File 02
The best-selling machine that continues to evolve
MB-46V Ⅱ is the future of manufacturing
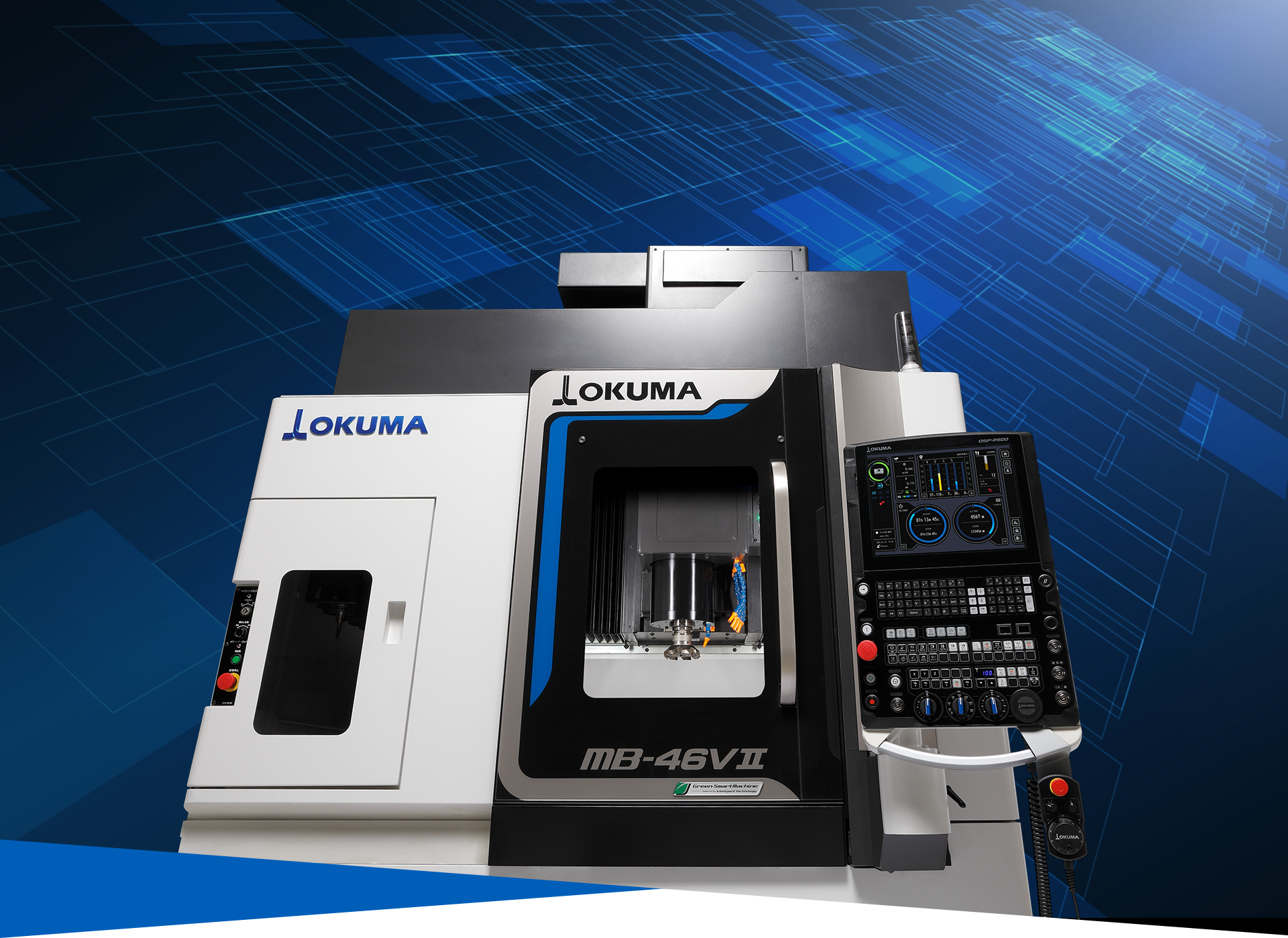
The MB-46V vertical machining center was released in 2001 and took the machining industry at the time by storm. What surprised people was the accuracy of its machining dimensional change over time of 8 μm and the revolutionary technology of the Thermo-Friendly Concept (thermal deformation control technology).
With a drastic reduction in the number of required compensation checks and a strong reputation for achieving high-quality machining without warm-up that had spread by word-of-mouth, the MB-V series became a bestseller with a cumulative sales of more than 11,000 units.
More than 20 years later, the MB-46V II was born. It inherited the DNA of the first generation, and was developed to address not only the current issues but also the future issues machine shops would face.
What kinds of challenges were encountered? Key people from each department talked about the challenges they faced.
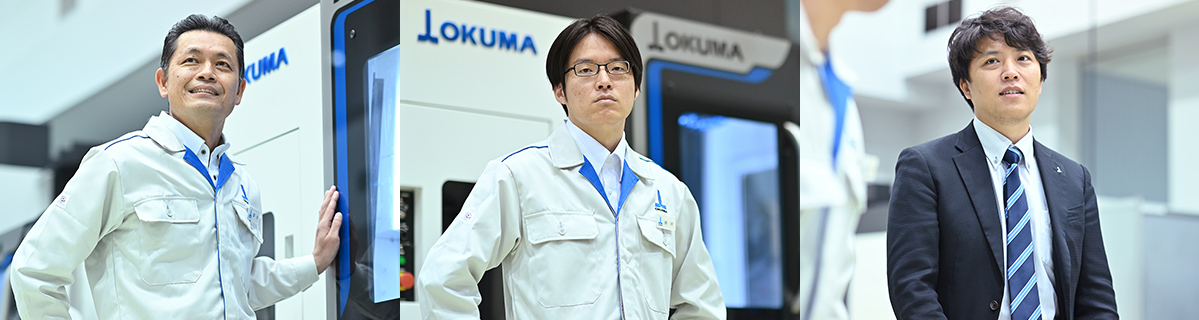
Kenji Omoya, Assistant General Manager, Solutions & Systems Engineering Department, Technology Division
Yasuki Izui, Project Leader, Projects-4, Product Development Department, Technology Division
Tatsuya Okazaki, Assistant Councilor, Section #2, Osaka Branch, Japan Sales Division
We wanted to reconsider everything from scratch, anticipate changes of the times, and deliver machines that lead the machining industry.

Development aiming to design machines
that solve social issues and
focusing on the future of full automationYasuki Izui, Product Development Department
"Since the MB-V brand was well established in the market, the basic structure and ease of use had to be maintained. At the same time, making only minor changes would not be acceptable. How could we make changes to the MB-46V, which was already a highly complete machine? We were at a loss at first." said project leader Yasuki Izui, revealing his feelings at the beginning of the project.
Tatsuya Okazaki, a sales representative who visits various customers, explains, "The MB-V has been used by large and small factories. It is highly acclaimed for features such as its dimensional accuracy that remains unchanged even after years of continuous use and the machine's design that makes it easy to operate from the front of the machine. Its compactness is also appreciated, especially in small factories."
However, after more than 20 years after its launch, the social environment surrounding the manufacturing industry has changed dramatically, and the issues faced by people engaged in metal machining have also become more complex.
When Okuma updates the models of its best-selling machines, it must respond quickly to these changes, anticipate new demands, and develop machines that lead the machining industry.
The development project decided to reevaluate every element from scratch, without being limited by previous evaluations. Looking back, Mr. Izui recalls, "We focused on the future of the manufacturing industry and kept in mind that we needed to develop a machine that solves social issues and can be fully automated." "If a machine could process workpieces more precisely, operators could just use the machine without being concerned about their level of experience or about particular characteristics the machine has. They could simply use the machine "normally" and manufacture products as desired. We want to deliver machines that are simple to use, rather than asking customers to be creative." he added, passionately describing the ideal situation for machine tools.
To meet customers' expectations for long, stable, and maintenance-free operation
The issues we identified made us realize once again that the industry and society was changing. "For example, we felt that as the number of workers in machine shops decreased, there would be a strong demand for machine tools that offered long, stable, and maintenance-free operation." said Kenji Omoya of the Application Engineering Department, who incorporates customer demands into product development.
At the same time, it is essential to reduce power consumption as the demand for decarbonization in the manufacturing industry increases. To achieve this, technology that can operate a machine efficiently using less energy is required.
The foundation for solving these issues was further development of the Thermo-Friendly Concept, which optimally controls thermal deformation.
While the first model achieved a machining dimensional change over time of 8 μm with a room temperature change of 8℃, the development team targeted a dimensional change of 5 μm, which was 38% better than the previous model. This level of performance is required for the machining of molds and the manufacturing of parts for semiconductor manufacturing equipment. Maintaining high-accuracy machining during extended periods of operation is required. This was an essential requirement for the next generation model of a best-selling machine.
The development team utilized structural analysis and endlessly worked to create a machine structure that would allow mounted tools to maintain a straight position at all times, even when temperature changes occurred during operations. After re-evaluating the shape of the castings numerous times and conducting countless tests of reshaped castings on actual machines, the development team achieved their goal.
As decarbonization is promoted throughout society, Okuma's energy-saving system "ECO suite plus" offers the perfect solution. The "ECO Idling Stop" system allows the machine itself to determine whether cooling is necessary or whether to temporarily stop the cooling system to reduce power consumption, but makes sure the machine maintains high accuracy machining at all times.
Regarding chip discharge, which has been a significant burden on machine shops, we provided the sludgeless tank. It collects impurities from the coolant and does not require the changing of coolant or cleaning of the tank for three years. (In-house test results)
The ATC shutter was also changed from a pneumatic system to an electric drive to increase the opening/closing speed, thereby drastically reducing tool change time and power consumption. Durability tests were performed for the open/close operation of the ATC door and results showed that the new ATC door was three times more durable than the previous model.
The MB-46V Ⅱ was also designed to make replacements of components and repair work easier, which minimizes machine downtime. The machine was made to be more durable and easier to fix.
CNC and robotic systems that even beginners can use
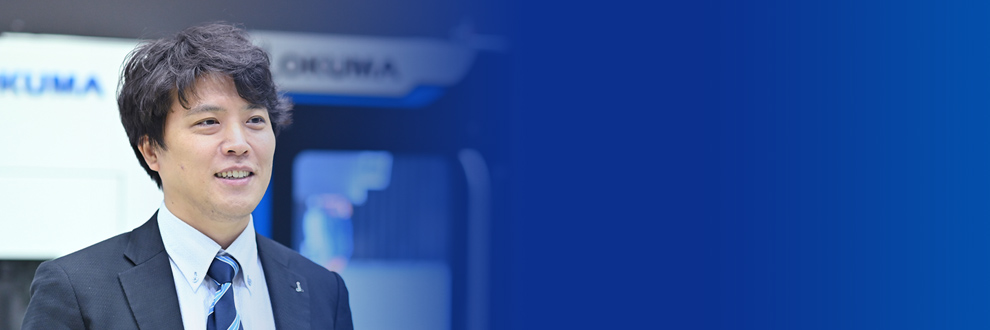
Having a guidance function that enables
you to do setup, programming, and machining
on your own is reassuringTatsuya Okazaki, Sales Division
The MB-46V Ⅱ has evolved dramatically through a variety of creative ideas, but not all issues can be solved by those ideas alone. It is also essential to have a control that uses digital technology and communication technology to coordinate with peripheral equipment.
The MB-46V Ⅱ is equipped with the next-generation CNC OSP-P500. This CNC has been receiving excellent reviews at exhibitions for its super-high-speed machining simulation generation time (with a maximin calculation speed of 1/1000 of the actual machining time) and its enhanced work procedure guidance functions that make operation easy even for novice users who have no knowledge about NC programs.
"With the number of skilled workers who can teach how to operate machines decreasing nowadays, it is reassuring to have a guidance function that enables you to do setup, programming, and machining on your own." Mr. Okazaki strongly emphasized,
Furthermore, the OSP-P500 can minimize trial-and-error when machining a part for the first time. Parts programs can be made on an office PC and then transferred to the machine after verification, which minimizes machine downtime. Because we are a machine tool manufacturer that develops NC controllers in-house, not only do we have highly precise control of axis movements, but we also have highly accurate control over the movement of peripheral units. This enables accurate simulation and precise machining of components.
While robots are effective when automating high-mix, low-/medium-volume production lines, the MB-46V II machining cell also addresses the social issue of declining labor forces. We provide a simple robot package, the STANDROID. It is compact in size and requires no specialized knowledge, which dramatically lowers the bar for installing robot operation. We also provide a movable collaborative robot that automates machine tools with a single touch when needed, according to the production volume.
"Contributing to society through the power of manufacturing services"
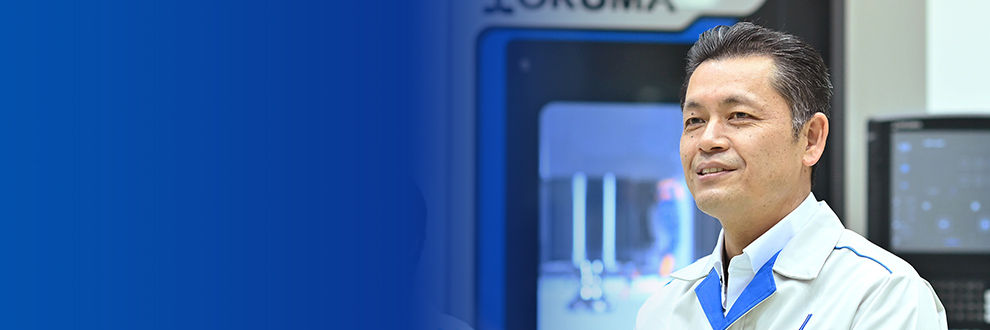
The MB-46V Ⅱ is a machine that
symbolizes the future of manufacturingKenji Omoya, Solution & System Technology Department
Okuma is clearly demonstrating its commitment as a solutions provider for machine shops in a changing society. Okuma not only improves the performance of individual machines, but also supports the transformation and optimization of entire factories.
Mr. Omoya shared his thoughts:
"The MB-46V Ⅱ is a machine that symbolizes the future of manufacturing. The Thermo-Friendly Concept and ECO suite plus are powerful tools for decarbonization, which is essential even for SMEs. Intelligent machine tools equipped with Thermo-Friendly Concept and ECO suite plus are defined as "Green-Smart Machines" by Okuma, and we have spread this through our machine lineup.
Furthermore, the next-generation CNC OSP-P500 is useful for issues such as decreases in skilled workers and labor shortages. Okuma is the only machine tool manufacturer that can optimally integrate mechanical, electrical, information, and intelligence technologies, which we have developed in our own machine shops, into one. This enables Okuma to make proposals that lead to optimization of entire factories, with an eye on the future of manufacturing."