File 01
単体機の高機能化から
「工場全体の最適化」へ
LB3000 EX Ⅲが提示した
“ものづくりの未来”
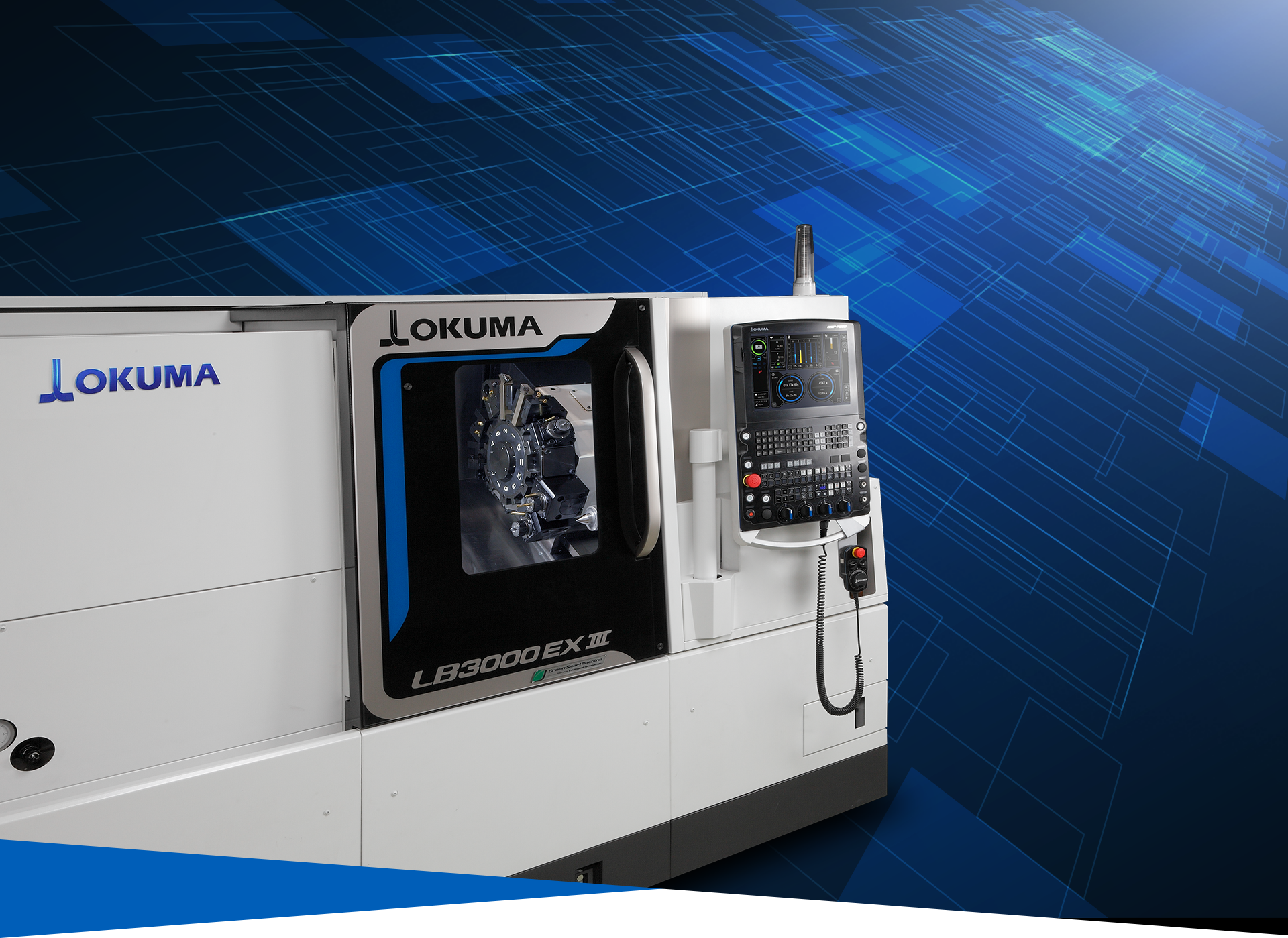
NC旋盤の名機LB-EXシリーズは、コンパクトながら重切削もこなす加工能力、抜群の寸法安定性、使いやすさが愛され、世界での累積販売台数は1万8,000台を超え、オークマを代表する機種の一つとなっている。
このベストセラーマシンが11年ぶりに生まれ変わった。その背景にあるのは、製造業が直面する「脱炭素・デジタル変革・労働力不足・技能継承」問題への対応である。これらのニーズに真正面から向き合った開発チームは、LB3000 EX Ⅲを誕生させた。
そこに至る彼らの想い、ものづくりの未来について語ってもらった。
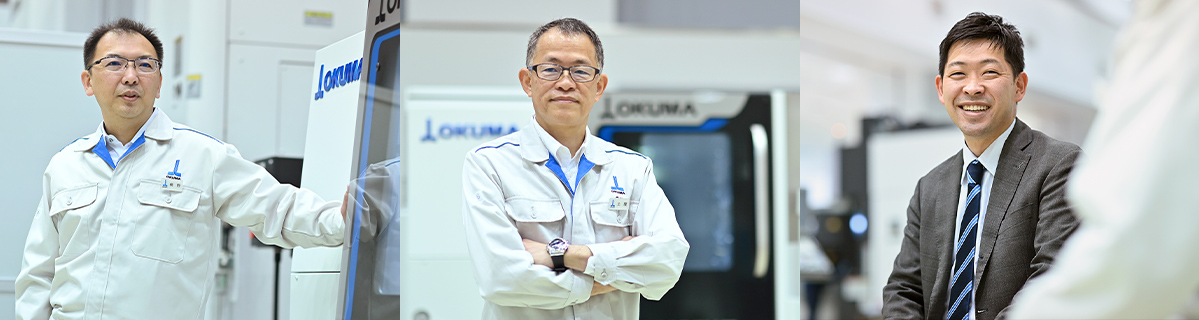
技術本部 ソリューション&システム技術部 次長 梶野 誠
技術本部 商品開発部 第三商品開発プロジェクト プロジェクトリーダー 土屋 昌史
営業本部 名古屋支店 安城営業所 販売主任 加藤 雄己
ロングセラーマシンは、
どのように進化したのか
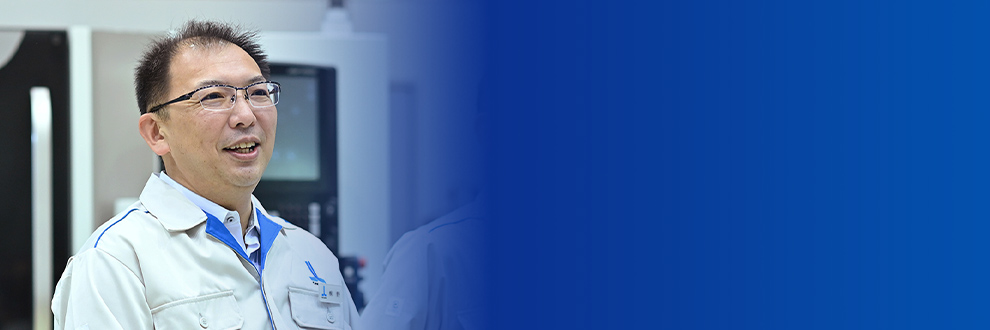
高精度で
止まらないことが基本ですソリューション&システム技術部 梶野 誠
オークマの旋盤といえば、多くの人が「LB」と口を揃える。その軌跡をたどると1982年に誕生したLB15形に遡る。当時、業種や企業規模、対象ワークサイズ・生産量が異なる多種多様なお客様に最適なNC旋盤を提供するため「コンパクトで耐久性が高く、購入しやすい価格の実現」を目指した。
そして、熱変位の小さいボックススラントベッド構造を採用したLB300(1998年)、最高レベルの複合加工能力、「経時加工寸法変化ø5μm」の高精度と共にワンチャッキングで完全工程集約で大きな支持を得たLB3000 EX(2006年)、そして操作性の更なる改善を図ったLB3000 EX Ⅱ(2012年)へと進化した。
「LBは数世代にわたって進化しましたが、お客様の隠れたニーズまで掘り起こして性能に反映させる開発姿勢や“高剛性・高生産・コンパクト”を追求する製品づくりは今なお不変です」。そう断言するのは、1990年代から歴代のLBシリーズの開発に携わり、最新モデルLB3000 EX Ⅲのプロジェクトリーダーも務めた土屋昌史である。
彼は「精度に関しては絶対に妥協しません。コストダウンのために軽量化や部品の一体化が議論されることがありますが、精度の要となる「サーモフレンドリーコンセプト(熱変位の制御)」には一定の重量が必要です。そのため構造的に譲れないところがあるのです」と強調する。
また、旋盤の営業技術職としてお客様と技術部門の橋渡しを担い、自動車産業の量産ラインや海外駐在経験も豊富な梶野誠は次のように証言する。
「量産工場では、精度不良や補正のためにチョコ停を繰り返すようでは信頼を得られない。その点、サーモフレンドリーコンセプトを適用したLB3000 EXは加工精度が非常に安定し、自動車関連のお客様からのリピート受注が相次ぎました。また、ドイツの販売拠点に5年間駐在し、欧州・アフリカ・中東地域を担当しましたが、LBの精度に関するクレームは聞いたことがありません。もちろん自動化や脱炭素化は重要ですが、まずは高精度で止まらないことが基本です」と。
工場が抱える
将来の課題まで見据えて
では、最新モデルには、どのような性能が求められたのか。開発プロジェクトは、ユーザー訪問やマーケティング会議などで国内外の声を収集・分析し、工場が抱える現在と将来の課題を整理し、CNC旋盤のあるべき姿を探った。
そして導き出したのが、「労働力や熟練技能者が減少する中で、厳しい精度要求や高い生産性を追求するにはさらなる工程集約、多様な自動化対応に加え、工場の稼働率を最大化するCNCが不可欠であり、さらには脱炭素社会にふさわしい機械が自律的に省エネできる環境性能を備え、これらをコンパクトに集約すること」だった。
そこには、工作機械にとどまらず「工場全体の最適化」や「工場経営の支援」まで視野に、ものづくり大変革時代におけるソリューション・プロバイダーを目指すオークマの決意があった。
基本に忠実で手離れの良い機械を
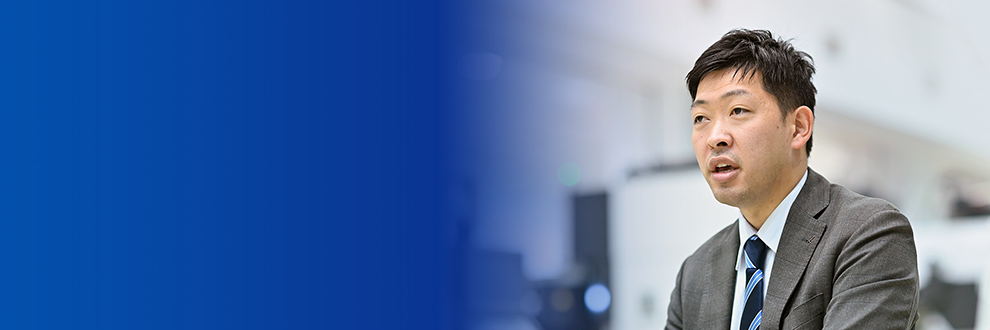
新世代CNC OSP-P500の操作性を
ぜひ体感いただきたい名古屋支店 加藤 雄己
2023年3月、満を持してLB3000 EX Ⅲを報道陣に披露した。
土屋はそこでも「自動化・省人化・無人化を進める前提として、機械の『加工精度が安定』し『止まらない』ことが不可欠です」と開発姿勢を披歴した。
労働人口が減っていく時代に手離れの良い機械、一度ボタンを押せば加工完了まで何もしなくてもよい機械が求められている。そのうえで多彩な機能が加わり、ミ―リングやギヤ加工・研削加工など単体でも複雑な加工もこなせれば、多品種・小ロット生産にも適用できる。それを具現化したのが今回の新型機だ。
「自動化」の追求では生産形態に合わせて導入しやすいシステムを用意した。量産に適したローダシステム、場所をとらない機内ロボット(ARMROID)、後付けで自動化できる自立型多関節ロボット…。特にティーチングの難しさが課題となっていたロボットは、始点と終点だけを指示すれば衝突しない動作経路を自動生成する「ROID Navi」によって機械操作の要領で動かせる。このようにオペレータの経験を問わない使いやすさに徹した配慮が随所に施されている。
「お客様がロボットの導入をためらうのは、設備投資に加え、ロボット言語の理解、資格取得、オペレータ教育、設置スペースの確保などが大きな負担だったからです。その点、オークマのロボットはビルトインタイプも取り揃え、OSPと同じ感覚で操作でき、システムインテグレータも不要です。この安心感は大きく、これなら扱えると納得いただけるでしょう」と開発陣は胸を張る。
さらに「新世代CNC装置OSP-P500の操作性をぜひ体感いただきたい」と強調するのは、販売主任として多種多様な加工現場と向き合う加藤雄己である。
「これまで画面の切り替えの多さに難しさを感じるお客様もありましたが、OSP-P500は画面遷移が少なく、オペレーションの快適さを実感いただけます。また、操作を教える技能者も減る中で、セットアップからプログラム、加工までをガイダンスしてくれる機能は非常に心強いものです」。
OSP-P500は、オフィスのPCで加工プログラムを作成・事前シミュレーションし、機械に転送すれば、初品加工における現場での試行錯誤を最小化し、機械の稼働率を最大限に高められる。シミュレーション機能は実加工時間の最大1000分の1というスピードで加工時間の誤差1%以下の超高精度である。
「オペレータの作業時間を短縮できれば機械稼働率が上がる。そうして生産性が上がれば、ワーク1個当たりの消費電力が節減でき脱炭素につながる。こうしたスマートなオペレーションが、普及していくのは間違いないでしょう」。
高精度・高生産性を維持したまま
消費電力を抑える
いま世界各国で脱炭素への取り組みが加速しているが、加工現場ではどうなのか?
「脱炭素は2020年頃まで大企業を中心とする課題でしたが、サプライチェーンを形成する一次・二次事業社も対象になってきました。特に最近は電気料金の高騰で消費電力への関心が高まっています」と梶野は語る。
オークマは、すでに20年以上前からこの課題の解決策を提示している。熱変位を最適制御するサーモフレンドリーコンセプトだ。機械を無理に冷やすのではなく熱を制御しやすい機械構造にする逆転の発想で驚異的な寸法精度を実現し、結果的に暖機運転や空調のエネルギー消費を最小限に抑える。この技術を適用したオークマの製品は、高精度・高生産性と省エネ(CO2削減)を両立できるのである。
近年ではこの技術を応用し、精度の維持に必要な冷却のタイミングを機械が判断し、不要な時は冷却装置をアイドルストップして消費電力を削減する(ECO suite plus)。さらにLB3000 EX Ⅲでは、前面ドアの開閉をエアからモータ式にするなど消費電力を抑えている。オークマは、このように「寸法精度の安定性」と「エネルギー消費量の削減」の両立を自律的に行う工作機械を「Green-Smart Machine」として全面展開している。
すべての土台となるのは
「機械精度のつくり込み」である
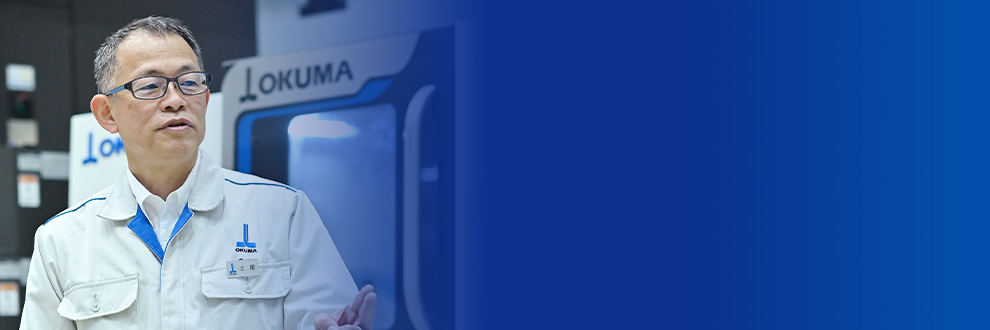
“機械精度のつくりこみ”を重視し、
開発から機械・電気・制御部門が一体となって
製品づくりを行っています商品開発部 土屋 昌史
生産性・複合加工・デジタル化・自動化など進化が著しいLB3000 EX Ⅲだが、最後にプロジェクトリーダーの土屋が、工作機械の本質について語った。
「近年、DXやIoTが注目され、工作機械にもデジタル技術が幅広く展開されています。しかし、我々が忘れてならないのは、金属を加工するのはあくまで“機械”であることです。シミュレーションがどれほど精密でも、実機がプログラム通りの加工精度を発揮できなければ、ものづくりは成り立ちません。そのため、オークマは何より“機械精度のつくりこみ”を重視し、開発から機械・電気・制御部門が一体となって製品づくりを行っています」と。
まさに、それこそがものづくりの本質であり、基本中の基本と再認識させてくれた。