PRODUCTS
- Wide Y-axis travel balanced with excellent workability
- Ideal work envelope for medium and large-size parts machining
-
Y-axis travel : 1,050mm
For medium and large parts, and large plastic mold manufacturing, with 800mm table, and 1,050mm Y-axis travel
Best-in-class floor space productivity- X-axis travel : 1,600mm
- Y-axis travel : 1,050mm
- Table size : 1,600×800mm
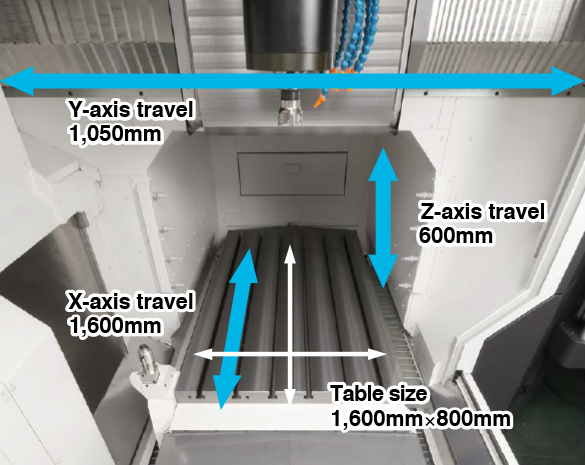
- Outstanding table and spindle access provide excellent workability
-
Easy access to table and spindle
- Access to spindle : 220mm
- Access to table : 345mm
- Table height : 900mm
- Front door opening : 1,620mm
-
Max workpiece
- Size : 1,600 × 800 × 600mm (L × W × H)
- Load mass : 2,500kg
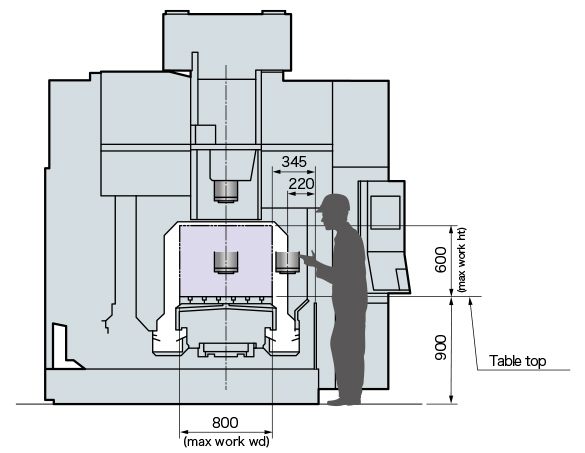
- Highly efficient machining of die/mold and
semiconductor manufacturing equipment parts
- Wide spindle lineup provides the right match for general machinery
to die/mold and aluminum parts applications -
Wide-range spindle (No.40)
Highly efficient general machine part applications
- Spindle speed : 15,000min-1
- Max output : 26/18.5kW (10 min/cont)
- Max torque : 199/146N - m (5 min/cont)
Tool | Spindle min-1 |
Cutting m/min |
Feed rate mm/min |
Width mm |
Depth mm |
Chips cm3/min |
---|---|---|---|---|---|---|
ø100 face mill 5 blades (carbide) |
955 | 300 | 1,429 | 70 | 4 | 400 |
ø50 insert drill |
606 | 95 | 90.9 | - | - | - |
Tap M30P3.5 |
240 | 23 | 840 | - | - | 84%(Spindle load) |
(material : S45C)
Tool | Spindle min-1 |
Cutting m/min |
Feed rate mm/min |
Width mm |
Depth mm |
Chips cm3/min |
---|---|---|---|---|---|---|
ø63 face mill 5 blades (carbide) |
15,000 | 2,969 | 8,523 | 44 | 4 | 1,500 |
(material : A5052)
-
High-speed spindle (No.40)
Mainly for aluminum (Optional)
- Spindle speed : 20,000min-1
- Max output : 30/22kW (10 min/ cont)
- Max torque : 57/42N - m (10 min/ cont)
-
Power spindle (No. 40/50, roller bearings)
Roughing and finish of dies&molds(Optional)
- Spindle speed : 12,000min-1
- Max output : 33/26kW (10 min/ cont)
- Max torque : 302/148N - m (10% ED/cont)
Tool | Spindle min-1 |
Cutting m/min |
Feed rate mm/min |
Width mm |
Depth mm |
Chips cm3/min |
---|---|---|---|---|---|---|
ø100 face mill 5 blades (carbide) |
955 | 300 | 1,910 | 70 | 5 | 669 |
ø20 roughing end mill, 7 flutes (carbide) |
4,000 | 251 | 9,520 | 20 | 3.7 | 704 |
(No. 50 high power spindle, material: S45C)
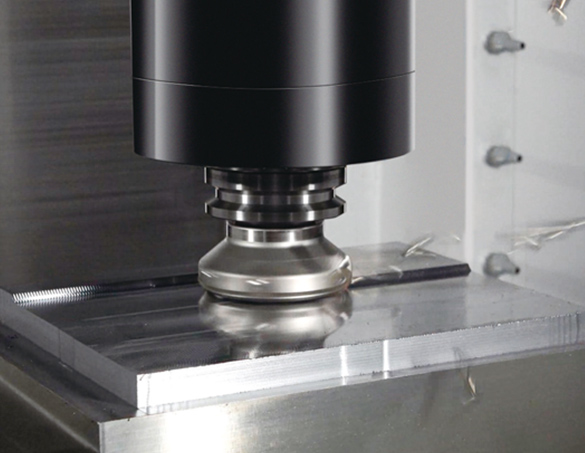
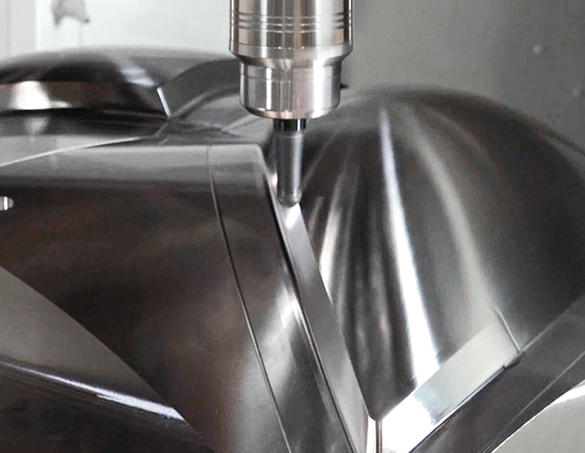
Delivering longer unattended operations
Large amounts of aluminum chips also cleanly removed
- Wide in-machine chip conveyor
- Crossrail shower system (Optional)
- In-machine vertical covers prevent chip accumulation
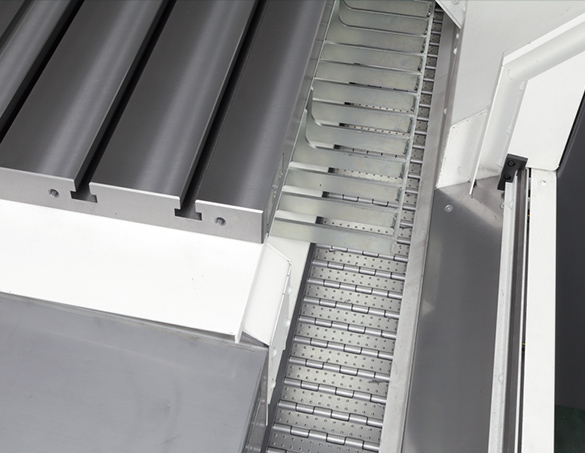
Large chip volumes discharged smoothly
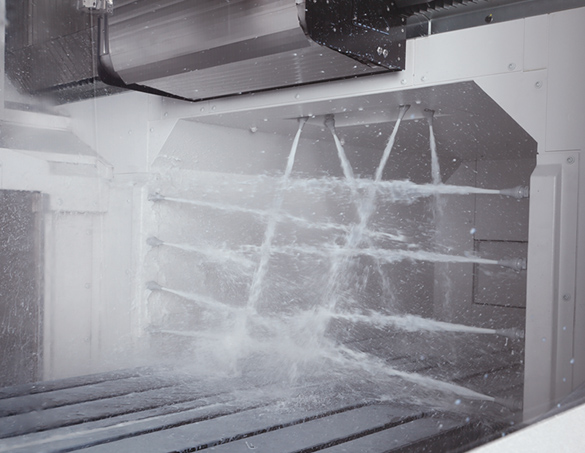
- “Working with temperature changes”
Thermo-Friendly Concept -
The “Thermo-friendly” concept enables remarkable machining accuracy through original structural design and thermal deformation control technology.
If frees you from troublesome dimensional compensation and warm-up. Exhibits excellent dimensional stability even during consecutive operation over long periods and environmental temperature change in the plant.
- Achieving high die/mold surface quality machining
Hyper-Surface (Optional) -
Auto machining data compensation, easy and improved die/mold surface quality
Modifying CAM machining data is not required.
Ridgelines and uneven surface edges are reduced,the machined surface quality is improved, and hand-polishing times are eliminated. In addition to the Sculptured-Surface Adaptive Acceleration Control featured in the previous Super-NURBS function, the new Hyper-Surface — while maintaining the required shape accuracy — automatically compensates for those edges and adjacent cutter path positioning errors caused by remnants of “disturbances” found in the CAM machining data.
Highlighted Specs
Item | Unit | MB-80V |
---|---|---|
Table size | mm (in) | 1,600 × 800 (62.99 × 31.50) |
Spindle speed | min-1 | 15,000 / 12,000 |
Tool storage | tools | 32 |
Motor | kW (hp) | 26/18.5 (35/25) (10 min/cont) 33/26 (44/35) (10 min/cont) |
Machine size (W × D × H) |
mm (in) | 4,500 × 2,970 × 3,320 (177.17 × 116.93 × 130.71) |