CNC Lathe / Multitasking MachineUsing skills and knowledge gained
from difficult machining to improve
customer production technology
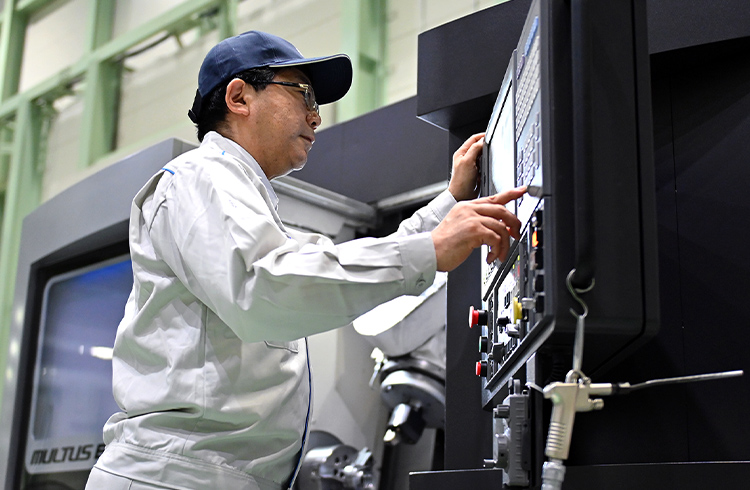
Selected as the youngest Contemporary Master Craftsman in history
In November 2012, Okuma received some delightful news. Isao Oyabu, a skilled NC lathe worker who had handled an array of difficult machining and been involved in delivery, installation, trial run, and operation guidance for machines both in Japan and overseas, was selected as a Contemporary Master Craftsman, the fifth case at Okuma. He was also the youngest person (at 50 years old) in history (at the time) to be selected in the field of numerical control metal machining.
He was selected because of his outstanding skills in machining slender shafts and thin-walled shapes, which are considered the most difficult tasks in lathe machining, including his ability to achieve a dimensional accuracy of Φ0.05 mm in machining slender shafts with a diameter of 7 mm and length of 150 mm and a roundness of 30 μm or less for thin workpieces with a diameter of 100 mm and wall thickness of 1.5 mm. He also made the most of his skills and contributed to solving problems for customers, such as improving machining accuracies and reducing cycle times through test machining before the delivery of NC lathes, as well as to product machining and guidance after delivery. In addition, he was also highly regarded for his dedication to the development of skilled workers, serving as a Central Trade Skill Test Commissioner of the Japan Vocational Ability Development Association as well as an overseas training instructor.
Proposing Okuma machines,
along with new machining methods and expert know-how
Mr. Oyabu, who later became one of our top masters, was greatly inspired as a rookie by the site of skilled workers who were challenging complicated shapes and strict tolerances at a customer's site when he visited to install a delivered machine.
"When I saw their methods of selecting tools according to the material and their machining methods and procedures for difficult shapes, I was surprised that such tools and jigs were being used and was inspired to try that kind of machining. And once I learned one skill, I tried to apply it to other workpieces. In this way, I gradually took on the challenges of difficult workpieces and pursued skills to achieve a good balance among machining time, machining accuracy, and tool life."
In saying so, what remains vivid in the memory of Mr. Oyabu is the machining of a cylinder liner, a cylindrical part made from cast iron that fits into the cylinder block of an engine.
This critical part requires a machining accuracy of 30 μm for roundness to ensure smooth reciprocation of the piston moving at high speeds while maintaining airtightness. At the customer's location, roundness could not be achieved by machining alone, so skilled workers finely adjusted the roundness by tapping on workpieces after turning. Reducing such post-processing would greatly improve productivity.
Mr. Oyabu learned about machining procedures, tools, and cutting conditions, such as cutting depth and feed, through repeated trial and error, never giving up. Ultimately, he achieved the targeted roundness by dividing the process among 4 machines.
Looking back on that time, he says, "Of course, it was satisfying to close a deal for Okuma machines, but the sense of accomplishment in establishing a machining method that can be completed through turning only and above all the smile on the customer's face were special."
There are many cases like this in which the outstanding skills and machining know-how of masters, combined with the performance of Okuma machines, have contributed to improving the processing accuracy and productivity of our customers.
Using the opinions of machine shops in product development
and passing on practical skills for techniques to the next generation
"High rigidity and high accuracy" and "user-friendly machines" always rank highly on the list when customers evaluate Okuma machines. The foundation for this is a culture that actively incorporates frank opinions from machine shops inside and outside the company.
When developing new models or new control systems, Mr. Oyabu, a master, was asked by the development and design departments to propose improvements from the standpoint of parts machining. He made proposals for experience-based points of improvement including suggestions for the layout of various types of equipment for easy machine access and easy tool change and suggestions for program input methods, which have been adopted.
In this way, each Okuma machine reflects ingenuity arising from the "standpoint of putting users first," and user-friendliness is evolving with every model and series.
On the other hand, the passing on of craftsmanship and skills is extremely important in an era with low hurdles to overcome for machine operation due to the ease of programming and high precision of machines. In the Monozukuri Dojo, Mr. Oyabu is responsible for improving the skills of skilled employees who have been with the company for 5 to 10 years, and he emphasizes this point:
"I have been involved in the installation of more than 150 machines and systems in Japan and overseas, and when we actually perform mass production on-site using mass-production machines, variations in machining dimensions and other phenomena sometimes occur. The ability to apply acquired skills is essential for making quick adjustments in such cases. For this reason, we deliberately have trainees in the Monozukuri Dojo manually assemble machining programs used in automated parts factories in order to train them in techniques and practical skills that they can accomplish on their own."
Contributing to improving the level of manufacturing in Asia
Okuma's masters don't just focus on training their own successors. As leaders in the industry, it is not uncommon for them to be examiners or involved in creating assignments for National Trade Skill Testing & Certification and to be dispatched as overseas training instructors.
Mr. Oyabu has also served as a training instructor in countries throughout Asia, thanks to his extensive experience in machine installation and operation guidance for overseas markets. In Singapore, for example, an Okuma machine was adopted as a training machine at a university, and he instructed faculty members for two weeks on a range of topics, from the creation of machining programs to the performance of actual machining.
In Vietnam, the Japan Vocational Ability Development Association was asked to cooperate in introducing a system equivalent to National Trade Skill Testing & Certification in Japan, and Oyabu traveled to Ho Chi Minh as an instructor for that project. He instructed about 40 teachers from vocational training schools on a range of topics, from the creation of a machine tool (competitor's product) program to the performance of actual machining and the development of scoring criteria for national testing.
At Okuma, we hope to continue to use such opportunities to contribute to improvement of the level of manufacturing in Asia.
Master Craftsman of Okuma
Numerically controlled metalworking machine-tool mechanic
ISAO OYABU
- 1980
- Joined Okuma Iron Works Ltd. (current Okuma Corporation)
- 2009
- Selected as a Master Craftsman in Aichi
- 2012
- Selected as an outstanding skilled worker (Contemporary Master Craftsman)
- 2019
- Awarded the Medal with Yellow Ribbon
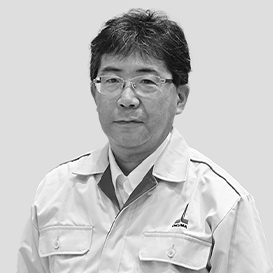