File 01
From the high functionality of a single machine
to optimization of an entire factory
The future of manufacturing offered by the LB3000 EX Ⅲ
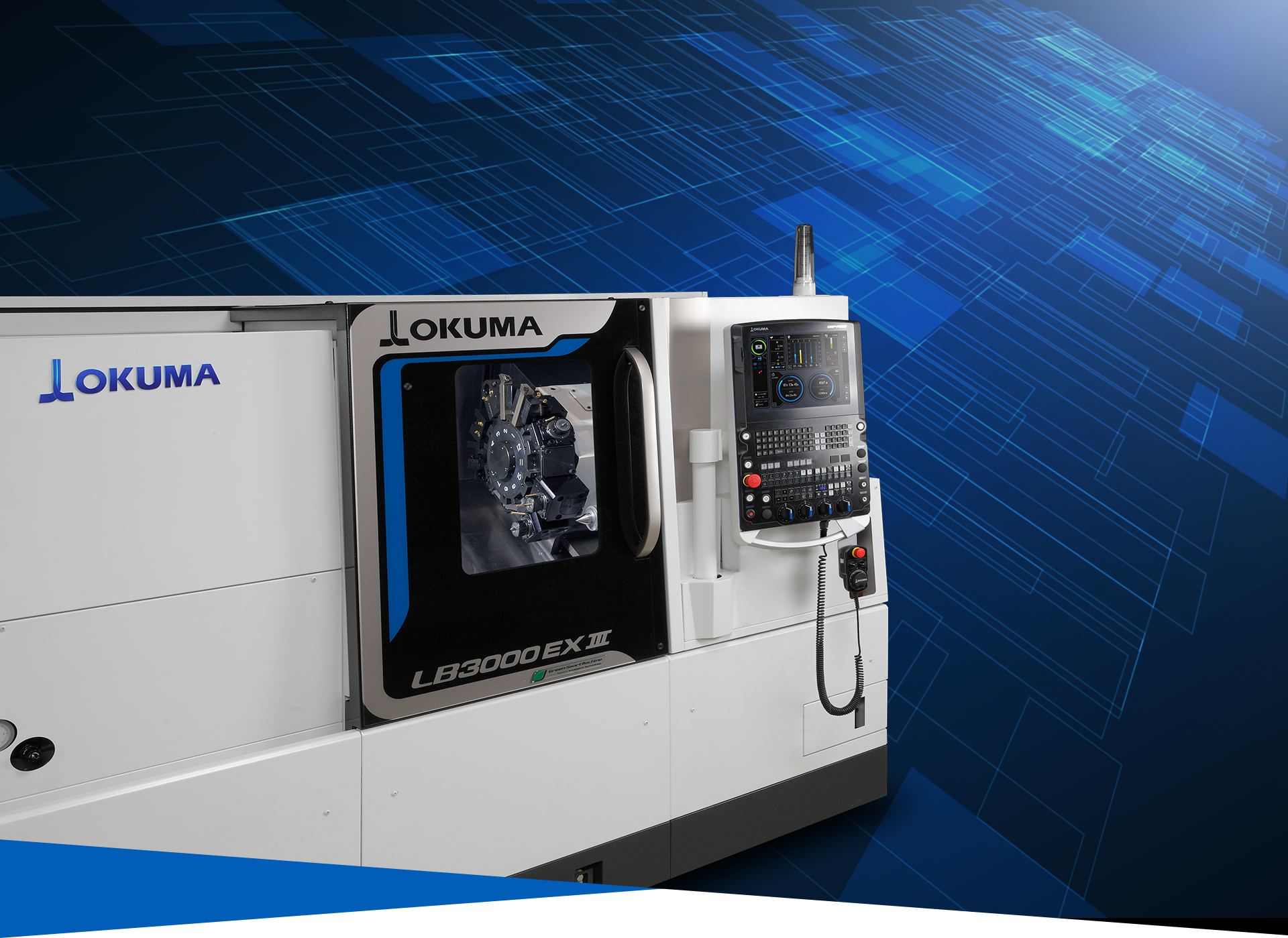
The LB EX series of CNC lathes are well-known for their compact size, heavy-duty cutting capacity, outstanding dimensional stability, and ease of use. The cumulative number of machines sold worldwide exceeds 18,000, making them one of Okuma's most popular models.
This best-selling machine was renewed for the first time in 11 years. Behind this is the response to issues faced by the manufacturing industry: decarbonization, digital transformation, labor shortages, and passing on skills to the next generation. The development team faced these needs head-on and created the LB3000 EX Ⅲ.
They were asked to talk about their thoughts that led them to that point and about the future of manufacturing.
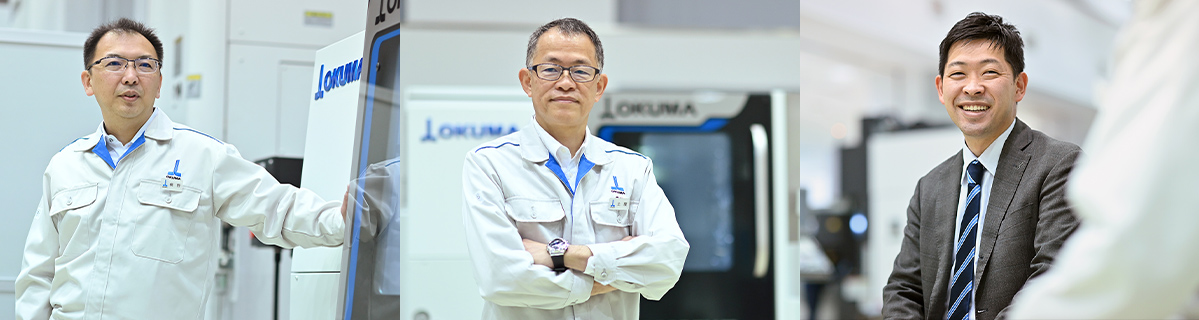
Makoto Kajino, Assistant General Manager, Solutions & Systems Engineering Department, Technology Division
Masashi Tsuchiya, Project Leader, Projects-3, Product Development Department, Technology Division
Yuki Kato, Sales Chief, Anjyo Office, Nagoya Branch, Japan Sales Division
How has this long-selling machine evolved?
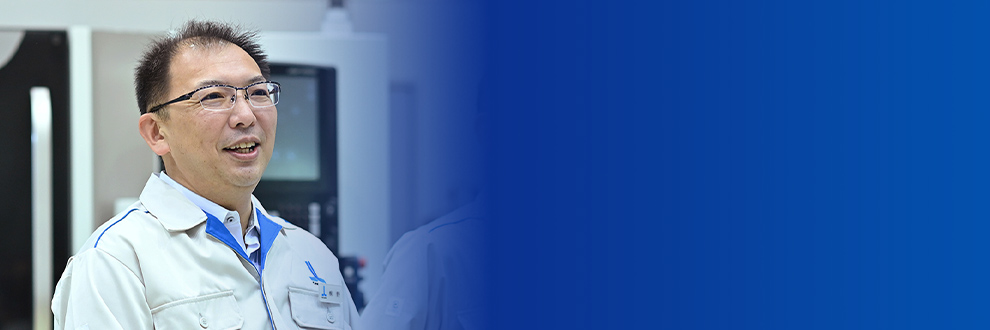
It is essential that a machine has
high accuracy and does not stopMakoto Kajino, Solution & System Technology Department
When talking about Okuma's lathes, many people refer to the "LB" series. This traces back to the LB15 model, which was created in 1982. At that time, the company aimed to achieve compactness, high durability, and affordable pricing in order to provide the optimal CNC lathe for a wide variety of customers in different industry sectors who had different company sizes, target workpiece sizes, and production volumes.
This later evolved into the LB300 in 1998 which adopted a slanted-box bed structure for low thermal deformation. After that, the LB3000 EX was released in 2006 which was regarded highly for its high accuracy machining, minimal machining dimensional change over time of ø5 μm, its high capability of complex machining, and its ability to do complete process integration without a chuck change. And then the LB3000 EX Ⅱ was introduced in 2012 which had further improvements made in operability.
"The LB has evolved over several generations, but our development approach—identifying the hidden needs of our customers and reflecting them in the performance of our products—and our pursuit of high rigidity, high productivity and compactness remain unchanged." asserts Masashi Tsuchiya. He has been involved in the development of successive generations of the LB series since the 1990s and also served as the project leader for the latest model, the LB3000 EX Ⅲ.
He emphasizes, "We never compromise when it comes to accuracy. Although weight reduction and integration of alternative parts are sometimes discussed to reduce costs, the Thermo-Friendly Concept (thermal deformation control), which is the key to accuracy, requires a certain amount of weight. Therefore, there are some things that cannot be compromised for structural reasons."
Makoto Kajino, a sales engineer in the lathe industry with extensive experience in bridging the gap between customers and technical departments, as well as in the set-up of mass production lines in the automotive industry and overseas assignments, adds the following.
"In mass-production factories, if a machine needs to be stopped repeatedly due to poor accuracy or because corrections must made, it will not earn trust. In this regard, the LB3000 EX achieved extremely stable machining accuracy because the Thermo-Friendly concept had been applied, and this resulted in a string of repeat orders from customers in the automotive industry. I worked at one of our sales offices in Germany for five years where I was responsible for the Europe, Africa, and Middle East regions, and I never heard any complaints about the accuracy of an LB. Of course automation and decarbonization are important, but the most important factor for a machine is having high accuracy and to not stop during machining."
Focusing on issues that factories may run into in the future
So, what kind of performance was required for the latest model? The development project collected and analyzed feedback from users in Japan and overseas through visits to the customer and marketing meetings. They then sorted through the current issues and also studied about future issues the factories may encounter. Through this process, the development project analyzed what would be the ideal form for a CNC lathe.
The conclusion they reached was: " As the number of workers and skilled craftsmen decrease, it is essential for a CNC to maximize factory utilization rates, achieve next-level process integration, and be capable of supporting diverse automation systems to meet strict accuracy requirements and pursue high productivity. Furthermore, machines appropriate for a decarbonized society should be equipped with environmentally friendly functions to autonomously save energy, and it should all be integrated compactly."
In an era of great manufacturing innovation, Okuma's goal is to become a solution provider for not only machine tools, but also to provide solutions for optimization of entire factories and factory management support.
A machine that remains true to the basics and is easy to handle
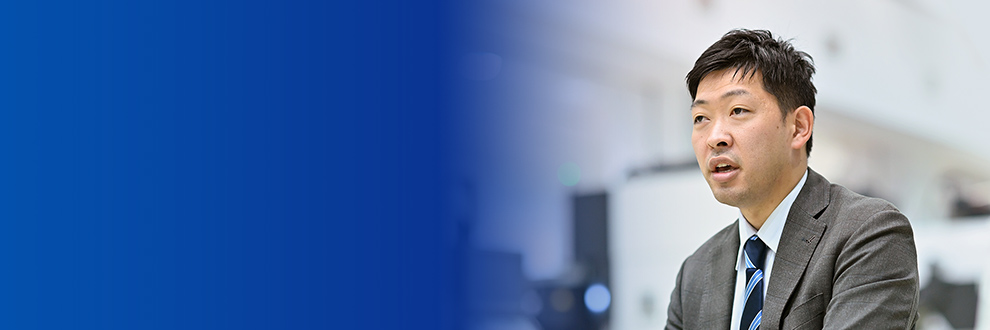
We want our customers to experience
the operability of the next-generation CNC
OSP-P500Yuki Kato, Sales Division
In March 2023, the long-awaited LB3000 EX Ⅲ was unveiled to the press.
At the unveiling, Mr. Tsuchiya explained his development approach saying, "As a prerequisite for promoting automation, manpower saving, and unattended operation, it is essential that a machine has stable machining accuracy and does not stop."
In an era in which workforces are decreasing, machines that can complete machining with the push of a button without any other interactions are being demanded. In addition to this, if various functions can be added to a machine (such as milling, gear cutting, and grinding) and a single unit is able to perform various complex processes, this machine can be used in high-mix, small-lot production lines. This new model embodies that.
In our pursuit of automation, we prepared easy-to-implement systems according to the type of production: loader systems suitable for mass production, space-saving in-machine robots (ARMROID), stand-alone articulated robots that can be automated after installation, etc. In particular, robots that used to be difficult to teach can now be programmed and moved with the same capacity as controlling a machine tool. This is made possible by ROID Navi. If you specify the start and end points, the ROID Navi automatically generates collision-free movement paths for the robot. As you can see, we have taken great consideration in providing ease of use everywhere. This allows the machine to be operated regardless of the operator's experience.
Proud of their product, the development team says, "Customers have been hesitant to adopt robots because of the heavy burdens of understanding robot languages, acquiring qualifications, training operators, and securing space for installation in addition to the capital investment. In this respect, Okuma's robots are also available as built-in types and can be operated in the same way as OSP, without the need for a system integrator. The sense of security is great, and you will be convinced that you can handle it."
Yuki Kato, who does businesses with a wide variety of machine shops as a sales chief, emphasizes, "We want our customers to experience the easy-to-use operability of the next-generation CNC OSP-P500."
Some customers found the previous OSP control to be difficult to use because you had to frequently switch between screens, but the OSP-P500 requires fewer screen changes, making operation more convenient. Also, as the number of technicians who can teach others to operate machines decreases, the ability for a CNC control to provide guidance from setup to programming and machining is very helpful."
OSP-P500 can minimize on-site trial-and-errors when machining a part for the first time and maximize machine utilization rate. This is because parts programs can be made and pre-simulated in advance on an office computor before being transferred to the machine. The simulation function is extremely accurate, with a maximum calculation speed of 1/1000 of the actual machining time, and error of less than 1% of the machining time.
"If the operator's work time can be reduced, the machine's utilization rate will increase. If productivity is increased in this manner, power consumption per workpiece can be reduced, leading to decarbonization. Without a doubt, this kind of smart operation will spread thoughout the industry." says Mr. Kato.
Reduce power consumption while maintaining high accuracy and productivity
Efforts toward decarbonization are accelerating around the world today, but what about in machine shops?
"Decarbonization was an issue mainly for large companies until around 2020, but primary and secondary companies that form supply chains are now also included. In particular, interest in power consumption has been growing recently due to soaring electricity prices." says Mr. Kajino.
Okuma has been offering a solution to this issue for over 20 years. That solution is the Thermo-Friendly Concept, which optimally controls thermal deformation. Superb dimensional accuracy was achieved through reverse thinking. Rather than forcibly cooling the machine, Okuma designed the structures of the machines so heat (thermal deformation) could be easily controlled. This resulted in minimizing the energy used for warm-up and air conditioning. Okuma's products that apply this technology can achieve high accuracy and high productivity while commiting to saving energy (reduction of carbon dioxide emissions).
In recent years, this technology has been applied to reduce power consumption by allowing the machine to determine when cooling is necessary to maintain accuracy and when it is not needed (ECO suite plus). Furthermore, power consumption has been reduced for the LB3000 EX Ⅲ by changing from pneumatic to motorized opening and closing of the front door, along with other means. In this way, Okuma is fully developing machine tools as Green-Smart Machines that autonomously achieve both stable dimensional accuracy and reduced energy consumption.
The foundation for everything is establishing machining accuracy
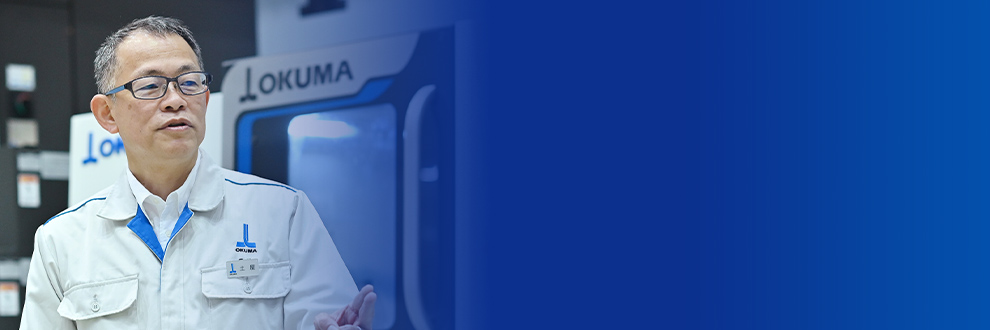
Always keeping "establishing machining
accuracy" as our main priority, Okuma's
development, mechanical, electrical, and
control departments work together to
develop products.Masashi Tsuchiya, Product Development Department
The LB3000 EX Ⅲ has evolved remarkably in terms of productivity, multitasking machining, digitalization, and automation. Mr. Tsuchiya, the project leader, concluded with the following remarks about the essence of machine tools.
"DX and IoT have been attracting attention in recent years, and digital technology has also been widely deployed in machine tools. However, we must not forget that it is the machine that processes the metal. No matter how precise a simulation is, manufacturing is not possible unless the actual machine can achieve the machining accuracy as programmed. Therefore, Okuma emphasizes establishing machining accuracy above all else, and the development, mechanical, electrical, and control departments work together to develop products."
This is the very essence of manufacturing, and it reminded us of the most basic of the basics of manufacturing.