车床/复合加工机主轴生产中
毫不妥协的“精良制造”
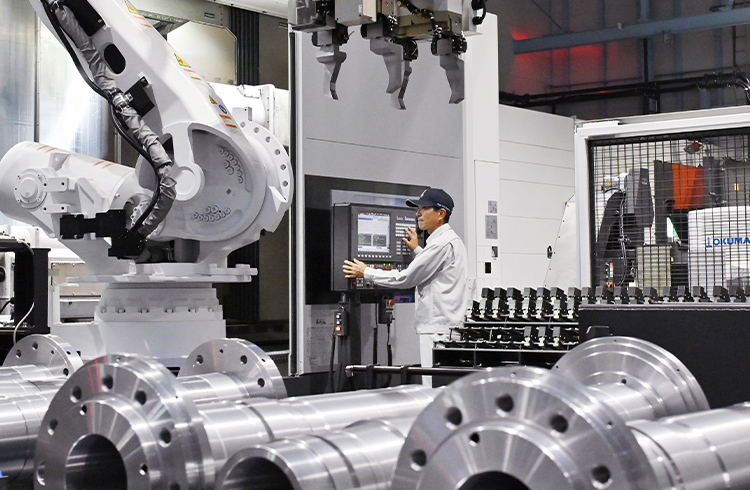
质量标准偏离1µm都被视为不合格
加入OKUMA公司后从事车床加工30多年,并被选为“爱知名工”的胜田佳裕(Yoshihiro Katsuda)说:“我觉得OKUMA对作为机床心脏的主轴制造的注重,似乎是在另一个水平。 ”他在所属的主轴加工部门磨练技能,从车床、加工中心、磨床、复合加工中心的本机主轴到龙门式加工中心的附加头和特殊刀具的安装主轴,负责过所有类型的主轴加工。
主轴制造工序分为:切割材料→锻造→车削粗加工→深孔加工→正火加工→车削精加工→机械加工→防碳、渗碳加工→粗磨削加工→精加工。在这个过程中,从材料的材质、热处理的方法、整直处理到最后的磨削加工,对于每道工序的关键点都制定了严格的质量标准和加工标准,并检查精度。
胜田表示:“质量标准偏离1µm都被视为不合格。在公司内部处理不完时偶尔也会寻求外包服务。但为了保证OKUMA的品质标准,最终的精加工一定在公司内部完成。 ”单元组装部门把这些完成的主轴和相关部件进行精密组装(详见本网站的CASE2),并安装在本机上。
为了制造可以保持高精度快速切削的机床
由于引进并不便宜的机床,所以希望它在快速切削的同时还能保持加工精度,为提高加工质量和生产效率做出贡献——这是我们所有客户的共同愿望。
然而,现实情况是“在同一台机床上同时使用粗加工和精加工时,会出现问题或故障” “重复重切削和轻切削时偏差明显” “为了工序整合想使用硬车削,但主轴可能无法承受”……这些问题可能是主轴和轴承等的加工和组装精度导致的刚性不足,或机床本身的结构导致的刚性不足造成的。
为防止这些问题的出现,OKUMA提供高刚性、高精度的机床,并将其作为设计和制造的基本理念,彻底实施严格的质量管理。
事实上,胜田曾被派到台湾的一家制造子公司,为亚洲地区的销售代理商和合作公司提供技术服务指导。至今他都忘不了从客户那里听到的话。 “经过10年的使用,OKUMA机床的高刚性、高精度的真正价值就显现出来了” “公司的经营状况随着OKUMA机床的引进而得到提高” “有朝一日我要引进目录封面上的5轴加工中心和复合加工中心”……。
客户们的每句话都是对包括技术大师在内的OKUMA全体员工的极大鼓励。
将技术大师的加工技术转化为智能化技术
说到OKUMA机床,以其高刚性、高精度著称的同时,也以其“智能化技术”闻名。规则热位移、不会撞机、不会振刀、自动调整至优化加工条件……这些支撑高精度、高生产效率的创新性加工基础功能,是将OKUMA加工现场培养的技术大师们的隐性知识(诀窍、直觉)进行量化和数字化控制的成果。
车削技术大师胜田以长尺寸工件中的振刀抑制为例进行了说明。“如果以相同转速切削一个长尺寸工件,不可避免地会发生振刀。但是,技工们可以通过评估工件的材质、形状和刀具,以及调整负载的施加方法和转速等来抑制振刀。将这种技术在NC控制中得以体现,并得出优化加工条件的就是‘Machining Navi’。”
此外,他还表示:“可以称之为智能化技术代表的 ' Thermo-Friendly Concept ',也是在高精度的部件加工和组装技术下才能实现的功能。由于机床根据环境温度和加工产生的热变化而 ' 规则变形 ' ,所以很容易控制。这就是为什么即使采用相同的机制,也无法达到与OKUMA机床相同的加工精度,因为机床的精良制造不同。”
从前辈到后辈、传承至今的OKUMA制造
成为技术大师的道路是怎样的呢?胜田说:“在被分配到的部门有一位前辈,后来被大家称为名工,我从他那里学到了很多东西。包括如何从图纸中得出最佳的加工工艺和步骤,丰富的知识和应用技能,以及快速准确的工作方法等。 ”可知,胜田不只学习了主轴加工,对前后工序的知识也是如饥似渴。在参与各种机型的同时,他还参与了交付机床的安装工作,提高了他作为一位多技能工的能力。
现在,基于这种经验,胜田作为“制造加工道场”的讲师,正在努力向骨干职员的实习生传授自己已掌握的技能。目标是使实习生通过国家技能测试合格率达到100%,并培养多技能工。为此公司也注重在内部技能竞赛中对年轻人进行加工教育,以提高他们的技能水平。
客户期望“有朝一日引进OKUMA的尖端机床”,为了提供超出客户预期的设备,年轻的实习生们努力在道场学习机床与工件的知识。
OKUMA的名匠
金属机床技工
胜田 佳裕YOSHIHIRO KATSUDA
- 1985年
- 入职株式会社大隈铁工所(即如今的OKUMA株式会社)
- 2000年~2001年
- 驻Tatung-Okuma Co. Ltd(台湾)
- 2007年~
- 爱知县技能测试 评审委员
- 2015年
- 被评选为“爱知的名匠”
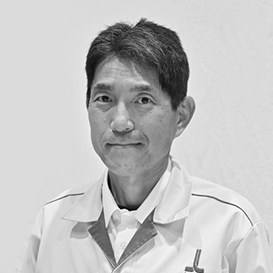