Machining CenterMachines are alive:
hone your five senses to respond
to their changes
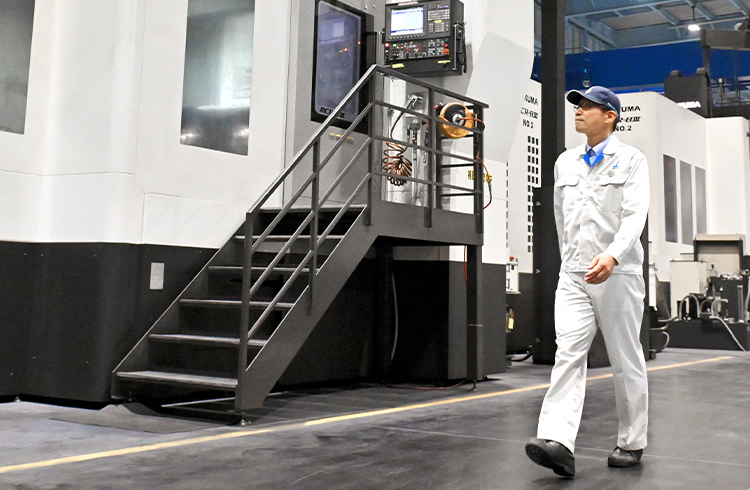
Whether engine parts for sports cars,
banknote printing machines,
or large diameter pipes for oil fields …
Selected as a certified Master Craftsman by Aichi Prefecture (called the "Manufacturing Kingdom" in Japan) in 2017, Katsumi Sumitaku has been handling an array of difficult machining since joining Okuma in 1983.
In his first work assignment, he learned the principles, concepts, and basic techniques of metal working while operating general-purpose boring machines. It was a workplace in which he saw a steady stream of work coming in that involved difficult-to-cut parts, such as parts processing for rotary knitting machines produced by Okuma at that time. These parts had special shapes that could not be handled by machining centers.
Mr. Sumitaku continued to hone his machining and other skills after that and was involved in the manufacture of banknote production equipment that required rigorous dimensional accuracy and in the manufacture of milling machines for large-diameter pipes used in U.S. oil fields. To put this into perspective, the machining accuracy required at that time for a headstock with an inner diameter of 930 mm was strict, with perpendicularity and roundness tolerances of only 3 μm.
He also struggled with other parts that had strict thread misalignment tolerances of within 1 μm despite them being small parts, and he was later told that they were parts of machines for manufacturing engine parts for the world's finest sports cars. That manufacturer still uses Okuma grinders to machine certain critical parts. These achievements have attracted attention from FI racing engineers, and Okuma's machines are used to machine engine parts for race cars that contend over the boundaries of speed.
Machines are alive:
hone your five senses to respond to their changes
"Machines are alive. Even the most sophisticated machines change with the environment and time. Machine operators need to hone their five senses, sense the changes, measure them with precision measuring instruments, and correct the commanded values in the machine; otherwise, satisfactory machining accuracies cannot be obtained." This is the machining philosophy Mr. Sumitaku, a master craftsman, heard repeatedly from older generations of staff who taught him and that he continues to convey to younger staff.
The following is an example of a situation that illustrates the greatness of such skilled workers. Mr. Sumitaku was consulted one day by a junior employee in the parts machining department, who said, "I am having trouble achieving the machining accuracies required for large parts." Thinking about the air flow in the machine shop, he offered the following advice: "Machines deform slightly due to the temperature difference between the bed and headstock. Install a thermometer above the column and under the bed, measure the temperatures there for 1 month, graph them, and determine the degree of deformation. Then, you should be able to achieve them if you apply corrections based on that data to ensure perpendicularity to holes made in 3-axis machining." A month later, he was contacted by the junior employee, who said, "I achieved the machining accuracies. Thank you."
Mr. Sumitaku continues to teach the importance of "understanding the peculiarities of each machine" and "machining parts after learning about the structure and characteristics of each machine."
In the Monozukuri Dojo, new employees cut dice-shaped workpieces in the morning and afternoon with the same machines to compare the finish accuracy so that they can gain experience with the characteristics of metals. Since changes arise in general-purpose machines in just a few hours, trainees seem uniformly surprised by them.
Transfer of know-how from the machine shop to design and bringing design knowledge to the machine shop
At Okuma, monozukuri is achieved through close cooperation between the product development and design department and manufacturing department such as parts machining and assembly. This is a corporate culture that has been cultivated traditionally and passed down from one generation to another to this day.
Based on his own experience, Mr. Sumitaku says, "Based on my many years of machining experience, it is possible to read drawings and see how changing certain points results in improvements, such as preventing vibration or making assembly easier while maintaining rigidity. Providing feedback to the design department is also an important role for us. On the other hand, the machine shop can acquire knowledge and wisdom through exchanges with the design department and further improve our skills." For example, cavities in certain spots may resonate when cutting workpieces. In addition, attachments of double-column machining centers (5-face machining centers), which can switch between more than 100 different spindle heads, may cause vibration when machining curved or inclined surfaces if there are any spots where the rigidity is insufficient. These observations are proffered to the design section at drawing review meetings and/or in the prototyping stage to ensure that we thoroughly adhere to the fundamental principles of Okuma machines: high rigidity and high accuracy.
Because we consistently do this throughout the entire process in Japan, from development to shipping, we are able to confidently deliver the highest level of products to our customers.
Bringing Okuma's machining know-how to customers
In NC programming, there are machining programs called macros that make it possible for operators to handle a wide range of workpieces by simply changing variables, without the need for complicated input. Among skilled workers, there are many who create their own macros by converting their personal machining experience and tacit knowledge (know-how and intuition) into programs.
Mr. Sumitaku, a master and outstanding multiskilled worker, is one of them. He has created a number of macros that have been used to improve machining efficiency and develop OSP software for Okuma CNC machines. Okuma's machines, recognized by customers as easy to use, are the result of the know-how of master craftsmen like him.
Mr. Sumitaku's outstanding skills and knowledge are used not only in the manufacture of Okuma's products but also to support National Trade Skills Testing & Certification and to support the World Skills Competition, where young skilled workers from all over the world compete by displaying their skills, thereby contributing to the development of human resources for the next generation.
Master Craftsman of Okuma
Metalworking machine-tool mechanic
KATSUMI SUMITAKU
- 1983
- Joined Okuma Iron Works Ltd. (current Okuma Corporation)
- 2006 —
- Aichi Prefecture Trade Skill Testing & Certification, Trade Skill Test Commissioner
- 2017
- Selected as a Master Craftsman in Aichi
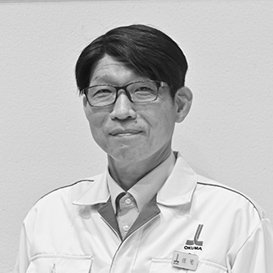