主要单元所有精度均数值化,
并进行严格管控。
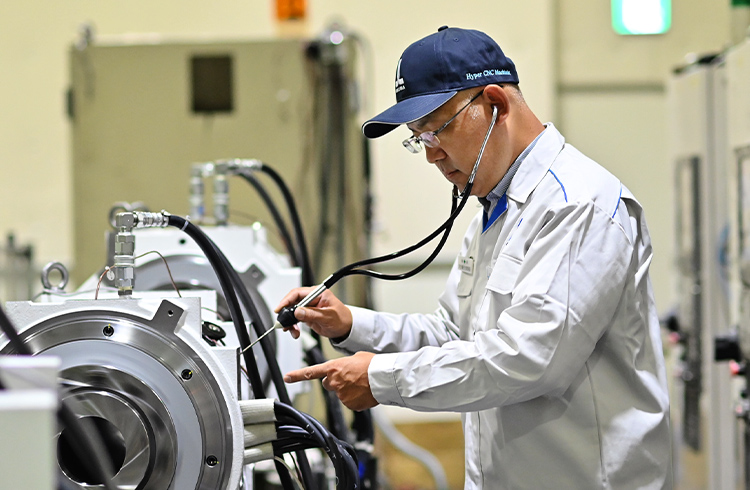
µm级单位数字交融在一起,监测听不到的振动。
机床的心脏部由主轴台、刀架、尾座等主要单元组成。其组装现场“1”、“3”、“5”等数字交织在一起。这是零件精度、装配精度或装配零件实际装配作业中的“旋紧余量”等数值,单位均为微米(µm:1/1000mm)。在此,这就是标准。
车床和复合加工中心单元组装的领军人物户崎 隆(Takashi Tozaki)说:“即使按照设计加工零件,在组装阶段也会出现几微米的误差。根据订单规格进行微调使其发挥最大性能是单元组装的工作。因此,我们频繁在现场使用测量仪器,一边检查数值一边进行作业。高端机型和普通机型的严谨性是一样的,我们对任何机床都追求最高的装配精度。”
对于影响主轴旋转稳定性的振动,在支撑主轴的主体上安装传感器,并仔细测量人耳无法听到的频率。如果检测到异常频率,会对作为发生源头的轴承内部的滚珠、滚子和轨道表面采取措施。
过去,熟练技工习惯于用耳朵去听主轴转动的声音判断其是否正常。这种技术仍然被传承,有时会将听诊器放在机床上诊断旋转的声音。通过这种方式,OKUMA将最新的测量仪器与经过历练的五感技能相结合,将高质量融入各生产环节。
发挥杰出的技能,满足海外用户需求。
许多在日本积累一定经验的技术人员希望去OKUMA海外公司任职,经过领导推荐,被派遣到OKUMA海外公司。
后来成为技术大师的户崎就是其中一员。拥有国家技能考试的“精加工”、“机械维修”和“机床加工”资格认证,并具有丰富的主要单元组装和维修经验,1998年至2005年被派遣到OKUMA欧洲(德国)公司任职。主要任务是指导当地销售代理商的服务人员进行复合加工中心的精度校正、主轴的装配和维修技术等。
但是,OKUMA欧洲公司管辖范围广大,遍及欧洲、非洲部分地区和中东国家,在机床故障原因不明或需要高度技术进行紧急维修时,户崎需要亲自前往客户的工厂进行对应。
户崎遇到了各种紧急事件,但最难忘的是船用发动机制造商的事件。当时,几年前交付的大型5轴加工中心出现故障,现场陷入困境。户崎赶到后,经过数日检查但未能查明原因。后来,注意到刀具更换装置的零件与平时看到的零件不同,尝试拧松该零件的安装螺栓后,加工异常就消失了。
户崎询问零件的来源时,厂方说:“几周前,由于机床内发生故障,刀具脱落,安装零件变形,所以该公司自己做了一个替代零件。” 仔细检查后发现,“零件组装时的准心校对”不理想,故障原因是无法发挥出原有的切削能力。厂长对户崎的观察能力非常感慨,亲自送他去机场。
“查明原因,解决问题”是他的原则,这是反映他的坚定信念和使命感的一个小插曲。
培养工匠精神的传统和企业文化
卓越的技术和技能不是一蹴而就的。OKUMA自1939年成立“技术人员培训中心”以来,一贯坚持培育以高技术和高技能为目标的企业文化,从开发设计到制造和售后服务,已渗透到各个部门的每一个角落,引领创新的产品开发,形成追求高质量的土壤。
最重要的是,自1964年以来,每年为在公司工作不到10年的员工举办的“OKUMA技术技能大赛”上,许多员工挑战高于国家技能考试的水平。这是展示日常钻研技术的成果并传承技术和技能的场所。
在这样的企业文化中,1000多名技术人员通过了国家技能测试,其中19人是被评为日本“制造王国”爱知县“名工”认证的技术大师。我们培育出8名被评为“现代名工”的顶级技术大师(截至2022年9月)。
将技术知识可视化,在制造道场传承技能。
OKUMA不仅专注于培养技术人员。技术大师们将从前辈继承或自己开发的专有技术等技能转化为数据(文字化、图纸化、手册化)并与各部门共享,应用于改进产品功能,并用于改进工序等,努力使技能价值最大化。
此外,2007年在公司内设置的“制造道场”,员工根据入职年份和技能水平分组,在技术大师的指导下,从基本制造技术的掌握到加工和组装的高级技能,通过反复练习达到手上工具运用自如的境界。
其目标是“培养多面手”,不仅在专业领域,而且在外围设备和NC设备方面拥有广泛的知识和技能。
OKUMA开发和制造各种机床,以及公司内部的NC设备和自动化系统,因此需要可以全方位对应的人力资源。这也是支撑OKUMA品牌信任背后的驱动力。
OKUMA的名匠
金属加工机床装配工
户崎 隆TAKASHI TOZAKI
- 1991年
- 入职OKUMA株式会社
- 1998年~2005年
- 驻Okuma Europe GmbH(德国)
- 2017年
- 被评选为“爱知的名匠”
- 2017年~
- 爱知县技能测试 评审委员
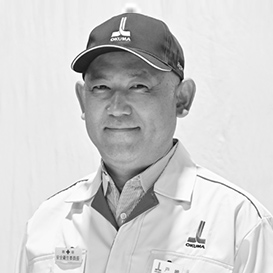