CNC Lathe / Multitasking MachineUncompromising craftsmanship
in the manufacturing of spindles
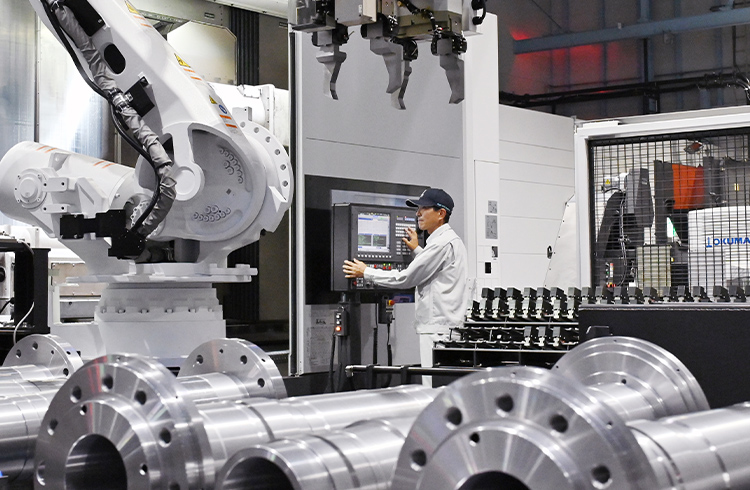
Even 1 μm outside the quality standards is failure
"Okuma's commitment to manufacturing spindles, the heart of a machine tool, feels like it is on a different level." says Yoshihiro Katsuda, a certified Master Craftsman in Aichi who has been involved in lathe machining for more than 30 years since joining the company. He honed his skills in the spindle machining section he was assigned to and was in charge of all types of spindle machining, from spindles for lathes, machining centers, grinders, and multitasking machines to attachments for double-column machining centers and mounting spindles for special tools.
The steps of the spindle manufacturing process are as follows: material cutting, forging, roughing, deep drilling, normalizing, turning finish, machining, anti-carburizing/carburizing, rough grinding, and finishing. In the process, strict quality and machining standards are established at critical points in each process, right up to the material for the blank material, the heat treatment method, straightening, and final grinding, and accuracies are checked.
"Even 1 μm outside the quality standards is failure. We always perform final finishing in-house to ensure compliance with Okuma's quality standards." explains Mr. Katsuda. Completed spindles and related parts are then assembled precisely in the unit assembly section (refer to Case 2 on this site) and mounted onto the machines.
To be machines that can always cut very well with precision
Because we introduce machine tools that are not inexpensive, we want them to always retain their cutting performance and machining accuracy and contribute to improvement of machining quality and productivity—this is a wish shared by all our customers.
However, you can encounter practical problems such as failures or malfunctions if you use the same machine for both roughing and finishing, noticeable variations in dimensions if heavy-duty and light cutting are performed repeatedly, and spindles not being able to withstand the performance of hard turning for process-intensive machining. These may be due to insufficient rigidity attributable to the machining and assembly accuracies of the spindles and bearings or insufficient rigidity related to the structure of the machine body.
Positioning the delivery of high-rigidity and high-accuracy machines free from such phenomena as a fundamental principle for design and manufacturing, Okuma enforces strict quality controls.
In fact, Mr. Katsuda still remembers the things he heard from customers when he was assigned to a manufacturing subsidiary in Taiwan to provide technical service guidance to distributors in Asia and technical guidance to partner companies: "The true value of high rigidity and high accuracy becomes apparent after using Okuma machines for 10 years." "The introduction of Okuma machines improved the status of my company." "We want to introduce the 5-axis machining center and multitasking machine from the cover of the catalog someday." as well as other comments.
Needless to say, every word of these customers provides great encouragement to all the employees of Okuma, including masters.
Turning the machining know-how of masters into Intelligent Technology
Okuma machines are known for their Intelligent Technology that revolutionizes the manufacturing, along with their high rigidity and high accuracy. Manageable thermal deformation, collision free, chatter free, auto adjustment to optimum machining conditions, and more—these innovative machining infrastructure technologies that support high accuracy and high productivity are the result of quantifying the tacit knowledge (know-how and intuition) of masters accumulated in Okuma's machine shops and applying it to digitally control machining.
Mr. Katsuda, a turning master, explained how to suppress chatter for slender workpieces as an example: "Chatter will inevitably occur if you cut slender workpieces at the same spindle speed. However, skilled craftsmen assess the material, shape, and tools for a workpiece and minimize chatter by adjusting the load applied and spindle speed. Machining Navi draws on these techniques in NC control to derive the optimum machining conditions."
He also said, "The Thermo-Friendly Concept that accurately controls thermal deformation, considered a representative Intelligent Technology, is also a feature that is only possible with high-precision parts machining and assembly technology. This control is easy because the machine deforms manageably in response to the ambient temperature as well as the thermal changes caused by machining. Therefore, the reason why the same machining accuracy as an Okuma machine cannot be achieved by other machines even if they adopt similar structures is that they are built differently."
Okuma's monozukuri (making things better than ever) is passed down to successive generations
How did you become a master? "At every place I was assigned, there were older generations of staff who were eventually called master craftsmen, and I learned everything from them, including ways of deriving optimum machining processes and procedures from drawings, a wealth of knowledge and practical skills, and accurate and fast ways of working," says Mr. Katsuda. At the same time, he gobbled up knowledge about not only spindle machining but also the processes before and after it. While he worked on a wide range of models, he was also involved in the installation of delivered machines and improved his capabilities as a multiskilled worker.
As an instructor in the Monozukuri Dojo, he strives to teach mid-career trainees all the skills he acquired based on this experience. His goal is for 100% of trainees to pass National Trade Skill Testing & Certification and to foster multiskilled workers. To this end, he is also focusing on machining training for younger workers at the Okuma Technology and Skill Tournament to raise the level of their skills.
In order to deliver products that exceed the expectations of customers who wish to someday introduce state-of-the-art Okuma machines, young trainees today work with machines and workpieces in the Dojo.
Master Craftsman of Okuma
Metalworking machine-tool mechanic
YOSHIHIRO KATSUDA
- 1985
- Joined Okuma Iron Works Ltd. (current Okuma Corporation)
- 2000 — 2001
- Assigned to Tatung-Okuma Co. Ltd. (Taiwan)
- 2007 —
- Aichi Prefecture Trade Skill Testing & Certification, Trade Skill Test Commissioner
- 2015
- 2015 Selected as a Master Craftsman in Aichi
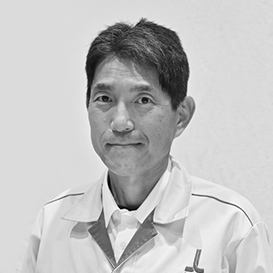