The design concept of our double-column machining centers
The spirit of a double-column machining center is in its details
- TOP
- The design concept of our double-column machining centers
High speed, high accuracy and high rigidity
required for the machining of large parts
In the machining of large parts, it is not easy to maintain high accuracy or increase productivity. While typical examples of machined items include key parts of automobiles, aerospace and semiconductor manufacturing equipment, as well as large precision dies, many of the parts are made of difficult-to-cut materials or have complex shapes. Also, machining with a micrometer level accuracy is commonly required.
In addition, since setup changes for heavy items take time and labor, a key to the reduction of the lead time is to complete a high-mix, high-volume and high-quality machining operation with just a single setting.
The DCMCs used for such machining need to have sufficient rigidity to continue high-speed and high-accuracy machining over long periods, as well as a high level of technology to control the heat and vibration generated during long-run continuous operation.
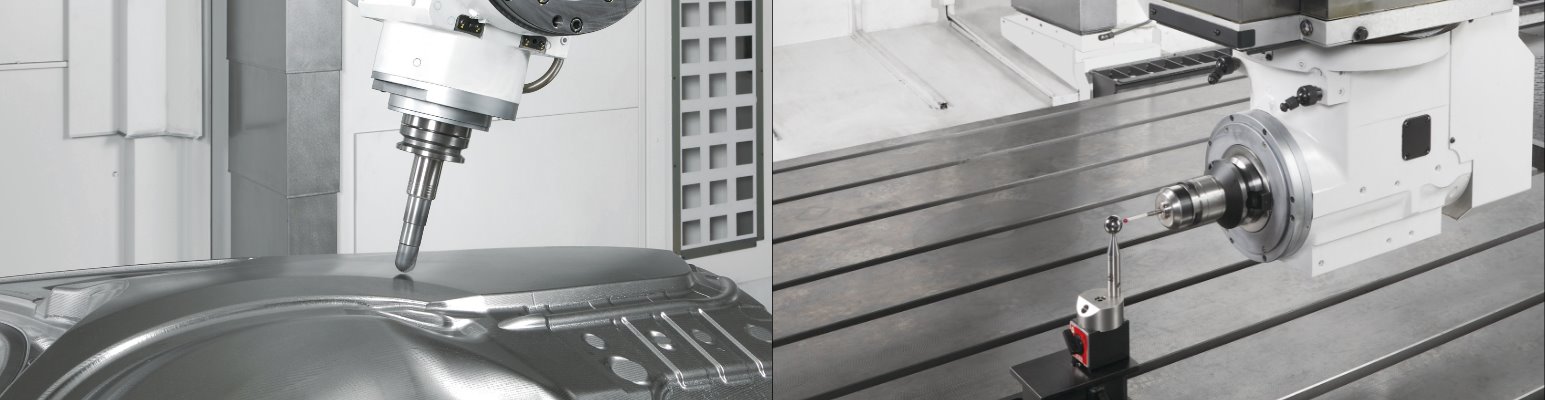
High specification achieved with a thorough
focus on detail
Since the development of its first DCMC in 1964 and unique 5-face machining applications in 1974, Okuma has worked to address head-on the challenges of machining large parts, and has provided successive innovative products developed with the knowledge acquired in its parts factories. We were able to achieve this by being thoroughly committed to manufacturing details.
For example, in the basic structure, the unique column and rib structure cope with strong torsional load in vertical and horizontal directions, while the elevating crossrail also has a structure designed for long-lasting accuracy with no lateral movement. The weight of the table and machined items is supported with roller bearings on the quenched and ground surface to ensure speedy and accurate positioning. In the assembly process, expert engineers finish the surface by hand scraping to ensure a perfect fit.
Our sincere commitment to the improvement of quality in this way allows us to provide a machining performance that competitors cannot provide, and helps establish unshakeable confidence in Okuma’s DCMCs.
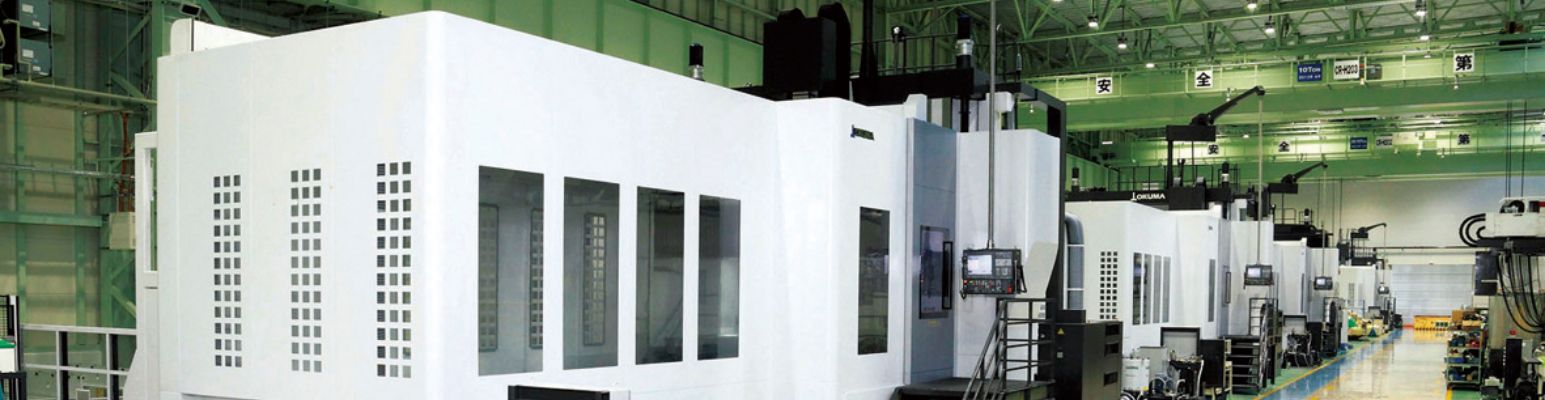
Pursuit of smart machining with a wide range of
Intelligent Technologies
While pursuing quality, Okuma also aims to integrate machines and control in an ideal manner. To this end, we have developed all the core parts, such as CNC controls, motors and encoders, in-house.
In recent years we went on to apply the TFC and various other intelligent technologies to DCMCs to achieve outstanding stability, protecting against thermal deformation, torsion, vibration, etc. We have also upgraded technologies to save labor and reduce the need for skilled workers, which has directly shortened lead time, such as automatic exchange of more than 100 types of attachment heads, automatic correction of machining programs to reduce the hand-finishing process of dies and automation of the calibration function essential for the maintenance of machine accuracy.
We are totally committed to the constant challenge of completing the machining of large parts as quickly as possible with a minimum number of steps. This is one reason why the cumulative sales of Okuma’s DCMCs throughout the world are approaching the milestone of 10,000 units.
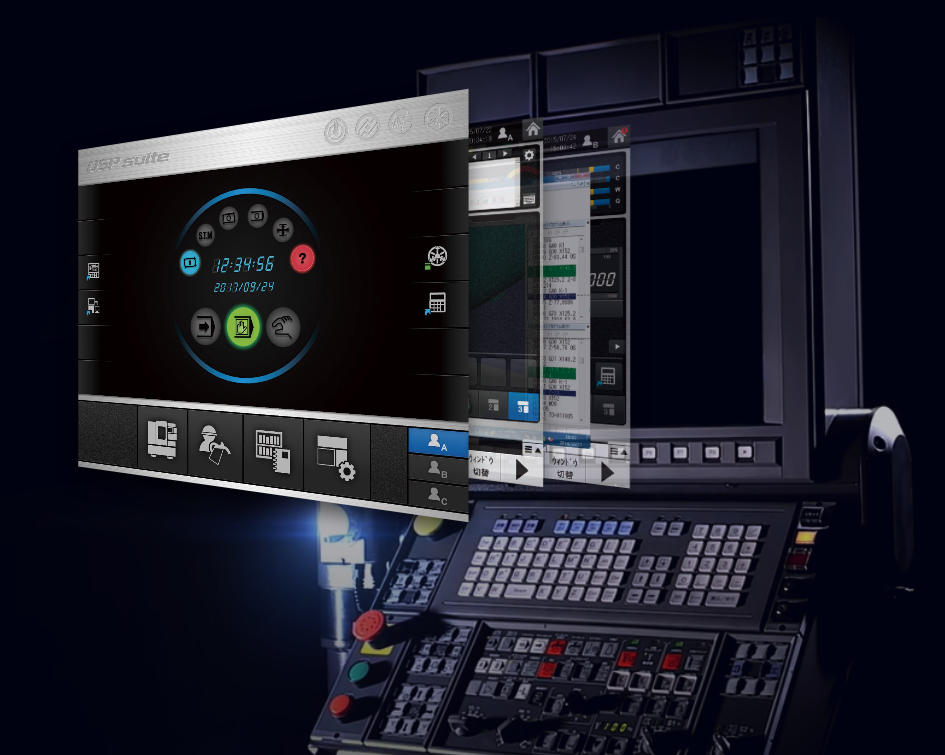