GrinderGrinders that represent
the unique craftsmanship of Okuma
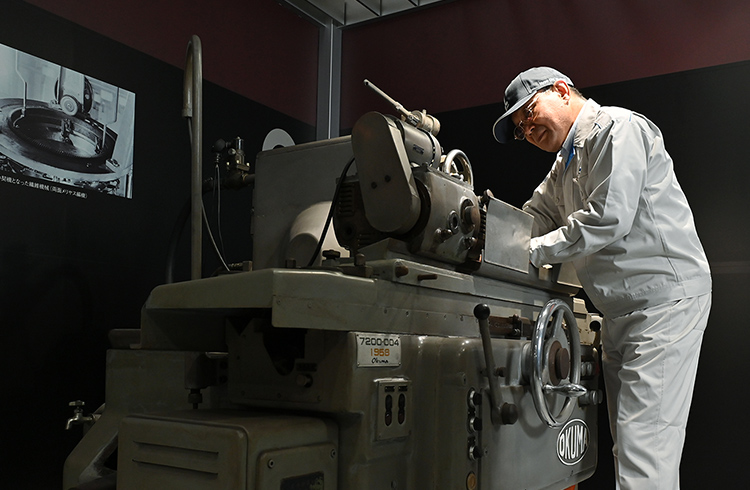
Request for repair of a grinder delivered 50 years ago
The grinders used in the final machining process require the most accurate parts machining and assembly. Involved in the assembly and repair of spindle units, the hearts of grinders, for more than 30 years and selected as a Contemporary Master Craftsman, the title of a top master, Yuji Kawamura has one particular memory he will never forget.
A request for repair of a special specifications GPB cylindrical grinder delivered to a customer more than 50 years ago had been brought to Mr. Kawamura one day. That machine is now displayed as Mechanical Engineering Heritage in the Okuma Memorial Gallery. When he disassembled and inspected it, he found that the unit had suffered serious damage, including seizing, due to poor maintenance, and the majority of its parts needed to be replaced. However, Mr. Kawamura concluded that it could not be repaired because there were no parts in stock or drawings for the machine and because it would take more than a year to complete the repairs even if he undertook them.
But the customer did not give up, saying, "This machine is used for critical machining that cannot be handled by other machines. I would like you to fix it no matter how long it takes or how much it costs." Ultimately, Mr. Kawamura manufactured all the parts for it from scratch, and with the full cooperation of the manufacturing department, he revived the machine in a year and a half, pouring all his knowledge, experience, and skills into it. The customer was extremely impressed, and Mr. Kawamura himself was filled with joy and a sense of accomplishment.
Unique craftsmanship that contributes to improving the quality of industrial products
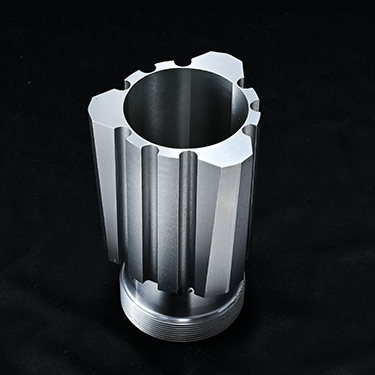
The reason why the customer was willing to wait a year and a half for the Okuma grinder was because they were attracted to Okuma's craftsmanship, represented by its bearing (Okuma non-round plain bearing), which could handle both heavy grinding and high-accuracy machining with strong retention strength and precise grinding wheel rotational accuracy.
Since it is a dynamic pressure type bearing that floats and supports the grinding wheel spindle with wedge-shaped oil film pressure, there is no metal-to-metal contact, and it has an innovative structure that can maintain its high performance semi-permanently, as long as maintenance is not neglected.
Developed in 1954, this bearing dramatically increased the machining accuracy of Okuma grinders, and this led precision parts manufacturers who produced the bearings and linear guides that determine the quality of industrial products to introduce Okuma machines one after another. This also significantly improved the quality of industrial products in Japan.
However, extremely advanced techniques and skills are required to manufacture these special bearings. In finishing, for example, mirror-finishing by lapping is required for the radial bearings that support spindles, while the thrust bearings that support end faces are wedged with a step of 1 μm or less by hand scraping.
Furthermore, if precision assembly cannot be performed with adjustment of the wedge angle and clearance so that they are optimal for the spindle bore diameter and spindle speed, high rotational accuracy and rigidity cannot be obtained. These critical processes are supported by the know-how of skilled workers who have acquired a wide range of experience and advanced skills.
I want to do something about it.
Let's try it! Don't give up!
In 2007, Okuma's grinders changed dramatically. The conventional belt drive system was converted into an integral motor/spindle drive system with built-in motor in the grinding wheel spindle in order to improve the rotational speed and accuracy of the grinding wheel spindle.
As a result, the bearing support parts, which were integrated with the grinding wheel spindle in the previous structure, were divided, and this required work to align the centers of each inner surface, so the difficulty of assembling the unit increased.
During the prototyping stage, the assembly department remarked that the structure would be complicated and that they were worried about being able to prevent misalignment. When Mr. Kawamura heard this, it sparked a feeling of wanting to do something about it, and he called on his colleagues to give it a try first and worked hard to find a solution. After much trial and error, he quantified the dimensional accuracy, which relied on the senses of expert engineers, and documented the alignment and adjustment work in a manual. In that process, he developed a feeler gauge, an instrument inserted into the inner surfaces of bearings and used as a reference for dimensions. Through dimensional control, he established a system to ensure that special skills were passed on to others, leading to stable manufacturing.
In this way, conversion to an integral motor/spindle for grinding wheel spindles got on the right track, and the value of Okuma grinders increased further, with rotational accuracy increasing from 0.02 to 0.01 μm and the maximum practical speed increasing from 2,000 to 6,000 rpm.
Based on this experience, Mr. Kawamura says, "The most important thing is not to give up easily." This is the craftsmanship that continues to live on in Okuma.
Keeping in mind work that brightens the corners
of the world and passing on skills to the next generation
Currently, Mr. Kawamura is teaching new employees Okuma's approach to monozukuri and basic work in the Monozukuri Dojo. He also conveys his approach to work, overlaying it with the path he has taken himself.
"Skills are your treasures and source of vitality. However, they cannot be learned and improved without effort. When each person exercises the skills they have honed in their own positions, they shine brightly as a whole." This is the Buddhist teaching that is now Mr. Kawamura's philosophy: "Itto Shogu, Banto Shokoku," which means one light may illuminate only a small area, but 10,000 lights gathered together will illuminate the entire country.
This also applies to the manufacturing of machine tools, which are made up of many parts, and is consistent with Okuma's mission statement: "Through total and consistent monozukuri service, Okuma aspires to contribute to the business of customers throughout the world who create value."
Master Craftsman of Okuma
Metalworking machine-tool assembler
YUJI KAWAMURA
- 1984
- Joined Okuma Iron Works Ltd. (current Okuma Corporation)
- 2009
- Selected as a Master Craftsman in Aichi
- 2020
- Selected as an outstanding skilled worker (Contemporary Master Craftsman)
- 2021
- Awarded the Medal with Yellow Ribbon
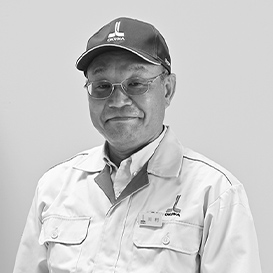