECO suite, the predecessor function
The "ECO suite plus" retains the concept of achieving both high machining accuracy stability and energy savings (less carbon dioxide emissions) achieved by the Thermo-Friendly Concept and the "ECO suite" that was put into practical use in 2014. It is an energy-saving system with enhanced high-accuracy/-productive functionality and advanced eco-friendly support.
4 solutions only Okuma can provide
- 1Reducing energy during machining
-
Intelligent Technology Thermo-Friendly Concept
Both stable accuracy and reduction of carbon dioxide emissions
The workpiece machining accuracy changes significantly due to machine ambient temperatures, heat generated from in-machine components and cutting. The idea behind Okuma's Thermo-Friendly Concept is simply “accepting” these temperature changes so that high accuracy can be achieved in normal factory environments without requiring special customer preparations. Maintaining excellent accuracy stability is possible without relying on excessive ambient temperature control from machine cooling systems and factory air conditioners.
Shorter warm-up and
dimensional compensation times.[LB3000 EX Ⅱ compared to previous models]
High accuracy stability even at 1/3 less air
conditioning electricity.[Estimates: machine shop with 4 machines installed]
Outstanding dimensional stability without machine coolers
[DCMC actual data: 8℃ ambient temperature change]
Power Regeneration System
Using regenerative power during deceleration eliminates energy waste Standard on spindles and feed axes of all models
Wasting no energy by regenerating decelerating power—previously discarded.
Power Regeneration System benefits - [Calculations]
- Horizontal Machining Center MB-5000HⅡ 50% utilization (8 hr/da, 20 da/mo, 1 yr)
- Workpiece: Aluminum casing
- Average load: 30% rating
- Calculated from measured regenerated power
ECO Hydraulics (option)
Highly efficient hydraulic power pack reduces power consumption
- Conventional hydraulic unit
- MB-4000H actual data:
840 W
- ECO Hydraulics
- 25min-1
260W
[Pressurized]
- 2Stopping unnecessary equipment
-
ECO Idling Stop
Ensure accuracy and actively turn off unnecessary peripherals
All auxiliary equipment when not needed (most of factory power consumption), can be turned off.
The ECO Idling Stop button enables diligent idle stop operations even during machining and maintenance work.
The cooling system necessary for maintaining accuracy uses Thermo-Friendly Concept technology, and the machine itself decides when to cool and stop idling while maintaining high accuracy.
With ECO suite plus, the machine automatically detects the operating status, eliminating the need to push buttons while reducing carbon dioxide emission as much as possible without operator awareness.ECO Idling Stop energy savings - [Calculations]
- Horizontal Machining Center MB-5000HⅡ 50% utilization (8 hr/da, 20 da/mo, 1 yr)
- Assuming 50% of setup and standby time used ECO Idling Stop.
- Workpiece: Aluminum casing
- Average load: 30% rating
- Calculated from measured regenerative power
ECO Operation (option)
Peripheral equipment runs only when needed
By using only the required peripherals (chip conveyor, mist collector), energy-saving operations that also maintain high productivity are possible.
ECO suite plus enables more detailed tuning of operations to thoroughly support carbon dioxide emission reduction activities that do not reduce productivity.
- 3Shortening cycle times
-
Cycle Time Reduction (easy setting)
Significantly shortens cycle times and reduces power consumption
Cycle times become much shorter by selecting the optimal parameter settings for the workpiece and machining operation all at once.
- [Measuring conditions]
- Sample part program used to drill and tap dozens of holes on three sides of an aluminum die casting.
- 4Confirming and evaluating energy-saving efficiency
-
ECO Power Monitor
Evaluating energy savings and analyzing areas of reduced energy
Making it possible for the OSP control to analyze the operating status of each device.
-
① Check carbon dioxide emissions on the spot
With ECO suite plus, you can also check the power consumption of each device.
-
② Simultaneously records operating status and carbon dioxide emissions
With ECO suite plus, recording carbon dioxide emissions for each device, and data output is possible.
-
③ Analyze carbon dioxide emissions and improve machine tool operation
With ECO suite plus, not only the display on the machine but data analysis for each device is also possible on a PC, to see a more detailed carbon dioxide emission analysis.
MCR-BⅢ at DS3 Energy Consumption
-